Top Methods for Process Improvement You Can Use Today
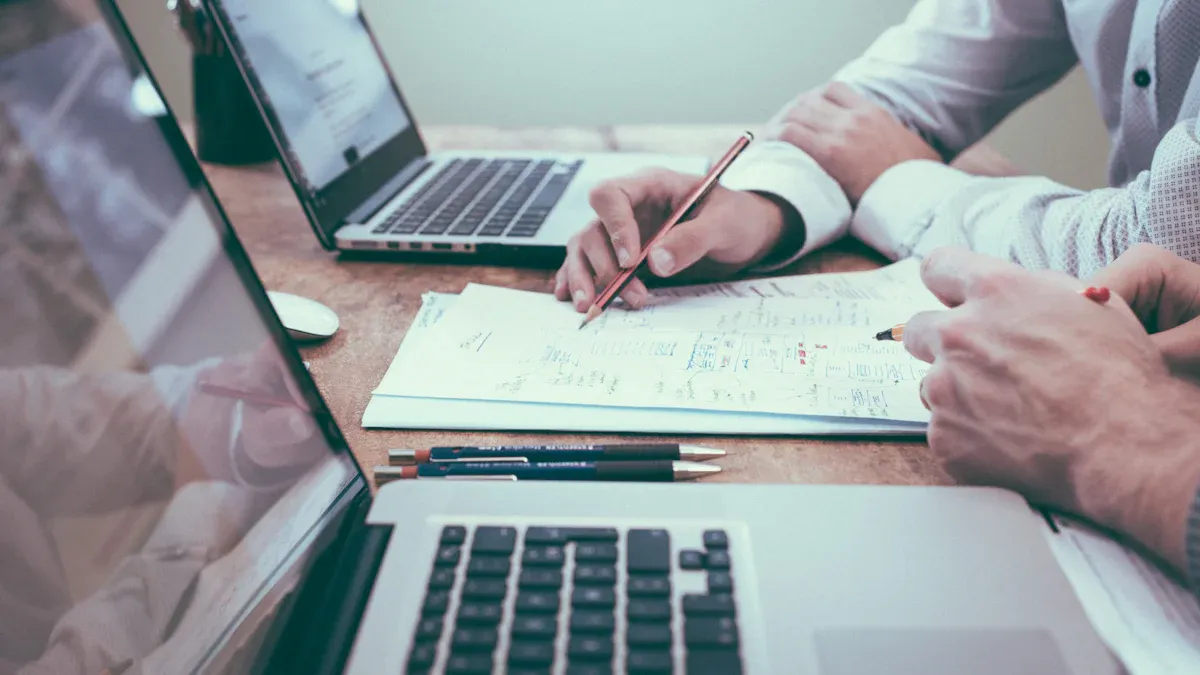
Improving processes is essential for organizations aiming to enhance efficiency and achieve long-term success. Studies show that businesses focusing on process improvement often experience remarkable results: a 20% increase in operational efficiency within the first year, a 40% reduction in production defects over five years, and a 30% decrease in operational costs. These improvements not only streamline systems but also lead to a 25% boost in customer satisfaction.
Teams can start small by identifying bottlenecks and implementing a methodology for process improvement that aligns with their goals. With the right resources and commitment, even incremental changes can create significant impacts. Taking the first step today can set the foundation for a more productive and successful future.
Key Takeaways
Improving processes saves time and money, making customers happier.
Start small by finding problem areas in work to fix first.
Pick the best method for your team, like Lean to cut waste or Six Sigma to improve quality.
Get workers involved to encourage teamwork and responsibility.
Set clear goals and use KPIs to check progress and success.
Always aim to improve so you can stay flexible and compete.
Share ideas clearly to avoid pushback and show the benefits.
Check and update processes often to keep improving and meet goals.
Understanding the Methodology for Process Improvement
What Is Process Improvement?
Process improvement refers to the systematic approach of analyzing and enhancing existing workflows to achieve better outcomes. It involves identifying inefficiencies, eliminating waste, and optimizing processes to align with organizational goals. This methodology can be applied across industries, from manufacturing to healthcare, to improve productivity and quality.
Several methodologies support process improvement efforts:
Agile methodology promotes flexibility and iterative progress.
Six Sigma focuses on reducing defects and variability using the DMAIC process.
Lean manufacturing emphasizes waste elimination to reduce costs.
Total Quality Management (TQM) aims to enhance customer satisfaction through continuous improvement.
Business Process Reengineering (BPR) involves radical redesigns of workflows for significant gains.
Kaizen fosters a culture of incremental, ongoing improvements.
Each approach offers unique tools and techniques, making it essential to choose the right methodology for process improvement based on organizational needs.
Why Process Improvement Matters
In today’s competitive business environment, process improvement plays a critical role in achieving operational excellence. By refining workflows, organizations can reduce costs, improve efficiency, and enhance customer satisfaction. For example, Toyota’s adoption of Lean Manufacturing principles in the 1950s revolutionized production efficiency and quality control, setting a benchmark for the automotive industry.
