How Lean Six Sigma Process Mapping Streamlines Workflows
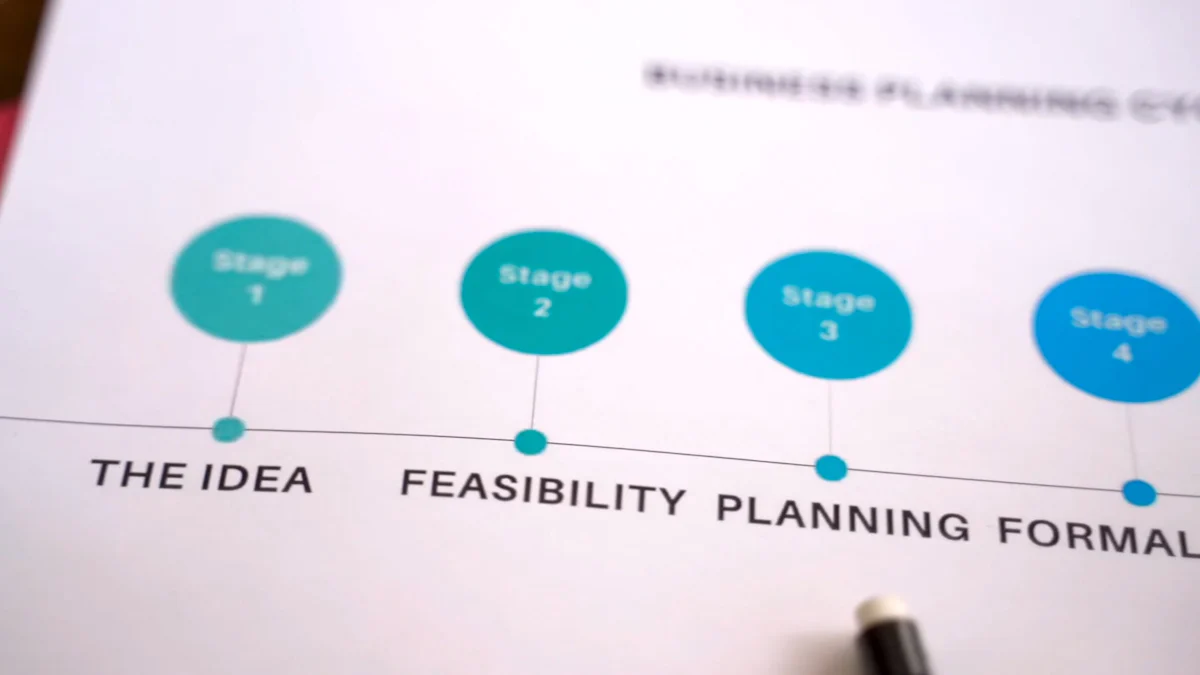
Lean Six Sigma process mapping helps systems and teams visualize workflows and uncover inefficiencies. It empowers organizations to implement targeted process improvement strategies that enhance productivity. By focusing on optimization steps, businesses can reduce waste and improve outcomes for clients and customers. This approach combines clarity with actionable insights, enabling teams to streamline operations and achieve measurable results.
Key Takeaways
Lean Six Sigma process mapping shows workflows clearly to find problems.
It mixes Lean's waste-cutting with Six Sigma's focus on quality for better results.
Tools like SIPOC and value stream maps explain roles and improve teamwork.
Finding and removing waste saves money and boosts productivity.
Involving everyone in mapping builds teamwork and shows real workflows.
Making a perfect process map helps teams see better workflows.
Checking maps with data often keeps them correct and improves processes.
Simple maps are easier to understand and help teams make changes well.
Understanding Lean Six Sigma Process Mapping
What is Lean Six Sigma Process Mapping?
Lean Six Sigma process mapping is a structured method for visualizing workflows and understanding how tasks, resources, and decisions flow within a system. It provides a clear picture of the current state of a process, enabling teams to identify inefficiencies, redundancies, and bottlenecks. By documenting each step, systems and teams can uncover opportunities for improvement and create a roadmap for achieving operational excellence.
This approach integrates the principles of Lean and Six Sigma to ensure processes are both efficient and consistent. It emphasizes reducing waste, improving quality, and fostering collaboration among stakeholders. Process maps serve as a shared visual language, making it easier for teams to align on goals and implement changes effectively.
How it Combines Lean and Six Sigma Principles
Lean and Six Sigma principles complement each other in process mapping. Lean focuses on eliminating waste and creating value, while Six Sigma aims to reduce defects and variability through data-driven analysis. Together, they provide a comprehensive framework for process improvement.
