Understanding Process Improvement Methodologies and Their Benefits
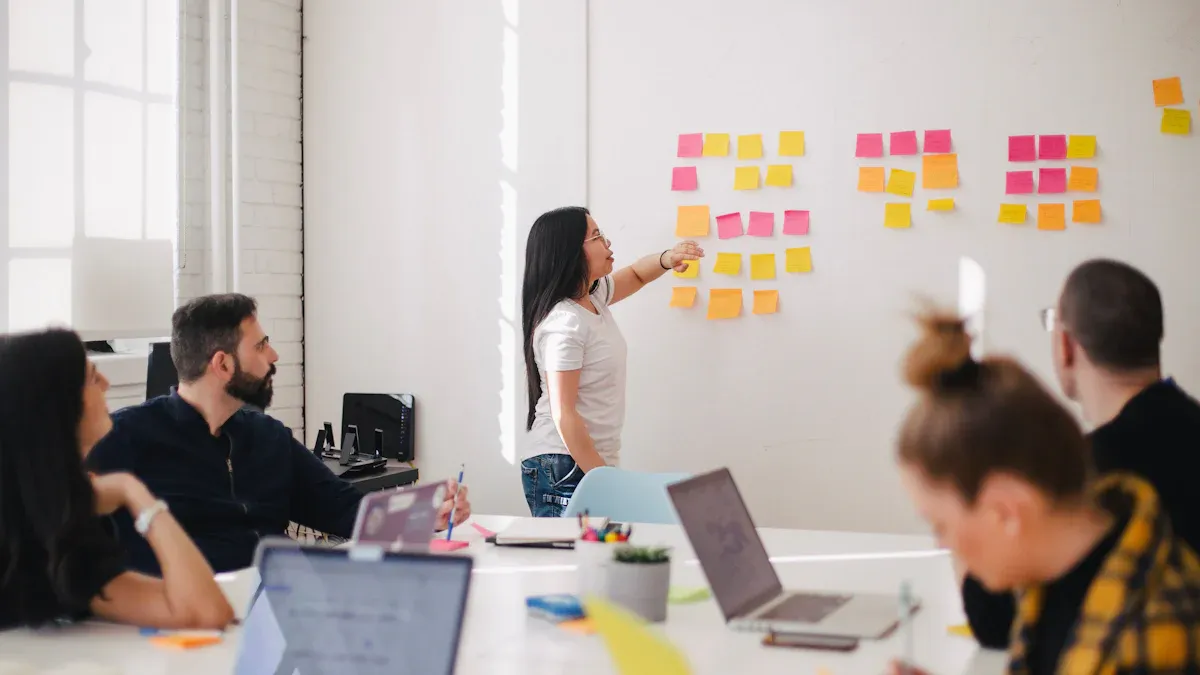
Process improvement methodologies provide structured approaches that help organizations refine workflows, reduce inefficiencies, and enhance overall performance in business management. These methodologies rely on data-driven strategies to address challenges and optimize outcomes across systems and teams, particularly in the realm of sales. In today's fast-paced world, improving processes has become essential for organizations to remain competitive and meet evolving customer expectations.
Organizations adopting these methodologies often experience significant transformations. For example:
Productivity increases by 20–30%, enabling teams to accomplish more with fewer resources.
Defect rates drop by up to 40%, ensuring higher-quality outputs.
Operational costs decrease by 15–25%, contributing to sustainable growth.
Resource utilization improves by 30–40%, while waste reduces by 20–30%.
By leveraging a methodology for process improvement, businesses gain the knowledge needed to make informed decisions, align processes with customer needs, and foster long-term success. Structured approaches like Six Sigma have also shown measurable benefits, such as enhanced employee productivity and a rebound in performance metrics post-adoption. These methodologies empower systems and teams to achieve impactful results, making them indispensable tools for modern organizations in the competitive landscape of business management.
Key Takeaways
Process improvement methods help businesses work better and faster.
Using Six Sigma can boost productivity by 20-30% and cut mistakes by 40%.
Lean focuses on removing waste, saving 15-25% in costs and improving work speed.
Agile helps teams stay flexible, work together, and finish tasks quickly.
Total Quality Management (TQM) involves everyone to make quality a priority.
Kaizen encourages small changes that add up to big improvements over time.
The Plan-Do-Check-Act (PDCA) cycle helps test and improve processes step by step.
Picking the right method depends on your goals, problems, and resources.
