Unlocking Success with Six Sigma Process Mapping
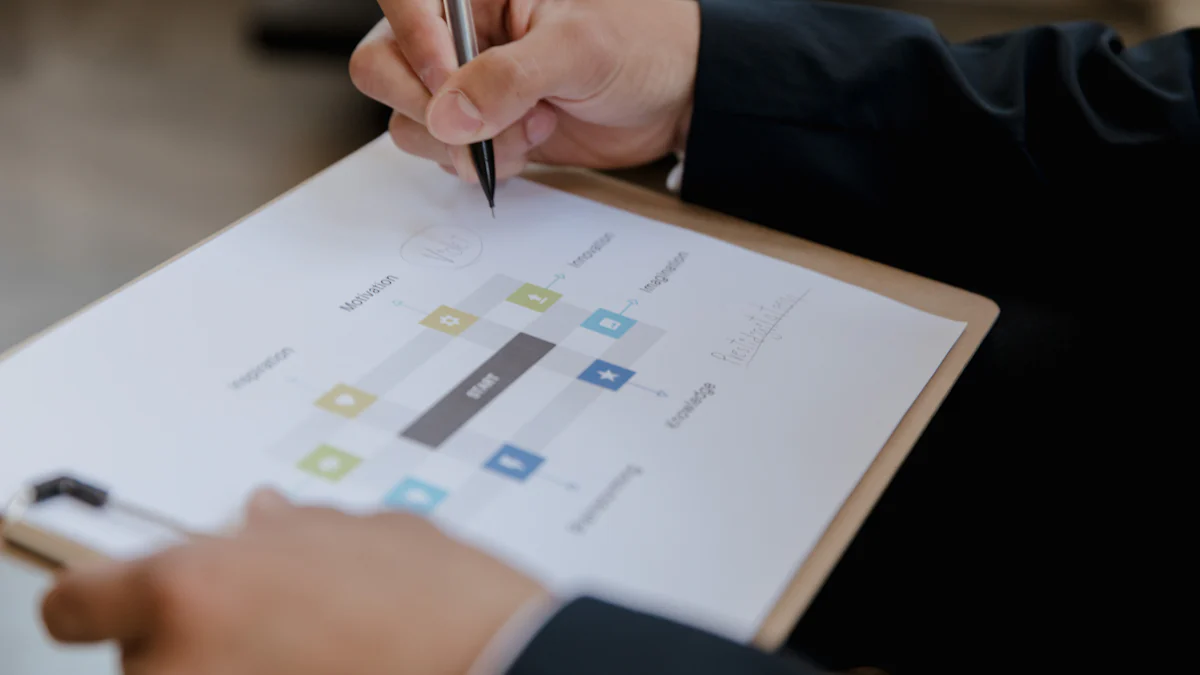
Six Sigma Process Mapping serves as a powerful visual tool for analyzing and improving business processes. By breaking down each step, it highlights inefficiencies and pinpoints areas for improvement. This approach reduces variability, eliminates waste, and enhances process efficiency. Teams can use it to identify bottlenecks, streamline workflows, and ensure consistent quality. Lean Six Sigma methodologies often integrate process mapping to support data-driven decisions and foster continuous improvement. With its ability to align processes with organizational goals, this tool becomes indispensable in modern business management, driving measurable success and operational excellence. This knowledge is crucial for organizations aiming to optimize their processes effectively.
Key Takeaways
Six Sigma Process Mapping is a vital tool for visualizing and improving business processes, helping teams identify inefficiencies and streamline workflows.
By breaking down processes into manageable steps, organizations can reduce variability, eliminate waste, and enhance overall quality.
Effective process mapping involves key components such as defining process scope, identifying roles, and integrating data to support data-driven decision-making.
Utilizing tools like SIPOC diagrams and value stream maps can significantly enhance collaboration and communication among team members.
Organizations that adopt process mapping often experience improved efficiency, reduced costs, and increased customer satisfaction through consistent quality outcomes.
Continuous improvement is essential; regularly reviewing and updating process maps ensures they remain relevant and effective in achieving business goals.
Embracing Six Sigma methodologies empowers teams to drive measurable success and operational excellence across various industries.
What is Six Sigma Process Mapping?
Definition and Core Principles
Six Sigma Process Mapping is a structured approach to visually representing the steps, interactions, and flow within a process. It provides a clear and detailed picture of how a process operates, enabling teams to identify inefficiencies and areas for improvement. This method aligns with the core principles of Six Sigma, which focus on reducing variability, eliminating waste, and enhancing quality. By breaking down processes into manageable components, it ensures that every step contributes to the overall goal of operational excellence.
The foundation of process mapping lies in its ability to simplify complex workflows. Teams use it to uncover hidden bottlenecks, redundant steps, or unnecessary delays. This clarity fosters transparency and creates a shared understanding among stakeholders. Additionally, process mapping supports Lean methodologies by emphasizing value-added activities while eliminating non-essential tasks. These principles make it an indispensable tool for organizations aiming to optimize their operations.