Lean tools, such as value stream mapping, help identify non-value-adding activities and streamline workflows.
Six Sigma tools, like the DMAIC process, guide teams in systematically analyzing and optimizing processes.
Combining these approaches accelerates results by addressing inefficiencies and defects simultaneously.
For example, a team might use Lean principles to remove unnecessary steps from a process and then apply Six Sigma techniques to ensure the remaining steps produce consistent, high-quality outcomes. This integration creates a balanced approach that prioritizes both speed and accuracy.
Role in the DMAIC Framework
Lean Six Sigma process mapping plays a vital role in the DMAIC process, which stands for Define, Measure, Analyze, Improve, and Control. Each phase leverages process mapping to achieve specific objectives:
DMAIC Phase | Role of Process Mapping |
---|---|
Define | Visualizes the current process to establish a baseline and identify improvement opportunities. |
Measure | Highlights critical inputs and outputs, helping teams understand variability and performance gaps. |
Analyze | Pinpoints bottlenecks, redundancies, and root causes of inefficiencies. |
Improve | Simulates potential changes and visualizes the ideal-state process for better decision-making. |
By aligning process mapping with the DMAIC framework, systems and teams can systematically address inefficiencies and implement sustainable improvements. This structured approach ensures that changes are data-driven and aligned with organizational goals.
Benefits of Lean Six Sigma Process Mapping
Visualizing Workflows for Clarity
Lean Six Sigma process mapping provides a clear and structured way to visualize workflows. By creating a detailed representation of each step in a process, systems and teams can better understand how tasks flow and where inefficiencies may exist. This clarity allows stakeholders to align on goals and identify areas for improvement.
The measurable benefits of visualizing workflows include improved efficiency, enhanced quality, better communication, and data-driven decision-making. The table below highlights these advantages:
Benefit | Description |
---|---|
Improved Efficiency | Process mapping helps identify inefficiencies and streamline workflows, leading to reduced cycle times and enhanced productivity. |
Enhanced Quality | By identifying sources of variability, process mapping aids in reducing defects and ensuring consistency in outcomes. |
Better Communication | Visual representations foster a shared understanding among team members, reducing misunderstandings and promoting alignment. |
Data-Driven Decision-Making | Integrating measurable metrics into workflows allows teams to make informed decisions that drive continuous improvement. |
By leveraging these benefits, organizations can use lean six sigma process mapping to create a foundation for effective process improvement.
Identifying and Eliminating Waste
One of the core principles of Lean Six Sigma is the elimination of waste. Process mapping plays a critical role in identifying inefficiencies and waste within workflows. By visually representing each step, teams can pinpoint redundant tasks, delays, or unnecessary actions. This analysis helps optimize resources and streamline operations.
For example, process mapping allows project managers to uncover unnecessary steps that slow progress. It also highlights areas where resources are underutilized or misallocated. These insights lead to cost savings and better resource management.
The goal is to identify and eliminate wasteful steps and ultimately optimize the value delivery process by exploring more efficient ways to get the job done.
Through this approach, systems and teams can focus on delivering value to clients while reducing operational costs and improving overall efficiency.
Enhancing Team Collaboration and Communication
Lean Six Sigma process mapping fosters collaboration by providing a shared visual language for teams. When workflows are clearly mapped, team members can better understand their roles and responsibilities. This clarity reduces misunderstandings and promotes alignment across departments.
Case studies demonstrate the impact of process mapping on team collaboration:
Case Study | Description | Outcome |
---|---|---|
Marketing Team | Improved communication and clarified roles. | Reduced campaign delivery times by 30% and increased team satisfaction. |
Manufacturing Team | Identified bottlenecks and standardized processes. | Increased productivity and reduced operational costs by 20%. |
Tech Company | Enhanced collaboration between development and support teams. | Reduced response times for customer issues by 40% and improved team morale. |
These examples highlight how process mapping strengthens teamwork and drives better results. By fostering collaboration, organizations can achieve smoother workflows and higher levels of productivity.
Driving Consistency and Standardization
Consistency and standardization are essential for maintaining quality and efficiency in workflows. Lean Six Sigma process mapping provides systems and teams with the tools needed to achieve these goals. By creating a structured approach to processes, organizations can ensure that tasks are performed uniformly, reducing errors and variability. This consistency leads to predictable outcomes, which are critical for meeting client expectations and maintaining operational excellence.