Key Process Improvement Methodologies
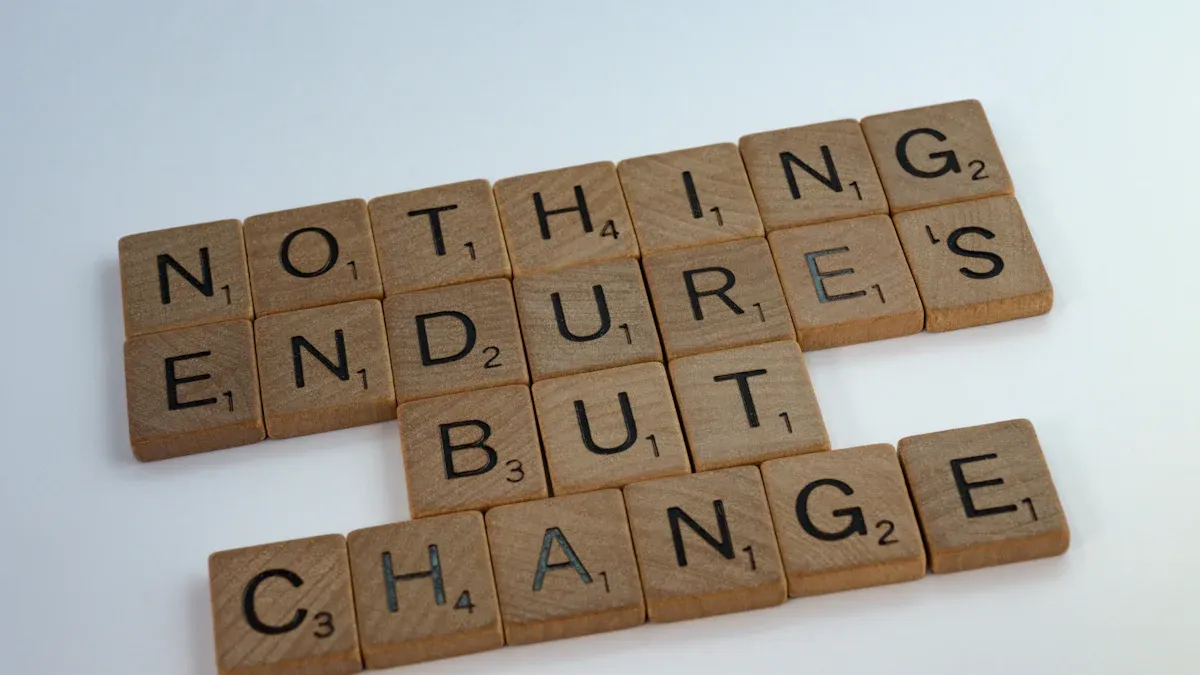
Six Sigma
Principles of Six Sigma
Six Sigma focuses on reducing variability and defects in processes by using data-driven techniques. It operates on two main methodologies: DMAIC (Define, Measure, Analyze, Improve, Control) for existing processes and DMADV (Define, Measure, Analyze, Design, Verify) for new processes. These frameworks rely on statistical tools to identify inefficiencies and implement solutions. Six Sigma emphasizes achieving near-perfection, with a goal of 3.4 defects per million opportunities.
The methodology encourages a structured approach to problem-solving. Teams often include certified professionals, such as Green Belts and Black Belts, who lead improvement projects. By prioritizing measurable outcomes, Six Sigma ensures that changes deliver tangible benefits.
Common Use Cases for Six Sigma
Organizations across industries use Six Sigma to enhance quality and efficiency. For example:
Manufacturing: Reducing defect rates and improving production consistency.
Healthcare: Streamlining patient care processes and minimizing errors in medical procedures.
Finance: Enhancing transaction accuracy and reducing processing times.
Companies like General Electric and Motorola have reported significant results. General Electric achieved nearly $700 million in benefits within two years, eventually surpassing $2.5 billion in five years. Motorola reduced product defect rates by over 80%, saving more than $16 billion. These examples highlight the transformative potential of this methodology for process improvement.
Measurable Outcome | Description |
---|---|
Defect reduction | Significant decrease in defects or errors, tracked using tools like Pareto charts. |
Process efficiency gains | Streamlined workflows and reduced cycle times, assessed through metrics like throughput. |
Cost savings | Lower operational costs due to reduced waste and improved resource utilization. |
Customer satisfaction | Improved customer satisfaction scores (CSAT) and net promoter scores (NPS) post-implementation. |
Employee engagement | Increased participation in improvement projects and positive feedback from teams. |
Lean
Core Concepts of Lean Methodology
Lean methodology aims to maximize value for customers by eliminating waste and optimizing workflows. It identifies seven types of waste, including overproduction, waiting, and unnecessary motion. Lean principles focus on continuous improvement, empowering employees to suggest and implement changes.
A key concept in Lean is "value stream mapping," which visualizes the flow of materials and information. This tool helps organizations identify bottlenecks and streamline processes. Lean also emphasizes "just-in-time" production, ensuring resources are used efficiently without overstocking.
Examples of Lean in Practice
Lean has delivered measurable outcomes in various sectors. In manufacturing, it reduces lead times by 70-90% and decreases costs by 25-30%. Healthcare organizations have also benefited. For instance:
Patient treatment times dropped from 187 to 60 days.
Overtime reduced by 75%, saving costs and improving staff well-being.
Workload decreased by 70 minutes per team, enhancing productivity.
Statistic | Description |
---|---|
70% Reduction in Lead Time | Lean principles reduce production lead times by 70-90%. |
25-30% Decrease in Costs | Manufacturers achieve 25-30% reductions in costs post-lean implementation. |
80% Improvement in Quality | Lean manufacturers see an average 80% reduction in defects. |
35% Increase in Productivity | Lean implementations yield a 35% increase in productivity within a year. |
200% Return on Investment | Properly executed lean initiatives deliver an average 200% ROI in 12-18 months. |
These results demonstrate how Lean methodology for process improvement can drive efficiency and cost savings while maintaining high-quality standards.
Agile
Agile Principles and Iterative Processes
Agile methodology emphasizes flexibility, collaboration, and iterative progress. It breaks projects into smaller, manageable increments called "sprints," allowing teams to adapt quickly to changes. Agile promotes continuous feedback from stakeholders, ensuring the final product aligns with user needs.
The Agile Manifesto outlines four core values:
Individuals and interactions over processes and tools.
Working software over comprehensive documentation.
Customer collaboration over contract negotiation.
Responding to change over following a plan.
These principles foster a dynamic work environment where teams can innovate and respond to challenges effectively.
Applications of Agile in Various Industries
Agile originated in software development but has since expanded to other fields. In technology, it accelerates product development cycles and improves time-to-market. Marketing teams use Agile to create adaptive campaigns that respond to consumer trends. Even education has adopted Agile principles to enhance curriculum design and delivery.
Companies like Honeywell have leveraged Agile to improve on-time delivery and product reliability, generating $1.2 billion from productivity improvements. This methodology for process improvement enables organizations to remain competitive in fast-changing markets.