Key Components of Process Mapping in Six Sigma
Effective process mapping relies on several key components that ensure accuracy and usability. These components include:
Process Scope: Clearly defining the boundaries and objectives of the process being mapped. This step ensures that the focus remains on relevant activities without unnecessary distractions.
Steps and Activities: Identifying each step within the process, including inputs, outputs, and interactions. This detailed breakdown helps pinpoint inefficiencies and areas for improvement.
Flow Representation: Using visual tools such as flowcharts, swimlane diagrams, or value stream maps to illustrate the sequence and relationships between steps. These visuals make it easier for teams to analyze and optimize workflows.
Roles and Responsibilities: Assigning accountability to specific team members or departments for each step. This clarity promotes collaboration and ensures that everyone understands their role in achieving process goals.
Data Integration: Incorporating data to measure performance, identify trends, and support decision-making. Metrics such as cycle time, error rates, or resource utilization provide valuable insights for continuous improvement.
By combining these components, process mapping becomes a powerful tool for driving efficiency and quality. Businesses that adopt this approach often experience reduced cycle times, streamlined operations, and improved outcomes. For example, systems and teams using process mapping can uncover improvement opportunities, eliminate redundant steps, and align processes with organizational goals. This structured methodology not only enhances individual processes but also contributes to the overall success of the organization.
Why Six Sigma Process Mapping is Essential for Businesses
Identifying Inefficiencies and Bottlenecks
Process mapping plays a critical role in identifying inefficiencies and bottlenecks within workflows. By visually representing each step of a process, it becomes easier to pinpoint areas where delays, redundancies, or errors occur. For example, a project manager overseeing a corporate initiative can use process mapping to uncover unnecessary steps that slow down progress. This clarity allows teams to focus on eliminating waste and streamlining operations.
In Six Sigma, the emphasis on reducing variability aligns perfectly with the goals of process mapping. Teams can analyze workflows to identify non-value-added activities and prioritize improvements. This approach not only enhances efficiency but also ensures that resources are allocated effectively. Systems and teams that adopt this methodology often experience significant gains in productivity and operational performance.
Facilitating Better Communication and Collaboration
Process mapping fosters better communication and collaboration among team members. A visual representation of workflows provides a shared understanding of how tasks interconnect and who is responsible for each step. This transparency reduces misunderstandings and promotes alignment across departments.
For instance, in environments like manufacturing plants or hospitals, process maps serve as a common reference point. They help teams coordinate efforts and ensure that everyone works toward the same objectives. Lean Six Sigma methodologies further enhance this collaboration by emphasizing teamwork and continuous improvement. When teams communicate effectively, they can address challenges more efficiently and achieve better outcomes.
Supporting Data-Driven Decision Making
Data-driven decision-making is a cornerstone of Six Sigma, and process mapping supports this principle by integrating measurable metrics into workflows. By incorporating data such as cycle times, error rates, or resource utilization, teams gain valuable insights into process performance. These insights enable informed decisions that drive continuous improvement.
For example, a value stream map can highlight areas where delays occur, allowing teams to address root causes with targeted solutions. This analytical approach ensures that changes are based on evidence rather than assumptions. Organizations that leverage process mapping in their quality improvement initiatives often achieve superior results, including reduced costs and enhanced customer satisfaction.
Benefits of Six Sigma Process Mapping
Improved Efficiency and Productivity
Process mapping enables systems and teams to identify inefficiencies and streamline workflows. By visually representing each step, it becomes easier to pinpoint redundant tasks, delays, or unnecessary actions. This clarity allows organizations to focus on eliminating waste and optimizing resources. For example, a manufacturing team can use process mapping to reduce cycle times and improve production rates.
The structured approach of process mapping aligns with Lean Six Sigma principles, emphasizing value-added activities while minimizing non-essential ones. Teams that adopt this methodology often experience significant boosts in productivity. By refining processes, they achieve smoother operations and faster delivery of results. This improvement not only benefits internal workflows but also enhances the overall performance of the organization.
Enhanced Quality and Customer Satisfaction
Process mapping plays a vital role in improving quality and meeting customer expectations. By identifying sources of variability, it helps teams reduce defects and ensure consistency in outcomes. For instance, a service provider can use process mapping to standardize procedures, leading to more reliable and high-quality services.
When processes operate efficiently and deliver consistent results, customer satisfaction naturally increases. Clients receive products or services that meet their expectations, fostering trust and loyalty. Systems and teams that prioritize process improvement through mapping often see measurable gains in customer retention and positive feedback. This focus on quality not only strengthens relationships with clients but also enhances the organization's reputation in the market.
Cost Reduction and Waste Elimination
One of the most significant benefits of process mapping is its ability to reduce costs and eliminate waste. By analyzing workflows, teams can identify areas where resources are underutilized or misallocated. For example, a logistics company might uncover inefficiencies in its supply chain, leading to cost savings and better resource management.