One of the key benefits of process mapping is its ability to document workflows in a clear and repeatable format. Teams can use these visual representations to establish standard operating procedures (SOPs) that guide employees through each step of a process. SOPs reduce ambiguity and ensure that everyone follows the same methods, regardless of their role or experience level.
Lean Six Sigma offers several tools that drive consistency and standardization:
SIPOC: This tool provides a high-level overview of a process by identifying Suppliers, Inputs, Processes, Outputs, and Customers. It helps teams understand the key elements that influence outcomes and ensures that all stakeholders are aligned on the process scope.
Value Stream Mapping: This tool analyzes workflows by distinguishing value-added activities from non-value-added ones. It visualizes the entire process flow, enabling teams to identify inefficiencies and standardize best practices.
These tools allow systems and teams to create a unified approach to process improvement. For example, SIPOC diagrams help clarify roles and responsibilities, while value stream maps highlight areas where standardization can eliminate waste. Together, they provide a comprehensive framework for achieving consistency.
Standardization also enhances training and onboarding processes. New employees can quickly learn their roles by following standardized workflows, reducing the time required to reach full productivity. Additionally, consistent processes make it easier to measure performance and identify areas for improvement.
Standardization is not about rigidity; it is about creating a reliable foundation for innovation. Once processes are consistent, teams can focus on optimizing them further to deliver even greater value to clients.
By leveraging Lean Six Sigma process mapping, organizations can build a culture of consistency that supports long-term success. Systems and teams that prioritize standardization not only improve efficiency but also enhance their ability to adapt to changing demands.
Types of Six Sigma Process Mapping Tools
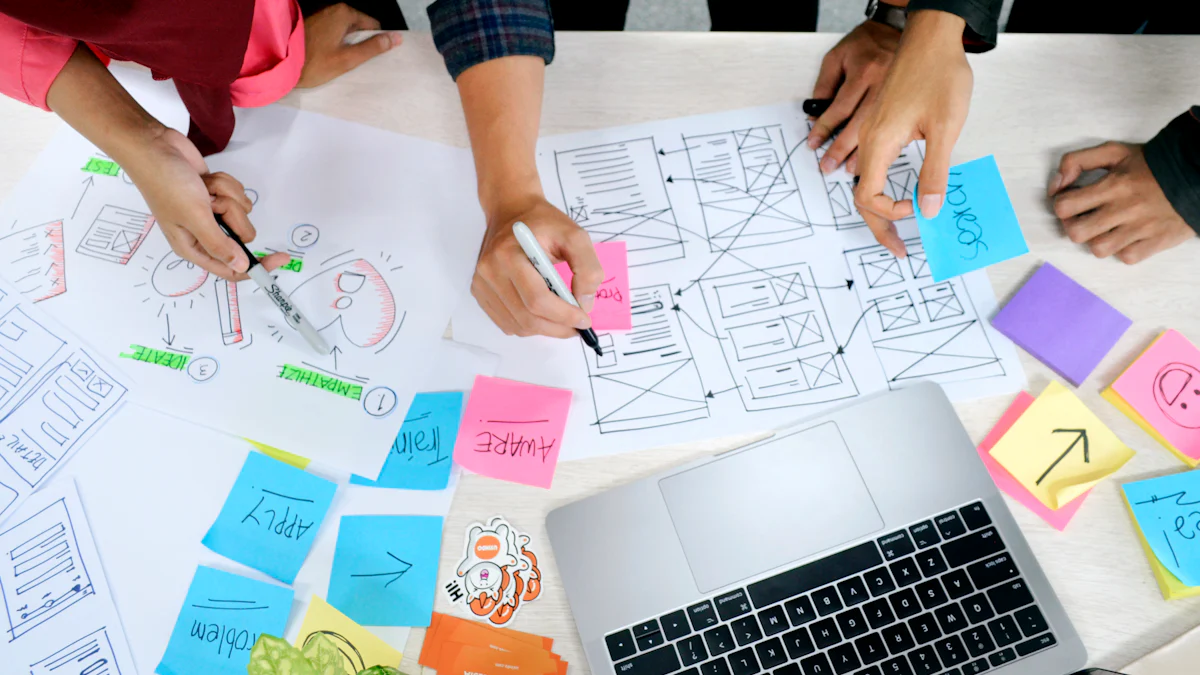
Lean Six Sigma offers a variety of tools to help systems and teams visualize workflows and identify areas for improvement. Each tool serves a unique purpose, allowing organizations to tailor their approach based on the complexity and scope of their processes. Below are three essential tools used in six sigma process mapping.