Total Quality Management (TQM)
Principles of TQM
Total Quality Management (TQM) is a methodology for process improvement that emphasizes a holistic approach to achieving long-term success through customer satisfaction. It focuses on continuous improvement across all organizational functions, involving every employee in the process. TQM principles include:
Customer Focus: Understanding and meeting customer needs is central to TQM.
Employee Involvement: Empowering employees to contribute to quality improvements fosters ownership and accountability.
Process Approach: Viewing activities as interconnected processes ensures efficiency and consistency.
Continuous Improvement: Regularly evaluating and enhancing processes leads to sustained growth.
Fact-Based Decision Making: Using data and analysis to guide decisions ensures accuracy and reliability.
These principles create a culture of quality that permeates every aspect of an organization, driving better outcomes and fostering innovation.
Use Cases of TQM in Organizations
Organizations across industries have successfully implemented TQM to improve performance. For example:
Manufacturing: Companies use TQM to reduce defects and enhance production efficiency.
Healthcare: Hospitals adopt TQM to improve patient care and safety.
Education: Schools implement TQM to enhance teaching methods and student outcomes.
Empirical studies validate the effectiveness of TQM practices. The table below highlights findings from two key studies:
Study Title | Findings |
---|---|
TQM implementation: an empirical examination and proposed generic model | Organizations that implemented TQM reported increased market share and improved competitiveness. A cause-and-effect relationship between TQM practices and enhanced corporate performance was established. |
An Empirical Study of the Contribution of Total Quality Management to Occupational Safety and Health Performance in Saudi Organizations | TQM practices significantly positively impacted occupational safety and health performance in Saudi organizations, indicating a strong relationship between TQM and performance. |
These examples demonstrate how TQM can drive measurable improvements in quality, safety, and overall organizational performance.
Continuous Improvement (Kaizen)
Philosophy and Principles of Kaizen
Kaizen, a Japanese term meaning "change for the better," embodies the philosophy of continuous improvement. It encourages small, incremental changes rather than large-scale transformations. Kaizen principles include:
Employee Empowerment: Involving employees at all levels fosters collaboration and innovation.
Standardization: Establishing clear standards ensures consistency and facilitates improvement.
Waste Reduction: Identifying and eliminating waste enhances efficiency and reduces costs.
Problem Solving: Using tools like root cause analysis helps address issues effectively.
Kaizen promotes a culture of ongoing improvement, enabling organizations to adapt and thrive in dynamic environments.
Examples of Kaizen in Action
Organizations implementing Kaizen principles often achieve significant improvements. The table below illustrates measurable outcomes:
Metric | Before Implementation | After Implementation |
---|---|---|
15 | 5 | |
Downtime per shift due to misplacement | 10% | 2% |
Employee satisfaction (scale of 1-10) | 6 | 9 |
Additional benefits include:
Efficiency Gains: Increased productivity post-implementation.
Cost Reduction: Savings achieved through process optimization.
Quality Improvement: Decrease in defects or errors.
These results highlight the transformative impact of Kaizen on organizational performance and employee morale.
Plan-Do-Check-Act (PDCA) Cycle
Steps in the PDCA Cycle
The Plan-Do-Check-Act (PDCA) cycle is a systematic approach to continuous improvement. It consists of four steps:
Plan: Identify problems, set objectives, and develop strategies to address them.
Do: Implement the planned actions on a small scale to test their effectiveness.
Check: Evaluate the results by comparing them to the objectives.
Act: Standardize successful changes and apply them on a larger scale.
This iterative process ensures that improvements are sustainable and adaptable to changing conditions.
Applications of PDCA in Process Improvement
The PDCA cycle has been widely adopted across industries to enhance performance. For example:
Manufacturing: Companies use PDCA to reduce defects and improve production efficiency.
Healthcare: Hospitals apply PDCA to streamline patient care and reduce errors.
Education: Schools use PDCA to refine teaching methods and improve student outcomes.
Statistics validate the effectiveness of PDCA in enhancing process performance:
Description | |
---|---|
Timeliness | Metrics such as throughput, cycle time, and delivery dates help assess efficiency. |
Product Quality | Measures like defect rates, rework volume, and product reliability provide insights into output quality. |
Service Quality | Responsiveness, trustworthiness, and service reliability are critical for evaluating service quality. |
Cost | Analysis of labor, material, overhead, and rework costs to understand financial efficiency. |
Customer Satisfaction | Customer feedback and satisfaction levels indicate if expectations are met. |
The PDCA cycle provides a structured framework for organizations to achieve continuous improvement and maintain high standards of quality.
Comparing Methodologies
Key Differences Between Six Sigma, Lean, Agile, and Others
Each methodology for process improvement offers unique strengths and focuses, making them suitable for different organizational needs. Six Sigma prioritizes data-driven decision-making to reduce defects and improve quality. It uses statistical tools and structured frameworks like DMAIC to achieve measurable results. Lean, on the other hand, emphasizes waste elimination to maximize customer value. It focuses on streamlining workflows and improving efficiency by identifying and removing non-value-adding activities.
Agile stands out for its flexibility and iterative approach. It breaks projects into smaller increments, allowing teams to adapt quickly to changes and deliver results faster. Agile fosters collaboration and continuous feedback, making it ideal for dynamic industries like software development. Total Quality Management (TQM) takes a holistic approach, involving every employee in the organization to achieve long-term success through continuous improvement and customer satisfaction.
Kaizen focuses on small, incremental changes that collectively lead to significant improvements over time. It empowers employees to identify inefficiencies and implement solutions, fostering a culture of continuous improvement. The Plan-Do-Check-Act (PDCA) cycle provides a systematic framework for testing and refining processes. It emphasizes iterative learning and adaptation, making it versatile across industries.