Process mapping supports data-driven decisions, enabling organizations to address root causes of waste effectively. Teams can implement targeted solutions that minimize unnecessary expenses and maximize value. This approach aligns with Six Sigma's goal of achieving operational excellence. Businesses that embrace process mapping often experience lower operational costs and higher profitability, making it a valuable tool for long-term success.
Types of Six Sigma Process Maps
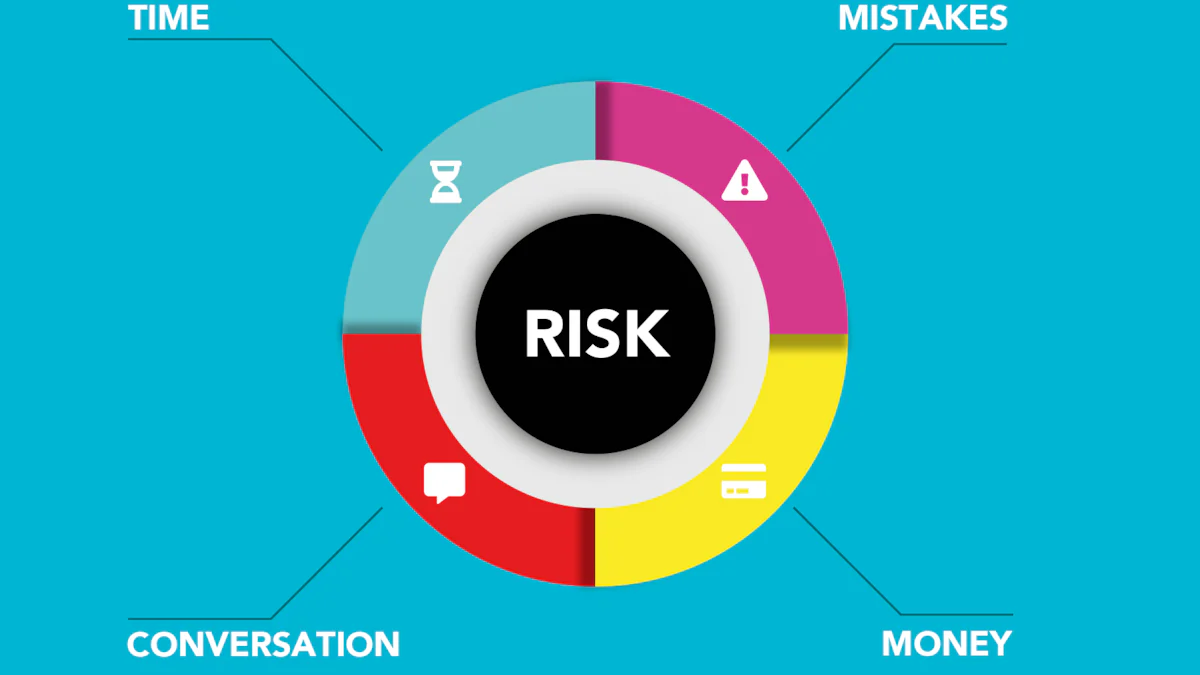
High-Level Process Maps
High-level process maps provide a simplified overview of a process. They focus on the major steps and interactions without delving into intricate details. These maps are ideal for understanding the overall structure of a workflow and identifying broad areas for improvement. For example, a manufacturing team might use a high-level process map to outline the key stages of production, such as material sourcing, assembly, and quality checks.
This type of process map is particularly useful during the initial stages of process mapping. It helps systems and teams establish a shared understanding of the workflow's scope and objectives. By focusing on the big picture, high-level process maps enable organizations to prioritize critical areas for optimization. Tools like SIPOC diagrams (Suppliers, Inputs, Process, Outputs, Customers) often complement high-level mapping by providing additional context about the process.
Detailed Process Maps
Detailed process maps break down workflows into specific steps, interactions, and decision points. They offer a comprehensive view of how a process operates, making it easier to identify inefficiencies, redundancies, or delays. For instance, a logistics company might use a detailed process map to analyze every step in its supply chain, from order placement to final delivery.
These maps often include metrics such as cycle times, error rates, or resource utilization. This data-driven approach aligns with the principles of Six Sigma, which emphasize reducing variability and improving quality. Detailed process maps also support continuous improvement by uncovering root causes of inefficiencies. Digital tools like Visio or Lucid Chart simplify the creation of these maps, offering templates and easy editing features.
Swimlane Diagrams
Swimlane diagrams add an extra layer of clarity by organizing process steps into lanes that represent different departments, roles, or functions. This format vividly shows where processes cross departmental boundaries, highlighting areas where collaboration or communication may falter. For example, a hospital might use a swimlane diagram to map patient care processes, assigning lanes to departments like admissions, nursing, and billing.