SIPOC Diagrams
SIPOC diagrams provide a high-level overview of a process by identifying its key components: Suppliers, Inputs, Process, Outputs, and Customers. This tool helps systems and teams understand the broader context of a workflow before diving into specific details. By focusing on these five elements, SIPOC diagrams ensure that all stakeholders align on the process scope and objectives.
For example, a manufacturing team might use a SIPOC diagram to map the journey of raw materials (Inputs) from suppliers to the final product delivered to customers. This approach highlights critical dependencies and ensures that each step adds value.
SIPOC diagrams are particularly useful during the Define phase of the DMAIC framework, as they establish a clear foundation for further analysis.
High-Level Process Maps
High-level process maps offer a simplified representation of a workflow, focusing on the essential steps without delving into intricate details. These maps are ideal for providing a quick overview of a process, making them useful for initial discussions or presentations.
Unlike SIPOC diagrams, which emphasize the broader context, high-level process maps concentrate on the sequence of activities. This distinction makes them valuable for identifying major inefficiencies or bottlenecks early in the analysis.
SIPOC diagrams identify key elements: Suppliers, Inputs, Process, Outputs, and Customers.
High-level process maps provide a simplified overview of essential steps without intricate details.
For instance, a healthcare team might use a high-level process map to outline the patient admission process, from registration to discharge. This visualization helps stakeholders pinpoint delays or redundancies that impact patient care.
Detailed Process Maps
Detailed process maps take a deeper dive into workflows, capturing every step, decision point, and interaction within a process. These maps provide a granular view, making them essential for identifying root causes of inefficiencies or defects.
Systems and teams often use detailed process maps during the Analyze phase of the DMAIC framework. By documenting each step, they can uncover hidden complexities or variations that impact performance.
For example, an IT team optimizing software development workflows might create a detailed process map to track tasks from initial requirements gathering to final deployment. This level of detail helps identify areas where automation or standardization could improve efficiency.
Detailed process maps are most effective when paired with data analysis, as they provide the visual context needed to interpret performance metrics.
By leveraging these tools, organizations can create a comprehensive six sigma process mapping strategy that addresses both high-level goals and detailed operational challenges.
Swimlane Diagrams
Swimlane diagrams provide a structured way to visualize workflows by dividing tasks and responsibilities into distinct lanes. Each lane represents a specific role, department, or team involved in the process. This layout makes it easy to see who is responsible for each step, ensuring accountability and reducing confusion. Systems and teams use swimlane diagrams to clarify roles and streamline communication.
These diagrams highlight interactions between different functional areas, promoting better cross-functional collaboration. By visualizing the process across departments, teams can identify redundancies or unnecessary handoffs. For example, a marketing team might use a swimlane diagram to map the approval process for a campaign. The diagram would show how tasks move between creative, legal, and management teams, making inefficiencies more apparent.
Swimlane diagrams also improve visibility and transparency. Teams can see the entire workflow at a glance, which helps them spot bottlenecks or delays. This clarity enhances collaboration and ensures that everyone understands their role in achieving the desired outcome. Additionally, these diagrams help systems and teams improve efficiency by reducing unnecessary steps and improving the quality of outputs.
Swimlane diagrams are particularly effective for processes involving multiple stakeholders. They provide a clear visual representation of responsibilities, fostering accountability and alignment.
By incorporating swimlane diagrams into a process map, organizations can create a more organized and efficient workflow. This tool not only enhances communication but also ensures that tasks are completed effectively and on time.
Value Stream Maps
Value stream maps focus on identifying inefficiencies within workflows by visualizing the entire process from start to finish. These maps distinguish value-added activities from non-value-added ones, helping systems and teams optimize their operations. By mapping out the current state of a process, organizations can pinpoint areas where resources are wasted or delays occur.
Value stream mapping offers several benefits:
It reveals inefficiencies, such as feedback loops or rework, that hinder productivity.
It reduces the number of steps in a process, streamlining workflows.
It highlights handoffs and wait times, which often cause delays.
For instance, a manufacturing team might use a value stream map to analyze the production process. The map would show how raw materials move through various stages, identifying where delays or waste occur. This insight allows the team to implement changes that reduce cycle times and improve efficiency.
Value stream maps are particularly useful for processes with complex workflows. They provide a comprehensive view of the entire system, enabling teams to focus on areas that deliver the most significant improvements.
By integrating value stream maps into their process map strategy, organizations can achieve greater efficiency and effectiveness. These maps not only help reduce waste but also ensure that every step in the process adds value to the final product or service.