Understanding these distinctions helps organizations choose the right methodology. For example, Six Sigma suits industries requiring precision and defect reduction, such as manufacturing. Lean works well in environments where waste elimination and efficiency are critical, like healthcare. Agile thrives in fast-paced sectors needing adaptability, while TQM and Kaizen are effective for organizations aiming to build a culture of quality and continuous improvement.
Note: While specific comparative statistics are unavailable, each methodology's unique focus—whether on data, waste, flexibility, or incremental change—guides its application in different contexts.
How to Determine Which Methodology Fits Your Needs
Selecting the right methodology begins with assessing organizational goals and challenges. Start by identifying pain points in current processes. Are defects or errors a recurring issue? Six Sigma may provide the structured approach needed to address them. If inefficiencies and waste hinder productivity, Lean could be the solution.
Consider the nature of your industry and the pace of change it demands. Agile suits industries like technology, where rapid adaptation is essential. For organizations seeking to involve all employees in quality improvement, TQM or Kaizen may align better with their culture and objectives.
Evaluate the resources and expertise available within your organization. Six Sigma often requires certified professionals, while Lean and Kaizen rely more on employee involvement and training. The PDCA cycle offers a simpler, iterative approach that can be implemented with minimal resources.
Finally, think about scalability and long-term goals. If your organization aims for continuous improvement, methodologies like Kaizen or TQM can foster a sustainable culture of growth. For short-term, project-specific improvements, Agile or Six Sigma may deliver faster results.
Tip: Organizations should pilot a methodology on a small scale before full implementation. This approach allows teams to evaluate its effectiveness and make adjustments as needed.
Benefits of Process Improvement Methodologies
Enhanced Efficiency
How methodologies streamline workflows
Process improvement methodologies enhance efficiency by identifying and eliminating bottlenecks in workflows. Techniques like Lean focus on removing non-value-adding activities, while Six Sigma uses data-driven tools to reduce variability. Agile, with its iterative approach, ensures teams can adapt quickly to changing requirements. These methodologies encourage systems and teams to standardize processes, which minimizes delays and improves task coordination.
For example, Lean's value stream mapping helps visualize workflows, enabling organizations to pinpoint inefficiencies. Similarly, the Plan-Do-Check-Act (PDCA) cycle provides a structured framework for testing and refining processes. By streamlining workflows, organizations can allocate resources more effectively and focus on high-priority tasks.
Examples of efficiency improvements
Organizations adopting these methodologies often report measurable efficiency gains. The table below highlights key improvements:
Improvement Type | Description |
---|---|
Increased productivity | Faster task completion allows teams to focus on higher value-added activities, boosting overall productivity. |
Reduced inefficiencies | Identifying and eliminating redundant tasks and waste enhances workflow and operational efficiency. |
Increased quality | Optimizing production processes minimizes errors and defects, ensuring consistent quality standards. |
Reduced costs | Streamlining operations and resource use leads to lower operational expenses. |
Improved customer satisfaction | Consistent quality and timely delivery strengthen customer trust and loyalty. |
Adaptability and agility | Optimized processes enable better adaptation to regulations and evolving customer expectations. |
Competitive advantage | Continuous process improvement positions organizations favorably in the marketplace. |
These outcomes demonstrate how methodologies for process improvement drive operational excellence and long-term success.
Cost Reduction
Identifying and eliminating waste
Cost reduction is a critical benefit of process improvement methodologies. Lean, for instance, identifies seven types of waste, including overproduction, waiting, and unnecessary motion. By addressing these inefficiencies, organizations can significantly lower operational expenses. Six Sigma complements this by reducing defects, which minimizes rework and associated costs.
Kaizen, with its focus on incremental changes, empowers employees to suggest cost-saving measures. This collaborative approach ensures that waste reduction becomes an ongoing effort across all levels of the organization.
Real-world examples of cost savings
Real-world applications highlight the financial impact of these methodologies. For example:
Six Sigma has led to annualized cost savings of approximately $19,729 in operating rooms by improving the efficiency of surgical instrument sterilization.
A 0.25 σ improvement (+5.2%) in process performance corresponds to these savings, showcasing the economic benefits of systematic process optimization.
These examples underscore the potential for organizations to achieve substantial cost reductions through targeted process improvements.
Improved Quality
Ensuring consistency and reducing errors
Process improvement methodologies prioritize quality by standardizing processes and reducing errors. Six Sigma's data-driven approach ensures consistency by addressing root causes of defects. TQM fosters a culture of quality by involving every employee in continuous improvement efforts. Agile, with its focus on iterative development, incorporates regular feedback to align outputs with customer expectations.
Tracking quality improvement metrics is essential for maintaining high standards. Organizations use both quantitative and qualitative measures to monitor progress. Key performance indicators, such as defect rates and customer satisfaction scores, provide actionable insights for refining processes.
Case studies of quality improvements
Organizations that adopt these methodologies often achieve remarkable quality improvements. For instance:
Tracking metrics like close rates and trial month outcomes helps organizations optimize operational excellence.
Establishing measurable benchmarks over time ensures sustained quality enhancement.
Qualitative insights from employee feedback highlight areas needing further training or adjustment.
These practices enable systems and teams to deliver consistent, high-quality results, fostering customer trust and loyalty.
Increased Customer Satisfaction
Aligning processes with customer needs
Organizations achieve higher customer satisfaction by aligning their processes with customer needs. Structured methodologies like Lean focus on eliminating waste and ensuring that products and services deliver maximum value. Six Sigma reduces defects, ensuring consistent quality that meets customer expectations. Agile adapts processes to changing requirements, enabling faster delivery and improved responsiveness.