By visually separating responsibilities, swimlane diagrams help systems and teams identify bottlenecks or misalignments in workflows. They also promote accountability by clearly defining who is responsible for each step. Many detailed process maps adopt the swimlane format to simplify complex workflows. Tools like cross-functional flowcharts further enhance this approach by revealing who does what and when within a process.
Swimlane diagrams are particularly effective for fostering collaboration and improving communication across teams. They ensure that everyone involved in a process understands their role and how their actions impact others. This clarity not only streamlines operations but also supports the alignment of processes with organizational goals.
Value Stream Maps
Value stream maps provide a comprehensive view of the entire process flow, from the initial input to the final output. This type of process map focuses on identifying value-added and non-value-added activities within a workflow. By analyzing these activities, systems and teams can pinpoint inefficiencies, delays, or waste that hinder productivity. For example, a manufacturing company might use a value stream map to examine its production line, identifying steps that do not contribute to the final product's value.
The primary goal of value stream mapping is to optimize processes by eliminating waste and improving efficiency. Teams often use this tool during the Define and Measure phases of Six Sigma projects. It enables them to visualize the current state of a process and design an improved future state. This approach aligns with Six Sigma principles, which emphasize reducing variability and enhancing quality.
Creating a value stream map involves several key steps:
Define the Scope: Teams identify the start and end points of the process they want to map. This step ensures clarity and focus throughout the mapping exercise.
Document Current State: Teams visually represent the existing process, including all steps, delays, and interactions. Tools like Slickplan’s Diagram Maker or Visio simplify this task by offering templates and editing features.
Analyze the Process: Teams evaluate the current state map to identify bottlenecks, redundancies, or waste. Metrics such as cycle time and lead time provide valuable insights during this analysis.
Design Future State: Teams create a new map that eliminates inefficiencies and aligns with organizational goals. This future state map serves as a blueprint for process improvement.
Value stream maps are particularly effective in industries like manufacturing, logistics, and healthcare. They help systems and teams streamline operations, reduce costs, and enhance customer satisfaction. For instance, a hospital might use a value stream map to improve patient care by reducing wait times and optimizing resource allocation.
Digital tools like Lucid Chart and Visio enhance the value stream mapping process by providing user-friendly interfaces and customizable templates. These tools allow teams to create detailed maps quickly and efficiently. By leveraging value stream maps, organizations can achieve significant improvements in process performance and overall operational success.
Steps to Create a Six Sigma Process Map
Define the Process Scope and Objectives
Defining the scope and objectives forms the foundation of effective process mapping. Teams must establish clear boundaries for the process under review. This step ensures focus on relevant activities while avoiding unnecessary distractions. Systems and teams should identify the start and end points of the process, as well as the desired outcomes. For example, a manufacturing team might aim to reduce production cycle times or improve quality control measures.
Objectives should align with organizational goals. Teams must ensure that the process contributes to broader business success. By setting measurable targets, such as reducing error rates or increasing efficiency, teams can track progress effectively. This clarity helps systems and teams maintain alignment throughout the mapping exercise. A well-defined scope and clear objectives provide a strong starting point for creating a successful process map.
Gather Data and Identify Key Steps
Accurate data collection is essential for creating a reliable process map. Teams should gather information about each step within the process, including inputs, outputs, and interactions. Observing workflows, interviewing stakeholders, and reviewing existing documentation can provide valuable insights. For instance, a logistics company might analyze delivery schedules, resource allocation, and customer feedback to understand its supply chain process.
Identifying key steps involves breaking down the process into manageable components. Teams should focus on capturing every activity, decision point, and interaction. This detailed breakdown helps uncover inefficiencies, redundancies, or delays. Systems and teams can use tools like value stream mapping to document these steps comprehensively. By integrating data into the mapping process, teams gain a deeper understanding of how workflows operate and where improvements are needed.
Visualize the Process Using Tools
Visualization transforms raw data into a clear and actionable representation of the process. Teams can use tools like flowcharts, swimlane diagrams, or value stream mapping to illustrate workflows. These visual aids make it easier to analyze the sequence of steps, identify bottlenecks, and optimize operations. For example, a hospital might use a swimlane diagram to map patient care processes, assigning lanes to departments like admissions, nursing, and billing.
Digital tools such as Lucid Chart or Visio simplify the creation of process maps. These platforms offer templates and customization options, enabling teams to design detailed and accurate visuals. Systems and teams should ensure that the chosen tool aligns with their specific needs and objectives. A well-visualized process map serves as a common reference point, fostering collaboration and supporting data-driven decision-making.
By following these steps, organizations can create effective process maps that drive efficiency and quality. Teams that invest time in defining scope, gathering data, and visualizing workflows often achieve significant improvements in performance. Process mapping not only enhances individual processes but also contributes to the overall success of the organization.