Steps to Create a Lean Six Sigma Process Map
Define the Process Scope
Defining the process scope is the first and most critical step in creating a Lean Six Sigma process map. Establishing clear boundaries ensures that teams focus on relevant activities while avoiding unnecessary distractions. Systems and teams must identify where the process begins and ends, as well as the desired outcomes. For example, a manufacturing team might define the scope of a production process from raw material intake to final product packaging.
Setting measurable objectives is equally important. Teams should align these objectives with organizational goals to maintain focus throughout the mapping exercise. For instance, if the goal is to reduce inefficiencies, the process map should highlight areas where delays or redundancies occur. By clearly defining the scope and objectives, teams create a strong foundation for effective process mapping.
Identify and Sequence Process Steps
Once the scope is defined, systems and teams can identify and sequence the steps involved in the process. This step requires breaking down the workflow into individual tasks, decisions, and interactions. Each step should be documented in the order it occurs to ensure an accurate representation of the process.
For example, a healthcare team mapping the patient admission process might outline steps such as registration, initial consultation, diagnostic tests, and final admission. Sequencing these steps helps teams visualize the flow of activities and identify potential bottlenecks.
Teams should also consider the inputs and outputs for each step. This approach ensures that all critical elements are captured in the process map. By sequencing steps logically, teams can create a clear and actionable representation of the workflow.
Validate the Process Map with Stakeholders
Validating the process map with stakeholders ensures its accuracy and relevance. Teams should engage individuals who are directly involved in or affected by the process. Stakeholders can provide valuable feedback, identify gaps, and confirm that the map reflects the actual workflow.
Several methods can enhance the validation process:
Review the process map with stakeholders to gather feedback and address discrepancies.
Test the map using realistic scenarios to evaluate its performance under different conditions.
Compare the map with industry benchmarks to identify strengths and areas for improvement.
Use data to validate the map and ensure its completeness.
For example, a logistics team might involve warehouse staff and delivery drivers in the validation process. Their insights can help refine the process map, ensuring it captures all critical steps and interactions. By validating the map, teams can build confidence in its accuracy and use it as a reliable tool for process improvement.
Engaging stakeholders early in the validation process fosters collaboration and ensures that the process map aligns with organizational goals.
Analyze for Inefficiencies and Bottlenecks
Analyzing inefficiencies and bottlenecks is a critical step in Lean Six Sigma process mapping. This phase involves examining the current process map to identify areas where workflows slow down or fail to deliver value. Systems and teams must approach this analysis with a focus on uncovering hidden obstacles that hinder productivity.
Several common inefficiencies often emerge during this stage:
Complex processes with diverse stakeholder input can create confusion and delays.
Over-engineered workflows frequently include unnecessary steps that do not contribute to the final outcome.
Discrepancies between theoretical design and practical execution may result in certain steps taking longer than anticipated.
Delays in approval processes often act as significant bottlenecks, reducing overall efficiency.
By addressing these issues, systems and teams can streamline operations and improve performance. For example, a logistics team might discover that redundant approval steps delay shipments. Removing these steps could reduce lead times and enhance customer satisfaction.
To ensure a thorough analysis, teams should use data to validate findings. Metrics such as cycle time, defect rates, and resource utilization provide valuable insights into inefficiencies. Teams can also conduct root cause analysis to determine why bottlenecks occur. This structured approach ensures that solutions target the underlying problems rather than just the symptoms.
Identifying inefficiencies is not about assigning blame. It is about creating opportunities for improvement and ensuring that every step in the process adds value.
Develop an Ideal-State Process Map
Once inefficiencies are identified, systems and teams can focus on creating an ideal-state process map. This map represents the optimized version of the workflow, designed to eliminate waste and maximize value. It serves as a blueprint for achieving operational excellence.
An ideal-state process map incorporates several key characteristics:
Immediate delivery occurs after a request is received, minimizing delays.
Workflows follow a one-piece flow or smaller batch sizes to improve efficiency.
Tasks align with actual customer demand, reducing reliance on forecasts or schedules.
Zero defects and minimal inspection ensure high-quality outcomes.
Waste, unnecessary movements, and partial completions are eliminated.
For example, a manufacturing team might stagger work times and resources to match customer demand. This adjustment reduces waiting periods and ensures a smoother production flow. Similarly, co-locating resources across the value stream can enhance collaboration and reduce handoffs.
Visual clarity is another hallmark of an ideal-state process map. A visual workplace allows teams to see the current status and identify problems at a glance. Minimal warehouse floor space, right-sized equipment, and optimized inventory levels further contribute to efficiency.