Streamlined workflows enhance delivery reliability and shorten lead times. These improvements allow businesses to respond more effectively to customer demands. For example, Lean methodologies help identify bottlenecks in production, ensuring timely delivery of goods. Agile principles enable teams to incorporate customer feedback during development, ensuring the final product aligns with user preferences.
Tip: Organizations should regularly evaluate customer feedback to refine processes and maintain alignment with evolving needs.
Examples of improved customer experiences
Process improvement methodologies have a measurable impact on customer satisfaction. Organizations adopting these approaches report significant benefits:
Enhanced operational efficiency leads to faster service delivery.
Reduced defects ensure higher-quality products.
Improved reliability strengthens customer trust.
For instance, Lean principles have helped companies reduce lead times by up to 90%, ensuring customers receive their orders promptly. Six Sigma has enabled businesses to achieve near-perfect quality, minimizing complaints and returns. Agile methodologies have improved customer response performance, allowing teams to address issues quickly and effectively.
These examples highlight how methodologies for process improvement create positive customer experiences, fostering loyalty and long-term relationships.
Employee Engagement
Empowering teams through structured approaches
Structured methodologies empower employees by clarifying roles and aligning them with organizational goals. Lean encourages employees to identify inefficiencies and suggest improvements, fostering a sense of ownership. Kaizen promotes collaboration by involving all team members in continuous improvement efforts. Agile enhances engagement by emphasizing teamwork and regular communication.
Clear processes reduce confusion and improve morale. Employees feel more confident when they understand their responsibilities and see how their contributions impact the organization. This empowerment boosts productivity and encourages innovation.
Note: Empowered employees are more likely to take initiative, driving continuous improvement across the organization.
How methodologies foster collaboration
Process improvement methodologies create environments that promote collaboration. Agile relies on cross-functional teams, ensuring diverse perspectives contribute to problem-solving. Lean and Kaizen encourage open communication, enabling employees to share ideas and work together to implement changes.
These methodologies also optimize workflows, reducing inefficiencies that hinder teamwork. Streamlined processes allow teams to focus on shared goals, improving coordination and productivity. For example, organizations using Lean report increased employee engagement due to reduced operational costs and clarified workflows. Agile teams often experience higher morale, as iterative processes provide regular opportunities for feedback and collaboration.
By fostering collaboration, these methodologies strengthen team dynamics and drive organizational success.
How to Choose and Apply the Right Methodology for Process Improvement
Assessing Your Organization’s Needs
Identifying Pain Points and Goals
Organizations must begin by identifying their pain points and defining clear goals. A needs assessment serves as a valuable tool for this process. It helps pinpoint areas requiring improvement and aligns them with organizational objectives. Key questions to guide this assessment include:
What activities are essential to achieving our objectives?
Which key performance indicators (KPIs) measure current performance?
Where do inefficiencies or challenges occur within the process?
Quantifiable measures, such as averages, variances, and trends, provide actionable insights. Averages highlight typical results, while variances reveal deviations that may indicate inefficiencies. Trends track changes over time, helping prioritize areas for improvement. By addressing these questions and metrics, organizations can establish a solid foundation for selecting the right methodology.
Evaluating Current Processes
Evaluating existing processes involves analyzing workflows, identifying bottlenecks, and assessing resource utilization. Tools like value stream mapping and process flowcharts can visualize inefficiencies. Organizations should also review historical data to identify recurring issues, such as delays or defects.
Performance metrics play a critical role in this evaluation. For example, throughput measures the efficiency of production, while defect rates assess quality. By comparing these metrics against industry benchmarks, organizations can determine where improvements are needed. This evaluation ensures that the chosen methodology addresses specific challenges effectively.
Comparing Methodologies
Matching Methodologies to Organizational Goals
Each methodology for process improvement offers unique strengths, making it essential to match the approach to organizational goals. Lean focuses on waste elimination and efficiency, making it ideal for industries like manufacturing and healthcare. Six Sigma emphasizes defect reduction and precision, suiting sectors requiring high-quality standards, such as aerospace and finance. Agile thrives in dynamic environments, enabling rapid adaptation in industries like software development.
A comparative analysis of methodologies highlights their effectiveness for different objectives:
Criteria/Objective | Description |
---|---|
Emphasizes the importance of having a defined approach to process improvement. | |
Clear Objectives | Focuses on setting specific improvement targets based on identified challenges. |
Quantitative Measures | Utilizes data and metrics to guide project selection and implementation. |
Organizations should evaluate these criteria to determine the best fit for their needs. For example, Toyota uses Lean to track daily quality metrics across production areas, while Boeing achieved a 50% reduction in defects using Six Sigma. These examples demonstrate how aligning methodologies with goals leads to measurable success.
Factors to Consider When Choosing a Methodology
Several factors influence the selection of a process improvement methodology. These include:
Industry Requirements: Consider the specific demands of the industry, such as precision in manufacturing or adaptability in technology.
Organizational Culture: Assess whether the organization values employee involvement (Kaizen) or data-driven decision-making (Six Sigma).
Resource Availability: Evaluate the expertise and tools available, as some methodologies require specialized training or software.
Scalability: Determine whether the methodology can adapt to future growth or changing needs.
Research findings emphasize the importance of evaluating methodologies based on efficiency, flexibility, and stakeholder engagement. This ensures that the chosen approach aligns with both short-term objectives and long-term strategies.
Steps for Implementation
Planning and Preparation
Effective implementation begins with thorough planning. Organizations should establish specific, measurable, achievable, relevant, and time-bound (SMART) goals. These goals define success and maintain focus throughout the process. Engaging stakeholders at this stage ensures diverse perspectives and fosters a culture of collaboration.