Analyze and Optimize the Process
Analyzing and optimizing a process involves a systematic approach to identify inefficiencies and implement improvements. Teams should begin by thoroughly examining the process map to uncover bottlenecks, redundancies, or delays. This analysis provides a clear understanding of areas that hinder performance. For instance, reviewing a value stream map can reveal non-value-added activities that waste resources or time.
Optimization focuses on refining workflows to enhance efficiency and quality. Systems and teams can apply Lean Six Sigma principles to eliminate unnecessary steps and reduce variability. Prioritizing value-added activities ensures that every action contributes to achieving organizational goals. For example, a manufacturing team might streamline production by reorganizing tasks or reallocating resources.
To optimize effectively, teams should follow these steps:
Evaluate Current Performance: Use metrics such as cycle time, error rates, or resource utilization to assess the process. These data points highlight specific areas needing improvement.
Identify Root Causes: Conduct root cause analysis to determine why inefficiencies occur. Tools like fishbone diagrams or the "5 Whys" method can help pinpoint underlying issues.
Implement Targeted Solutions: Develop and test solutions that address identified problems. For example, automating repetitive tasks can reduce errors and save time.
Monitor and Adjust: Continuously track the process after implementing changes. Use feedback and performance data to make further adjustments as needed.
Digital tools like Value Stream Mapping templates simplify the optimization process. These tools provide a structured framework for visualizing and analyzing workflows. By leveraging such resources, systems and teams can achieve significant improvements in productivity and operational performance.
Optimization is not a one-time effort. Continuous improvement ensures that processes remain efficient and aligned with evolving business needs. Teams that embrace this mindset often experience sustained success and measurable outcomes. For organizations seeking to enhance their operations, adopting Six Sigma methodologies and tools like process mapping is essential. To learn more about these strategies, reach out to us for guidance and support.
Tools and Techniques for Effective Process Mapping
Common Tools (e.g., SIPOC, Value Stream Mapping)
Effective process mapping relies on structured tools that simplify workflows and enhance clarity. Among these tools, SIPOC and value stream mapping stand out for their versatility and impact.
SIPOC (Suppliers, Inputs, Process, Outputs, Customers) provides a high-level overview of a process. It identifies the key elements that influence outcomes, ensuring teams focus on critical components. For example, in a manufacturing plant, SIPOC can outline the relationship between raw material suppliers, production steps, and customer delivery. This tool helps systems and teams establish a shared understanding of the process scope, making it an excellent starting point for creating a six sigma process map.
Value stream mapping offers a detailed analysis of workflows by distinguishing value-added activities from non-value-added ones. It visualizes the entire process flow, from input to output, enabling teams to identify inefficiencies and eliminate waste. For instance, a logistics company might use value stream mapping to optimize its supply chain, reducing delays and improving resource allocation. This tool aligns with six sigma principles by emphasizing efficiency and quality.
Both tools support data-driven decision-making, a cornerstone of six sigma methodologies. They provide actionable insights that guide teams toward continuous improvement. By integrating SIPOC and value stream mapping into their strategies, organizations can achieve measurable gains in productivity and operational performance.
Software Solutions for Process Mapping
Digital tools have revolutionized process mapping by offering user-friendly interfaces and advanced features. Software solutions like Lucidchart, Visio, and Slickplan simplify the creation of six sigma process maps, making them accessible to systems and teams across industries.
Lucidchart provides customizable templates and drag-and-drop functionality, enabling teams to design detailed process maps quickly. Its collaborative features allow multiple users to work on the same map simultaneously, fostering teamwork and alignment. For example, a hospital might use Lucidchart to map patient care processes, ensuring seamless coordination between departments.
Visio offers robust diagramming capabilities, ideal for creating complex process maps. It supports various formats, including swimlane diagrams and value stream maps, catering to diverse organizational needs. Manufacturing teams often rely on Visio to visualize production workflows, identify bottlenecks, and implement improvements.
Slickplan specializes in value stream mapping, providing tools that highlight inefficiencies and suggest optimization strategies. Its intuitive interface makes it easy for teams to document current workflows and design future state maps. For instance, a restaurant chain might use Slickplan to streamline its supply chain, reducing costs and enhancing service quality.
These software solutions enhance the accuracy and usability of process maps, empowering teams to make informed decisions. By leveraging digital tools, organizations can unlock the full potential of process mapping, driving efficiency and achieving operational excellence.