Leadership also plays a vital role in sustaining the ideal state. Leaders should act as coaches, fostering a culture of continuous improvement. Dedicated time for process enhancements and data-driven decision-making ensures that the ideal-state map evolves with changing needs.
An ideal-state process map is not static. It is a dynamic tool that guides systems and teams toward long-term success while adapting to new challenges and opportunities.
By developing and implementing an ideal-state process map, organizations can achieve streamlined workflows, reduced costs, and improved customer satisfaction. This proactive approach transforms inefficiencies into opportunities for growth.
Real-World Applications of Six Sigma Process Mapping
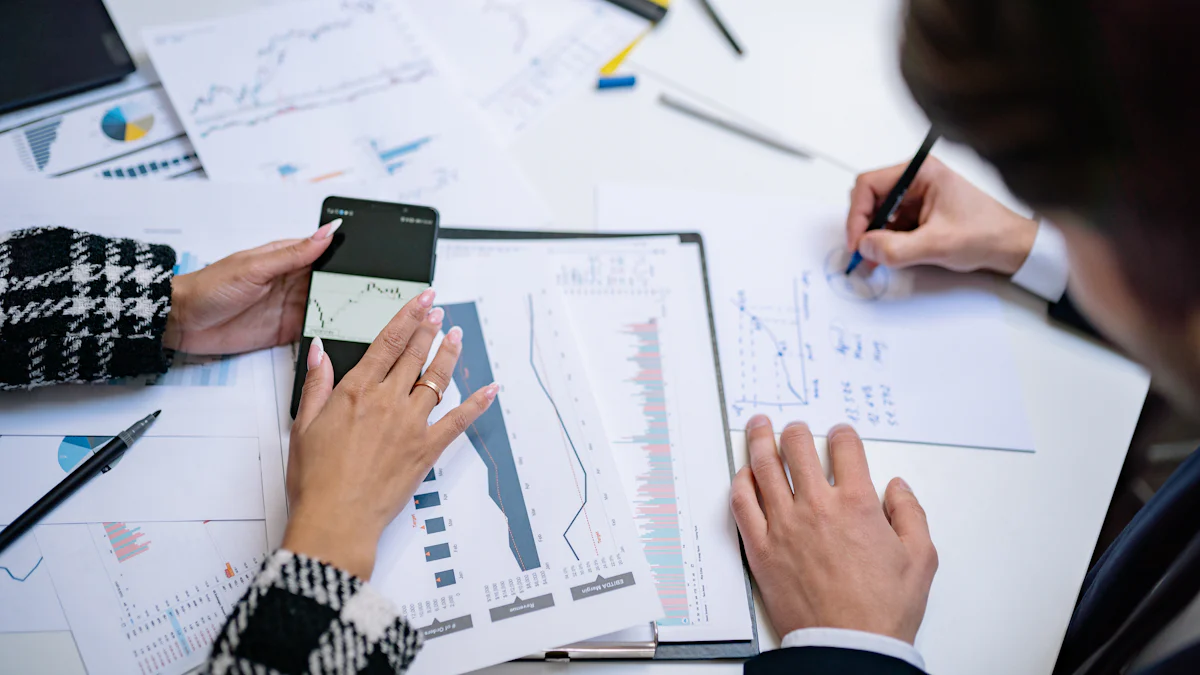
Manufacturing: Reducing Production Delays
Manufacturing systems often face challenges like production delays caused by inefficiencies in supply chains or workflows. Six sigma process mapping provides a structured approach to address these issues. For instance, a manufacturing company experiencing delays in raw material delivery used this methodology to analyze its supply chain. By identifying non-value-adding activities, the team implemented changes such as automating procurement and improving communication with suppliers. These adjustments reduced lead times from 14 days to 7 days, significantly minimizing production delays.
This example highlights how a process map can uncover inefficiencies and guide teams toward actionable solutions. By visualizing workflows, manufacturing systems can streamline operations, reduce waste, and enhance overall productivity.
Healthcare: Streamlining Patient Care Processes
Healthcare organizations rely on efficient workflows to deliver timely and effective patient care. Six sigma process mapping plays a pivotal role in optimizing these workflows. Value Stream Mapping (VSM), a key tool in this methodology, enables healthcare teams to visualize the entire patient journey, from initial contact to discharge.
VSM allows systems to identify bottlenecks and opportunities for improvement, ensuring a smoother and more patient-focused care delivery process.