Research highlights the importance of process improvement in driving business success. Organizations that prioritize this approach often experience measurable benefits, such as shorter cycle times, higher customer satisfaction scores, and streamlined operations. Key performance indicators (KPIs) like these help businesses track progress and align processes with strategic objectives.
Key Benefits of Process Improvement
Implementing a methodology for process improvement offers several advantages:
Increased Efficiency: Streamlined workflows reduce time and resource wastage. Amazon, for instance, optimized its order fulfillment processes through automation, achieving faster deliveries and higher customer satisfaction.
Cost Savings: Eliminating inefficiencies leads to significant cost reductions. Accident Fund, for example, eliminated 100 non-value-adding projects, saving resources and earning national recognition.
Enhanced Quality: Continuous evaluation ensures consistent quality improvements. Merchants Insurance Group improved on-time project delivery to 80%, boosting revenue and client trust.
Employee Engagement: Involving employees in improvement efforts fosters a sense of ownership and collaboration. Kaizen, for instance, encourages all team members to contribute ideas for incremental changes.
Customer Satisfaction: Better processes lead to improved products and services, enhancing the overall customer experience.
By adopting a structured approach to process improvement, organizations can achieve long-term success and adaptability in a rapidly changing market.
Top Methodologies for Process Improvement
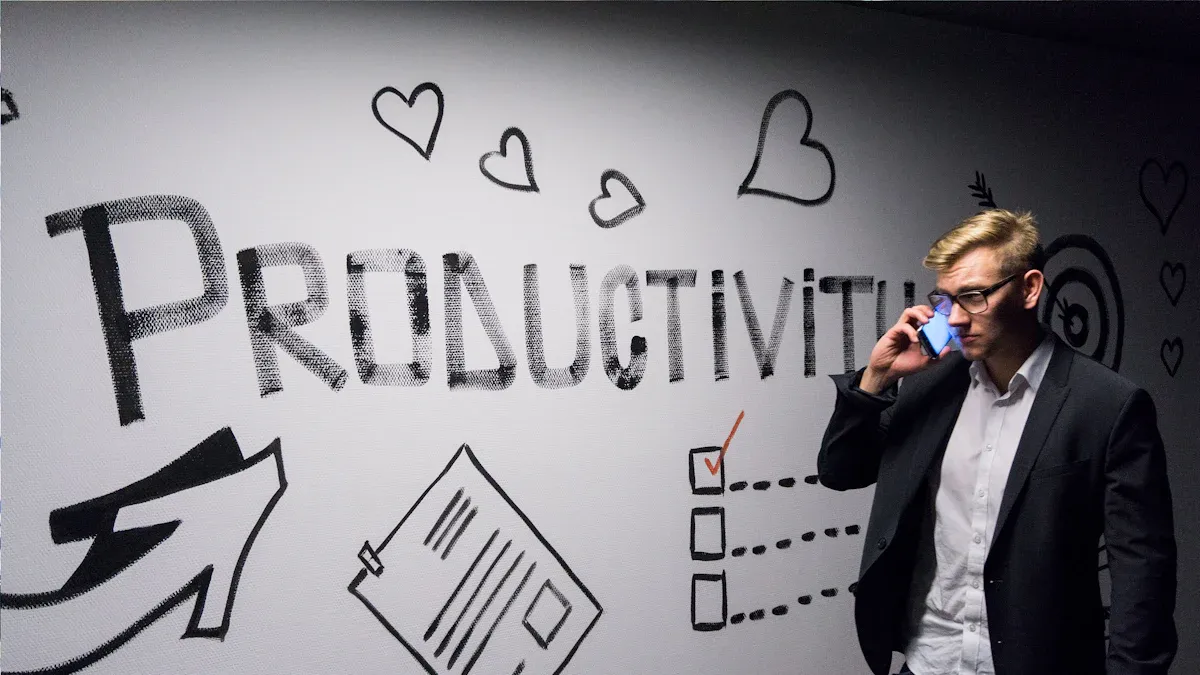
Lean Manufacturing
Principles of Lean
Lean Manufacturing focuses on maximizing customer value by eliminating waste within processes. It operates on five core principles: identifying value, mapping the value stream, creating flow, establishing pull, and pursuing perfection. These principles aim to streamline operations, ensuring every step adds value to the final product or service.
Benefits of Lean Manufacturing
Organizations adopting Lean Manufacturing often experience significant improvements. For example:
Automotive Manufacturing: Companies have enhanced part consistency and quality while reducing variability, leading to higher customer satisfaction.
Electronics Production: Manufacturers have improved production yields and minimized downtime by monitoring production lines effectively.
Medical Device Production: Standardized processes have ensured safety and quality, boosting customer trust.
These benefits demonstrate how Lean Manufacturing can transform industries by reducing costs and improving efficiency.