Real-World Applications and Success Stories
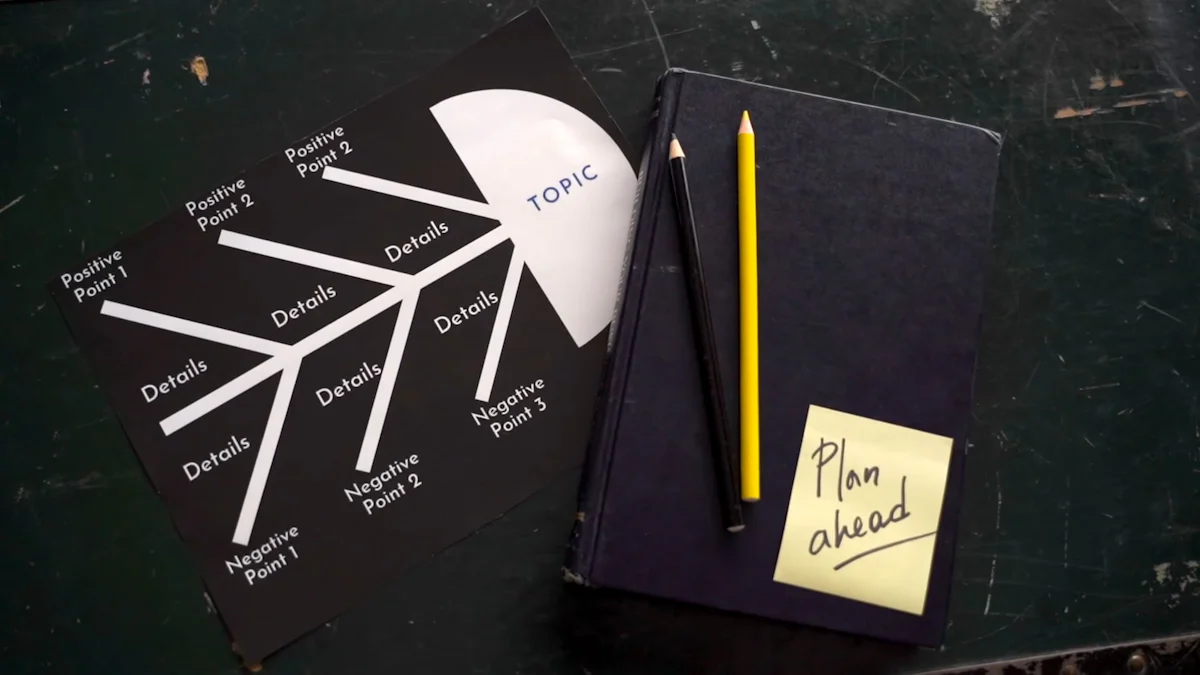
Case Study 1: Manufacturing Industry
In the manufacturing industry, process mapping has proven to be a transformative tool for achieving operational excellence. A global automotive manufacturer faced challenges with production delays and high defect rates. The systems and teams implemented Six Sigma process mapping to analyze their assembly line. By visualizing each step, they identified bottlenecks in material handling and redundant quality checks that slowed down production.
The team used value stream mapping to distinguish value-added activities from non-value-added ones. This approach revealed inefficiencies in resource allocation and highlighted areas for improvement. After optimizing the workflow, the company reduced cycle times by 20% and decreased defect rates by 15%. These improvements not only enhanced productivity but also boosted customer satisfaction by delivering higher-quality vehicles on time.
Process mapping also supported data-driven decisions. Metrics such as error rates and lead times provided actionable insights, enabling the team to implement targeted solutions. The success of this initiative demonstrated how process mapping can streamline operations and align processes with organizational goals. Manufacturing systems and teams seeking similar results can leverage this methodology to uncover improvement opportunities and drive measurable outcomes.
Case Study 2: Service Industry
In the service industry, process mapping has been instrumental in enhancing efficiency and customer experience. A healthcare provider struggled with long patient wait times and inconsistent service delivery. The organization’s systems and teams adopted Six Sigma process mapping to address these issues. By creating a swimlane diagram, they visualized the patient care process across departments, including admissions, nursing, and billing.
The map revealed communication gaps between departments and unnecessary steps that prolonged the patient journey. Using this information, the team streamlined workflows and redefined roles to ensure accountability. For example, they automated appointment scheduling and optimized resource allocation in the nursing department. These changes reduced patient wait times by 30% and improved service consistency.
The healthcare provider also integrated data into the process mapping exercise. Metrics such as average wait times and patient feedback scores guided the optimization efforts. This analytical approach ensured that improvements were evidence-based and aligned with patient needs. The success of this initiative highlighted the value of process mapping in fostering collaboration and delivering superior service quality.
Organizations in the service sector can replicate this success by adopting process mapping to visualize workflows and identify inefficiencies. By doing so, they can enhance operational performance and meet customer expectations effectively. For more guidance on implementing these strategies, reach out to us for expert support.
Challenges and Best Practices in Process Mapping
Common Challenges in Process Mapping
Process mapping, while highly effective, presents several challenges that systems and teams must address to ensure successful implementation. One common issue involves the lack of clarity in defining the process scope. Teams often struggle to establish clear boundaries, leading to confusion and inefficiencies during the mapping exercise. Without a well-defined scope, the process map may include irrelevant details or overlook critical steps, reducing its effectiveness.