Healthcare teams benefit from VSM in several ways:
It identifies waste and inefficiencies, leading to streamlined workflows.
It optimizes both patient care steps and supporting administrative processes, enhancing patient outcomes.
For example, a hospital might use a process map to analyze the patient admission process. By identifying delays in registration or diagnostic testing, the team can implement changes that reduce wait times and improve the overall patient experience. This approach not only enhances care quality but also boosts operational efficiency.
IT: Optimizing Agile Development Workflows
Agile IT development thrives on collaboration and efficiency. Six sigma process mapping helps IT teams optimize workflows by creating a shared understanding of roles, responsibilities, and task sequences. Tools like flowcharts and swimlane diagrams clarify workflows, reducing confusion and improving communication among team members.
Key benefits of this approach include:
Enhanced collaboration in cross-functional teams.
Improved task sequencing, which minimizes delays.
Greater transparency in workflows, enabling faster decision-making.
For example, an IT team working on software development might use a process map to visualize the steps from requirements gathering to deployment. By identifying inefficiencies, such as redundant handoffs between teams, they can streamline the process and deliver projects faster. This structured approach ensures that every team member understands their role, fostering a more cohesive and productive work environment.
By applying six sigma process mapping, IT systems can achieve greater agility and efficiency, ensuring that projects meet deadlines and deliver value to stakeholders.
Logistics: Improving Supply Chain Efficiency
Logistics systems often face challenges such as delays, inefficiencies, and high operational costs. Six sigma process mapping provides a structured approach to address these issues by visualizing workflows and identifying areas for improvement. This methodology begins with a comprehensive evaluation of the supply chain, from sourcing materials to delivering products. By mapping the entire process, systems and teams can uncover inefficiencies and eliminate waste.
Several benefits emerge when Lean Six Sigma principles are applied to logistics:
Enhanced quality through reduced defects and variability.
Cost savings by identifying and removing waste.
Better collaboration among teams with clear visual workflows.
Data-driven insights for continuous improvement.
For example, a logistics company experiencing frequent delays in order fulfillment used six sigma process mapping to analyze its supply chain. The team created a value stream map to visualize the flow of goods from suppliers to customers. This analysis revealed bottlenecks in the inventory management process and redundant approval steps in shipping. By streamlining these areas, the company reduced delivery times by 25% and improved customer satisfaction.
Another key advantage of process mapping in logistics is its ability to enhance collaboration. Visual workflows clarify roles and responsibilities, ensuring that all stakeholders understand their contributions to the supply chain. For instance, a warehouse team might use a swimlane diagram to map the handoffs between receiving, storage, and shipping departments. This approach reduces confusion, minimizes delays, and fosters better communication across teams.
Data-driven insights also play a critical role in optimizing supply chain efficiency. Metrics such as lead time, defect rates, and resource utilization help teams identify performance gaps and prioritize improvements. For example, a transportation team might use these insights to optimize delivery routes, reducing fuel costs and transit times.
Lean Six Sigma empowers logistics systems to achieve operational excellence by focusing on value-added activities and eliminating waste. By leveraging tools like process maps and value stream analysis, teams can create streamlined workflows that deliver measurable results. Organizations seeking to enhance their supply chain efficiency can benefit from adopting this methodology to drive continuous improvement.
To learn more about how six sigma process mapping can transform logistics operations, reach out to our team for expert guidance.
Overcoming Challenges in Process Mapping
Addressing Resistance to Change
Resistance to change often emerges as a significant barrier during Lean Six Sigma process mapping. Team members may hesitate to adopt new workflows due to concerns about increased workload or job security. This reluctance can slow progress and hinder the success of process improvement initiatives.
Organizations can address resistance by implementing structured strategies across three key phases:
Phase | Strategy Description |
---|---|
Phase 1 – Prepare Approach | Identify resistance early and develop tactics based on understanding the change's impact on individuals. |
Phase 2 – Manage Change | Integrate resistance management into the change process to address barriers and equip teams for transitions. |
Phase 3 – Sustain Outcomes | Review performance and document lessons learned to improve future resistance management efforts. |
In addition to these phases, systems and teams can adopt practical approaches to foster acceptance:
Proactive communication: Regular updates keep stakeholders informed and engaged.
Stakeholder engagement: Involving team members in the solution process fosters ownership and reduces pushback.
Feedback loops: Mechanisms for ongoing feedback allow adjustments based on team input.
By prioritizing open communication and collaboration, organizations can ease transitions and build trust among team members. This approach ensures smoother implementation of Lean Six Sigma methodologies.