Measurable milestones, such as performance indicators and timelines, help track progress. For example, pre-defined metrics like defect rates or cycle times provide benchmarks for evaluating success. By setting clear objectives and involving key stakeholders, organizations create a roadmap for successful implementation.
Training and Team Involvement
Training equips employees with the skills needed to execute the chosen methodology. Workshops, certifications, and hands-on sessions ensure teams understand the principles and tools involved. For instance, Six Sigma requires Green Belt or Black Belt certifications, while Lean emphasizes employee-driven initiatives.
Team involvement is equally critical. Cross-functional teams bring diverse expertise, enhancing problem-solving and innovation. Agile methodologies, for example, rely on collaborative sprints to achieve iterative progress. By fostering teamwork and providing adequate training, organizations empower employees to drive improvements effectively.
Monitoring and Continuous Improvement
Monitoring ensures that the implementation stays on track and delivers desired outcomes. Organizations should use performance metrics, such as throughput and defect rates, to evaluate progress. Regular feedback from employees and stakeholders provides additional insights for refinement.
Continuous improvement is a cornerstone of methodologies like Kaizen and PDCA. These approaches emphasize iterative learning, allowing organizations to adapt and optimize processes over time. For example, the PDCA cycle involves testing changes on a small scale before full implementation, ensuring sustainability. By prioritizing monitoring and ongoing refinement, organizations can maintain high standards and achieve long-term success.
Common Challenges and Solutions
Overcoming Resistance to Change
Resistance to change often emerges as one of the most significant barriers during process improvement initiatives. Employees may feel uncertain about new methodologies or fear that changes could disrupt their routines. This hesitation can slow down progress and hinder the success of improvement efforts. Addressing this challenge requires a proactive and inclusive approach.
Organizations can foster a culture of adaptability by emphasizing the benefits of change. Leaders should communicate the rationale behind proposed improvements, focusing on how these changes align with organizational goals and individual roles. For example, explaining how Lean principles reduce redundant tasks can help employees see the value in adopting new workflows. Open communication channels allow employees to voice concerns and provide feedback, which builds trust and reduces apprehension.
Pilot testing process improvements on a smaller scale can also alleviate resistance. This approach demonstrates tangible benefits without overwhelming teams. For instance, implementing a small-scale Six Sigma project to reduce defects in one department can showcase measurable results, encouraging broader acceptance. Additionally, involving employees in the planning and execution stages empowers them to take ownership of the changes, fostering a sense of collaboration and shared purpose.
Ensuring Long-Term Adoption and Success
Sustaining the benefits of process improvement methodologies requires a commitment to long-term adoption. Many organizations struggle to maintain momentum after the initial implementation phase. Without consistent effort, processes may revert to their previous state, negating the progress made.
To ensure lasting success, organizations should integrate continuous improvement into their culture. Regular training sessions help employees stay updated on methodologies and tools. For example, providing ongoing Lean workshops ensures that teams remain focused on waste reduction and efficiency. Establishing clear policies and procedures also reinforces the importance of maintaining improved processes.
Monitoring progress through key performance indicators (KPIs) is another critical step. Metrics such as defect rates, cycle times, and customer satisfaction scores provide insights into the effectiveness of implemented changes. Organizations can use these metrics to identify areas for further refinement, ensuring that improvements remain aligned with goals.
The table below highlights common challenges encountered during process improvement and corresponding solutions:
Challenge | Solutions |
---|---|
Data Quality and Accessibility | Collaborate with IT teams to ensure data quality standards are maintained. Implement data governance practices to standardize data definitions and improve data integrity. Invest in tools to aggregate and harmonize data from different sources. |
Stakeholder Engagement and Buy-In | Communicate the value of process improvement initiatives, emphasizing benefits like cost savings and efficiency gains. Involve stakeholders early in defining objectives and selecting KPIs. Provide training to build confidence in using data-driven insights. |
Resistance to Change | Foster a culture of continuous improvement by emphasizing agility and adaptability. Communicate the rationale behind changes and address concerns. Pilot test improvements on a small scale to demonstrate tangible results and build confidence. |
Data Privacy and Security Concerns | Ensure compliance with regulations like GDPR or HIPAA. Use anonymization techniques to protect sensitive information. Establish clear policies for data access and storage, with built-in controls to monitor compliance. |
By addressing these challenges with structured solutions, organizations can overcome obstacles and create a foundation for sustained success. Continuous monitoring, employee involvement, and a focus on measurable outcomes ensure that process improvements deliver long-term value.