Another challenge arises from incomplete or inaccurate data collection. Teams may fail to gather sufficient information about the process, resulting in maps that do not accurately reflect real workflows. This issue can hinder the identification of inefficiencies and bottlenecks. For example, missing data on resource utilization or cycle times can obscure areas requiring improvement.
Resistance to change also poses a significant obstacle. Stakeholders may hesitate to adopt process mapping due to unfamiliarity with the methodology or fear of disrupting established workflows. This resistance can limit collaboration and slow down the mapping process. Additionally, the complexity of certain workflows can make it difficult to create detailed and accurate maps. Teams may find it challenging to visualize intricate processes involving multiple departments or decision points.
Lastly, the absence of proper tools and techniques can impede progress. Without access to tools like SIPOC diagrams, swimlane diagrams, or value stream mapping, teams may struggle to create comprehensive and actionable process maps. These tools provide essential frameworks for analyzing workflows and identifying areas for optimization.
Best Practices for Successful Implementation
To overcome these challenges, systems and teams can adopt best practices that enhance the effectiveness of process mapping. The first step involves clearly defining the process scope and objectives. Teams should establish the start and end points of the process, as well as the desired outcomes. Using tools like SIPOC diagrams can help outline the key components of the process, including suppliers, inputs, outputs, and customers. This clarity ensures that the mapping exercise remains focused and relevant.
Accurate data collection is another critical practice. Teams should gather comprehensive information about each step in the process, including inputs, outputs, and interactions. Observing workflows, interviewing stakeholders, and reviewing existing documentation can provide valuable insights. Incorporating measurable metrics, such as cycle times or error rates, enhances the reliability of the process map and supports data-driven decision-making.
Collaboration among stakeholders is essential for successful process mapping. Teams should involve representatives from all relevant departments to ensure a shared understanding of the workflow. Tools like swimlane diagrams can facilitate this collaboration by visually separating responsibilities and highlighting areas where processes cross departmental boundaries. This approach fosters accountability and promotes alignment across teams.
Leveraging advanced tools and techniques further enhances the mapping process. For instance, value stream mapping provides a detailed analysis of workflows, distinguishing value-added activities from non-value-added ones. This tool helps teams identify inefficiencies and eliminate waste, aligning with the principles of six sigma. Digital platforms like Lucidchart or Visio simplify the creation of process maps, offering templates and customization options that streamline the mapping exercise.
Continuous improvement should remain a priority throughout the process mapping journey. Teams must regularly review and update their maps to reflect changes in workflows or organizational goals. Monitoring performance metrics and gathering feedback from stakeholders ensures that the process remains efficient and aligned with business objectives.
By adopting these best practices, systems and teams can unlock the full potential of process mapping. They can overcome common challenges, create actionable maps, and drive measurable improvements in efficiency and quality. For organizations seeking guidance on implementing these strategies, reaching out to us can provide valuable support and expertise.
How Six Sigma Process Mapping Unlocks Success
Aligning Processes with Business Goals
Six sigma process mapping serves as a critical tool for aligning workflows with organizational objectives. By visually representing each step, it provides clarity on how processes contribute to broader business goals. Systems and teams can use this approach to ensure that every activity adds value and supports strategic priorities. For instance, identifying non-value-added tasks allows organizations to redirect resources toward more impactful initiatives.
Process mapping fosters transparency by offering a clear view of operations. This visibility helps decision-makers identify inefficiencies and prioritize improvements that align with key performance indicators. Teams can evaluate whether current workflows meet customer expectations or organizational standards. When processes align with business goals, companies achieve greater consistency, efficiency, and quality in their operations.
Moreover, process mapping lays the foundation for root cause analysis. By pinpointing areas of variability or waste, it enables systems and teams to address underlying issues that hinder performance. This alignment not only enhances operational efficiency but also ensures that processes remain adaptable to changing business needs. Organizations that integrate process mapping into their strategies often experience measurable improvements in productivity and goal achievement.
Driving Continuous Improvement and Innovation
Process mapping plays a pivotal role in driving continuous improvement and fostering innovation. Lean six sigma methodologies emphasize the importance of eliminating waste and reducing variability, and process mapping supports these principles by identifying inefficiencies and bottlenecks. Teams can use this tool to visualize workflows, analyze performance metrics, and implement targeted solutions for process improvement.
Continuous improvement thrives on data-driven decisions, and process mapping integrates measurable metrics into workflows. Metrics such as cycle times, error rates, and resource utilization provide actionable insights that guide optimization efforts. For example, systems and teams can use value stream maps to highlight delays and design future state workflows that enhance efficiency. This iterative approach ensures that processes evolve to meet organizational demands.
Innovation emerges when teams challenge existing workflows and explore new possibilities. Process mapping encourages this mindset by revealing opportunities for redesign and optimization. By streamlining operations, organizations create space for creative problem-solving and strategic growth. Teams that embrace process mapping as a tool for innovation often discover novel ways to enhance quality, reduce costs, and deliver exceptional value to customers.