Ensuring Accurate Data Collection
Accurate data collection forms the foundation of effective process mapping. However, many organizations struggle with inconsistent practices, human error, and incomplete information. These issues can compromise the reliability of insights and hinder decision-making.
To overcome these challenges, systems and teams should adopt best practices for data collection:
Leverage technology to automate data gathering, reducing errors.
Conduct regular audits to identify and address quality issues early.
Promote a culture of data sharing to enhance collaboration.
Invest in data cleaning and preparation to ensure accuracy.
Additionally, teams should gather comprehensive information about each process step. Observing workflows, interviewing stakeholders, and reviewing documentation can provide valuable insights. Incorporating measurable metrics, such as cycle times or error rates, further enhances data reliability.
Tip: Automating data collection not only improves accuracy but also frees up resources for analysis and decision-making.
By following these practices, organizations can ensure their process maps reflect reality, enabling more effective improvements.
Avoiding Overcomplication in Process Maps
Overcomplicated process maps can overwhelm teams and obscure critical insights. Excessive detail or unnecessary elements often make workflows harder to understand, reducing their effectiveness as a tool for improvement.
To avoid this pitfall, systems and teams should focus on simplicity and clarity. Key strategies include:
Define clear objectives: Ensure the process map aligns with the intended goals.
Prioritize essential steps: Include only the tasks, decisions, and interactions critical to the workflow.
Use visual aids effectively: Tools like swimlane diagrams and value stream maps can simplify complex processes.
Validate with stakeholders: Collaborate with team members to confirm the map's accuracy and relevance.
For example, a healthcare team mapping patient care workflows might limit their focus to high-impact steps, such as registration, diagnosis, and treatment. This approach ensures the map remains actionable and easy to interpret.
Note: A streamlined process map not only improves understanding but also accelerates decision-making and implementation.
By emphasizing simplicity, organizations can create process maps that drive meaningful improvements without overwhelming their teams.
Lean six sigma process mapping serves as a cornerstone for process improvement by helping systems and teams visualize workflows and identify inefficiencies. Organizations that align their processes with business goals experience enhanced operational efficiency and quality. This methodology fosters collaboration through shared visual representations, enabling teams to eliminate waste and redirect resources toward impactful initiatives.
Its applications span industries, from manufacturing to healthcare, where tools like value stream mapping and SIPOC diagrams have driven measurable outcomes. Teams achieve smoother workflows, reduced cycle times, and higher-quality outputs. By fostering a culture of collaboration and innovation, organizations ensure long-term success while adapting to evolving demands.
Lean six sigma process mapping is not just a tool—it is a universal solution for streamlining workflows and enhancing productivity. Systems and teams seeking to achieve operational excellence can rely on this approach to drive continuous improvement.
FAQ
What is the primary purpose of Lean Six Sigma process mapping?
Lean Six Sigma process mapping helps systems and teams visualize workflows, identify inefficiencies, and streamline operations. It provides a structured approach to improving processes by reducing waste and enhancing quality.
How does process mapping benefit team collaboration?
Process mapping fosters collaboration by creating a shared visual representation of workflows. Teams gain clarity on roles and responsibilities, reducing misunderstandings and improving communication across departments.
Which industries can benefit from Lean Six Sigma process mapping?
Industries such as manufacturing, healthcare, IT, and logistics can benefit. Systems and teams in these sectors use process mapping to optimize workflows, reduce costs, and improve service delivery.
What tools are commonly used in Lean Six Sigma process mapping?
Common tools include SIPOC diagrams, value stream maps, swimlane diagrams, and detailed process maps. Each tool serves a specific purpose, helping systems and teams analyze and improve workflows.
How does process mapping help eliminate waste?
Process mapping identifies non-value-added activities, redundancies, and bottlenecks. Systems and teams can use this insight to remove unnecessary steps, optimize resources, and focus on value-added tasks.
Can Lean Six Sigma process mapping improve customer satisfaction?
Yes, it enhances customer satisfaction by streamlining workflows and ensuring consistent, high-quality outcomes. Systems and teams can deliver faster, more reliable services by eliminating inefficiencies.
How long does it take to create a process map?
The time required depends on the complexity of the process. Simple workflows may take hours, while detailed maps for complex systems may require days. Systems and teams should allocate sufficient time for validation and analysis.
Where can systems and teams learn more about implementing process mapping?
Systems and teams can reach out to our experts for guidance. We provide tailored solutions to help organizations implement Lean Six Sigma process mapping effectively and achieve operational excellence.