Real-World Examples of Process Improvement
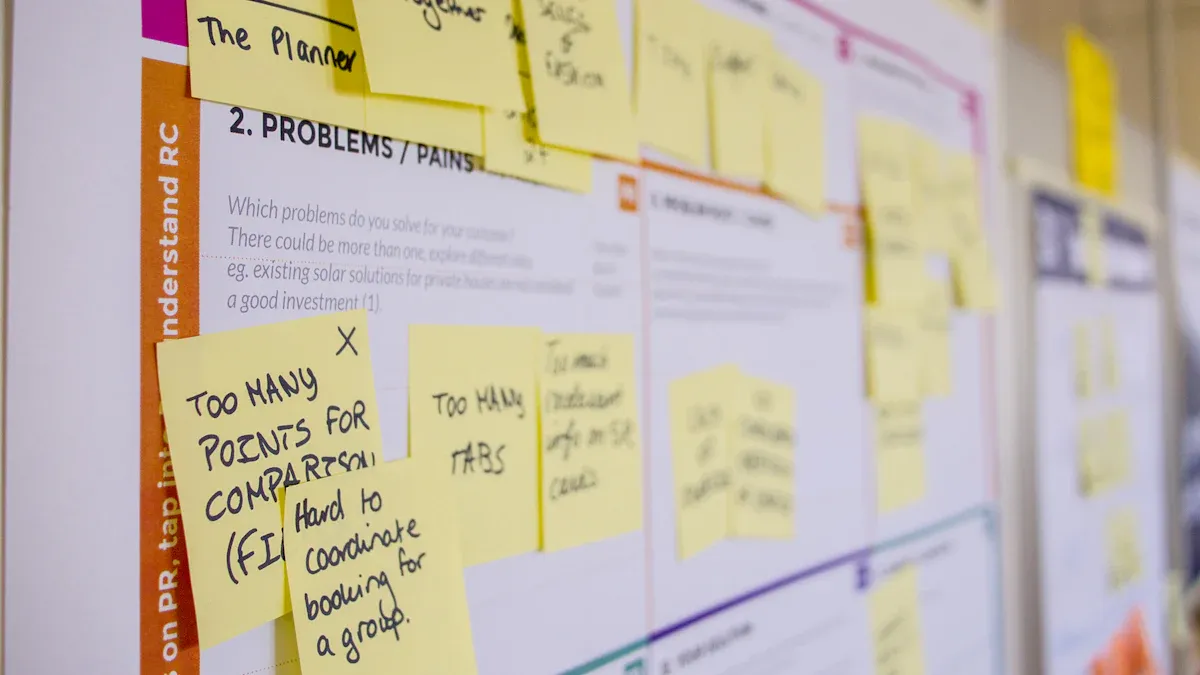
Case Study: Six Sigma in Manufacturing
Problem Identification and Resolution
Manufacturing companies often face challenges related to defects and inefficiencies in production processes. Six Sigma provides a structured approach to address these issues. By using the DMAIC framework, organizations define problems, measure current performance, analyze root causes, implement improvements, and control outcomes. For example, a manufacturing firm identified high defect rates in its assembly line. The team conducted a thorough analysis using statistical tools, pinpointing variability in machine calibration as the primary cause. Adjustments to equipment settings and operator training resolved the issue, reducing defects significantly.
Results Achieved
The application of Six Sigma in manufacturing has delivered measurable improvements. Companies report enhanced operational efficiency, reduced waste, and improved bottom lines. The table below highlights key outcomes:
Sector | Outcome | Description |
---|---|---|
Various | Improved operational efficiency | Companies transformed processes, reduced waste, and improved bottom lines through operational efficiency initiatives. |
Additionally:
Businesses partnering with CarbonSmart USA reduced carbon emissions by 15% within the first year.
Data-driven initiatives led to $5 million in annual cost savings through reduced energy consumption.
Companies achieved a 30% increase in sustainability ratings.
These results demonstrate the effectiveness of Six Sigma in driving both financial and environmental benefits.
Case Study: Lean in Healthcare
Streamlining Patient Care Processes
Healthcare organizations often struggle with inefficiencies that impact patient care. Lean methodology addresses these challenges by eliminating waste and optimizing workflows. Hospitals have used Lean principles to reduce wait times, improve medication accuracy, and enhance overall patient experiences. For instance, value stream mapping helped one hospital identify bottlenecks in its emergency department. By reallocating resources and standardizing procedures, the hospital reduced patient wait times and improved throughput.
Outcomes and Benefits
Lean has delivered significant quantitative improvements in healthcare. The table below outlines key outcomes:
Improvement Area | Quantitative Outcome |
---|---|
Medication Errors | |
Hospital-Acquired Infections | 40% decrease |
Wait Times | 35% reduction |
Throughput | 25-30% improvement |
Operating Costs | 15-20% reduction |
These results highlight how Lean methodology enhances patient safety, reduces costs, and improves operational efficiency. Hospitals adopting Lean principles have also reported higher staff satisfaction due to streamlined workflows and reduced overtime.
Case Study: Agile in Software Development
Iterative Development and Delivery
Agile methodology has revolutionized software development by emphasizing flexibility and iterative progress. Teams break projects into smaller tasks, known as sprints, allowing them to adapt quickly to changes. Regular feedback from stakeholders ensures alignment with user needs. For example, a software company used Agile to develop a customer relationship management (CRM) tool. By incorporating stakeholder input during each sprint, the team delivered a product that met user expectations while reducing development time.
Success Metrics
Agile success is validated through performance metrics that measure efficiency and adaptability. The table below highlights key metrics:
Metric | Description | Importance in Agile Methodologies |
---|---|---|
A unit of measure for estimating the effort required for tasks and user stories. | Enhances agility by allowing teams to adapt to changes and uncertainties. | |
Velocity | Measures the amount of work completed in a specific timeframe, typically in Story Points. | Helps teams predict their capacity and set realistic goals based on past performance. |
Sprint Burndown | A visual representation of work completed versus work remaining in a sprint. | Provides insight into the team's progress and helps identify potential issues early. |
Lead Time | The total time taken from the start of a task to its completion. | Indicates the efficiency of the development process and helps in identifying bottlenecks. |
Cycle Time | The time taken to complete a task from start to finish. | Useful for measuring the speed of delivery and improving workflow efficiency. |
These metrics demonstrate how Agile enables teams to deliver high-quality software efficiently while maintaining flexibility to address evolving requirements.
Case Study: Kaizen in Retail
Incremental Improvements in Inventory Management
Retail organizations often face challenges in managing inventory efficiently. Kaizen, with its focus on continuous improvement, offers a practical solution. By encouraging employees to identify inefficiencies and propose small, incremental changes, Kaizen helps streamline inventory processes. This approach ensures that stock levels align with customer demand, reducing overstocking and stockouts.