Incorporating process mapping into lean six sigma initiatives empowers organizations to achieve operational excellence. It supports a culture of continuous improvement by providing a structured framework for analyzing and optimizing workflows. Systems and teams that prioritize this approach unlock the potential for sustained success and innovation. For those seeking to enhance their processes and drive measurable outcomes, reaching out to us can provide valuable guidance and expertise.
Six sigma process mapping stands as a vital tool for achieving business success. It empowers systems and teams to visualize workflows, identify inefficiencies, and implement targeted improvements. By enhancing efficiency, improving quality, and reducing costs, process mapping drives measurable results. Organizations that embrace this methodology often experience smoother operations and greater alignment with their goals.
Embracing process mapping in quality improvement initiatives can lead to transformative results, making operations more efficient and effective.
Readers are encouraged to integrate six sigma process mapping into their strategies. This approach fosters continuous improvement and unlocks the potential for sustained success. For guidance on implementing these practices, reach out to us for expert support.
FAQ
What is Six Sigma Process Mapping?
Six Sigma Process Mapping is a visual tool that represents the steps, interactions, and flow of a process. It helps systems and teams identify inefficiencies, eliminate waste, and improve quality. This method aligns with Six Sigma’s goal of reducing variability and achieving operational excellence. By breaking down processes into manageable steps, it provides clarity and fosters continuous improvement.
Why is Process Mapping important in Six Sigma?
Process Mapping plays a crucial role in Six Sigma by enabling teams to visualize workflows and pinpoint inefficiencies. It supports data-driven decision-making and ensures alignment with organizational goals. According to experts, this tool minimizes variability and enhances quality, making it essential for achieving measurable business success.
“Process Mapping is vital in Six Sigma for boosting efficiency and visualizing processes to pinpoint and remove inefficiencies.” – Six Sigma Process Mapping Expert
What are the key benefits of using Six Sigma Process Mapping?
Six Sigma Process Mapping offers several benefits, including:
Improved efficiency by eliminating redundant steps.
Enhanced quality through reduced defects and variability.
Cost savings by identifying and removing waste.
Better collaboration among teams with clear visual workflows.
Data-driven insights for continuous improvement.
These advantages help systems and teams achieve operational excellence and align processes with business objectives.
What types of process maps are used in Six Sigma?
Six Sigma employs various types of process maps, including:
High-Level Process Maps: Provide an overview of major steps.
Detailed Process Maps: Break down workflows into specific actions.
Swimlane Diagrams: Highlight responsibilities across departments.
Value Stream Maps: Focus on value-added and non-value-added activities.
Each type serves a unique purpose, helping teams analyze and optimize processes effectively.
How does Process Mapping support data-driven decision-making?
Process Mapping integrates measurable metrics, such as cycle times and error rates, into workflows. These metrics provide actionable insights that guide teams in identifying inefficiencies and implementing targeted improvements. For example, value stream maps highlight delays and waste, enabling systems and teams to design optimized workflows based on evidence rather than assumptions.
Can Process Mapping be applied to industries outside manufacturing?
Yes, Process Mapping is versatile and applies to various industries, including healthcare, logistics, and service sectors. For instance, hospitals use swimlane diagrams to streamline patient care processes, while logistics companies rely on value stream maps to optimize supply chains. Its adaptability makes it a valuable tool for any organization seeking to improve efficiency and quality.
What challenges do teams face when creating process maps?
Teams often encounter challenges such as:
Difficulty defining the process scope.
Incomplete or inaccurate data collection.
Resistance to change from stakeholders.
Complexity in visualizing intricate workflows.
Using tools like SIPOC diagrams and involving cross-functional teams can help overcome these obstacles. Continuous review and updates ensure the process map remains relevant and effective.
How does Process Mapping contribute to cost reduction?
Process Mapping identifies areas where resources are underutilized or misallocated. By eliminating waste and optimizing workflows, teams can reduce operational costs. For example, a logistics company might uncover inefficiencies in its supply chain, leading to significant savings. This approach aligns with Six Sigma’s focus on achieving high-quality outcomes at lower costs.
Who developed the Six Sigma methodology?
Bill Smith, an engineer at Motorola, developed the Six Sigma methodology in 1986. He combined innovative quality improvement methods from the preceding decades to create a structured approach for reducing defects and improving processes. The term “Six Sigma” originates from process capability statistics, aiming for fewer than 3.4 defects per million opportunities.
“Six Sigma’s goal is to improve overall processes to that level of quality or better.” – Six Sigma Process Mapping Expert
How can organizations get started with Six Sigma Process Mapping?
Organizations can begin by defining the process scope and objectives, gathering accurate data, and visualizing workflows using tools like flowcharts or value stream maps. Teams should analyze the process to identify inefficiencies and implement targeted improvements. For guidance and support, systems and teams can reach out to experts who specialize in Six Sigma methodologies.