Lean inventory management, a key aspect of Kaizen, emphasizes waste reduction and process refinement. Retailers adopting this methodology regularly review their workflows to eliminate errors and inefficiencies. For example, a study by the Lean Enterprise Institute found that companies engaged in continuous process refinement adapt more effectively to market changes. This adaptability gives them a competitive edge in the fast-paced retail sector.
Key benefits of Kaizen in inventory management include:
Reduced errors: Regular process reviews minimize mistakes in stock tracking and ordering.
Improved efficiency: Streamlined workflows enhance operational performance.
Better adaptability: Continuous improvement fosters resilience to market fluctuations.
Retailers implementing Kaizen also report significant improvements in delivery experiences. By optimizing inventory processes, they ensure timely restocking and order fulfillment, which directly impacts customer satisfaction.
Positive Impacts on Customer Satisfaction
Kaizen’s influence extends beyond operational efficiency to customer satisfaction. Streamlined inventory processes enable retailers to meet customer expectations consistently. Products remain available when needed, and delivery times improve. These factors contribute to a positive shopping experience, fostering customer loyalty.
A customer-centric approach, supported by Kaizen principles, enhances service delivery. Retailers focus on aligning their operations with customer needs, creating a seamless experience. For instance:
Faster delivery: Optimized inventory systems reduce delays in order fulfillment.
Consistent availability: Improved stock management ensures products are always in stock.
Enhanced trust: Reliable service builds stronger relationships with customers.
Retailers practicing Kaizen often see measurable results. Streamlining inventory and delivery processes not only boosts operational efficiency but also strengthens customer trust. This dual impact highlights Kaizen’s value in creating a sustainable, customer-focused retail environment.
Case Study: PDCA in Education
Enhancing Teaching Methodologies
Educational institutions use the PDCA cycle to refine teaching methodologies and improve learning outcomes. The iterative nature of PDCA—Plan, Do, Check, Act—allows educators to test new strategies, evaluate their effectiveness, and implement successful changes. For example, teachers may plan a new instructional approach, apply it in the classroom, assess student performance, and adjust the method based on results.
This structured framework encourages continuous improvement in teaching practices. Schools adopting PDCA often focus on specific goals, such as enhancing student engagement or improving test scores. By analyzing performance metrics, educators identify areas needing attention and develop targeted interventions.
Key benefits of PDCA in education include:
Improved teaching strategies: Iterative testing refines instructional methods.
Data-driven decisions: Performance metrics guide adjustments to teaching practices.
Enhanced collaboration: Teachers work together to share insights and best practices.
PDCA fosters a culture of innovation in education, ensuring that teaching methodologies evolve to meet the needs of diverse learners.
Measurable Improvements in Student Outcomes
The PDCA cycle’s impact on education is evident in measurable improvements in student outcomes. Schools using this methodology report higher test scores, increased engagement, and better retention rates. For instance, a school implementing PDCA to address low math scores saw a 20% improvement within a year.
Performance metrics play a crucial role in tracking progress. Educators use tools like standardized tests, attendance records, and feedback surveys to evaluate the effectiveness of their strategies. These insights inform further refinements, creating a cycle of continuous improvement.
Tip: Schools can maximize PDCA’s benefits by involving students in the process. Encouraging feedback from learners helps tailor teaching methods to their needs.
By adopting PDCA, educational institutions create dynamic learning environments that adapt to challenges and foster academic success. This methodology ensures that teaching practices remain effective and responsive to student needs.
Process improvement methodologies play a vital role in helping organizations enhance efficiency, reduce costs, and improve quality. These structured approaches empower systems and teams to identify inefficiencies, implement solutions, and achieve measurable results. By adopting a methodology for process improvement, businesses can align their processes with customer needs and foster long-term success.
Organizations should evaluate their goals, assess current processes, and select the methodology that best fits their needs. Whether focusing on waste reduction, defect elimination, or iterative progress, these methodologies provide a clear path to operational excellence. Readers are encouraged to explore these approaches and take the first step toward transforming their systems and teams. For more insights, reach out to us to learn how these methodologies can benefit your organization.
FAQ
What is a methodology for process improvement?
A methodology for process improvement is a structured approach that organizations use to enhance workflows, reduce inefficiencies, and achieve better outcomes. It provides tools and techniques to identify problems, implement solutions, and sustain improvements.
How do organizations choose the right methodology?
Organizations assess their goals, challenges, and resources to select the most suitable methodology. For example, Lean focuses on waste reduction, while Six Sigma emphasizes defect elimination. The choice depends on the specific needs of the organization.
Can multiple methodologies be combined?
Yes, organizations often combine methodologies to address complex challenges. For instance, Lean and Six Sigma are frequently integrated to maximize efficiency and quality. This hybrid approach leverages the strengths of both methodologies.
What industries benefit from process improvement methodologies?
Industries such as manufacturing, healthcare, software development, and education benefit significantly. These methodologies help streamline operations, improve quality, and enhance customer satisfaction across diverse sectors.
How long does it take to see results?
The timeline varies based on the methodology and scope of implementation. Small-scale improvements using Kaizen may show results within weeks, while larger Six Sigma projects might take months to deliver measurable outcomes.
Are these methodologies suitable for small businesses?
Yes, small businesses can adopt methodologies like Kaizen or PDCA, which require fewer resources. These approaches focus on incremental improvements, making them accessible and effective for smaller organizations.
What role do employees play in process improvement?
Employees play a critical role by identifying inefficiencies, suggesting solutions, and implementing changes. Methodologies like Kaizen and Lean emphasize employee involvement, fostering a culture of collaboration and innovation.
How do organizations measure success?
Organizations use key performance indicators (KPIs) such as defect rates, cycle times, and customer satisfaction scores. These metrics provide insights into the effectiveness of the chosen methodology and guide further improvements.