How to Apply Lean in Your Organization
To implement Lean, organizations should start by analyzing their workflows to identify waste. Teams can use tools like value stream mapping to visualize processes and pinpoint inefficiencies. Encouraging employee involvement is crucial, as their insights often reveal hidden bottlenecks. Regularly reviewing and refining processes ensures continuous improvement and alignment with Lean principles.
Six Sigma
Overview of Six Sigma
Six Sigma is a data-driven methodology for process improvement that aims to reduce defects and variability. It uses the DMAIC framework (Define, Measure, Analyze, Improve, Control) to identify and eliminate inefficiencies. This approach ensures processes meet high-quality standards and align with customer expectations.
Benefits of Six Sigma
Organizations implementing Six Sigma often achieve measurable results:
General Electric: Enhanced product quality and services, leading to increased revenue.
Boeing Airlines: Resolved manufacturing issues by identifying root causes.
Microsoft: Developed successful products like Windows CE by analyzing customer demand.
These examples highlight Six Sigma's ability to drive operational excellence and customer satisfaction.
Steps to Implement Six Sigma
To adopt Six Sigma, organizations should follow these steps:
Define: Identify the problem and set clear objectives.
Measure: Collect data to understand current performance.
Analyze: Determine the root causes of inefficiencies.
Improve: Develop and implement solutions.
Control: Monitor changes to ensure sustained improvements.
Training employees in Six Sigma tools and techniques is essential for successful implementation.
Kaizen (Continuous Improvement)
Philosophy of Kaizen
Kaizen, a Japanese term meaning "change for the better," emphasizes continuous improvement involving everyone in the organization. This methodology for process improvement encourages small, incremental changes that collectively lead to significant advancements over time.
Benefits of Incremental Improvements
Kaizen fosters a culture of ownership and collaboration, leading to sustainable change. Employees feel empowered to contribute ideas, enhancing engagement and morale. Over time, these small improvements result in streamlined processes, reduced waste, and improved customer satisfaction.
Tips for Fostering a Kaizen Culture
To cultivate a Kaizen culture, organizations should:
Encourage open communication and idea-sharing among employees.
Recognize and reward contributions to improvement efforts.
Provide training on Kaizen principles and tools.
Leaders play a vital role in setting the tone for continuous improvement by modeling the behavior they wish to see in their teams.
Plan-Do-Check-Act (PDCA)
Explanation of the PDCA Cycle
The Plan-Do-Check-Act (PDCA) cycle is a four-step iterative process designed to improve workflows and solve problems systematically. It begins with the Plan phase, where teams identify issues, set objectives, and develop strategies. In the Do phase, they implement the plan on a small scale to test its effectiveness. The Check phase involves analyzing results and comparing them to the desired outcomes. Finally, the Act phase focuses on standardizing successful changes or revisiting the cycle to address unresolved issues.
This methodology for process improvement emphasizes continuous learning and adaptation. By repeating the cycle, organizations can refine their processes and respond effectively to changing needs.
Benefits of PDCA
The PDCA cycle offers several measurable benefits:
Encourages continuous improvement by fostering a culture of learning and experimentation.
Promotes data-driven decision-making through systematic data collection and analysis.
Enhances customer satisfaction by prioritizing feedback during the Check phase.
Improves efficiency and productivity by identifying and addressing inefficiencies early.
Reduces risks in product launches through frequent course corrections.
These advantages make PDCA a versatile tool for organizations seeking sustainable growth and adaptability.
Practical Application of PDCA
Organizations can apply the PDCA cycle in various scenarios, such as improving production processes, enhancing customer service, or developing new products. For example, a manufacturing team might use the cycle to reduce defects in a production line. During the Plan phase, they identify the root cause of defects and propose solutions. In the Do phase, they test these solutions on a small batch. The Check phase evaluates the results, and the Act phase implements successful changes across the entire production line.
To maximize the effectiveness of PDCA, teams should document each phase, involve key stakeholders, and remain open to iterative improvements.
Business Process Reengineering (BPR)
What Is BPR?
Business Process Reengineering (BPR) involves the radical redesign of workflows to achieve significant improvements in performance metrics such as cost, quality, and speed. Unlike incremental approaches, BPR focuses on rethinking and restructuring processes from the ground up. This methodology for process improvement often leverages technology to streamline operations and eliminate redundancies.
Benefits of Radical Process Redesign
BPR delivers transformative results for organizations:
Cycle time improvements ranging from 50% to 75%.
Enhanced customer satisfaction through faster and more efficient service delivery.
Case studies highlight its impact. IBM reduced lead times from 40 days to 4 days, saving $1 billion annually. Ford Motor Company cut order-to-delivery time by 75%, boosting profitability and customer trust.
How to Approach BPR Effectively
To implement BPR successfully, organizations should:
Identify processes that require redesign, focusing on those with the highest impact.
Assemble cross-functional teams to analyze current workflows and propose innovative solutions.
Leverage technology to automate and optimize processes.
Monitor progress using key performance indicators (KPIs) to ensure desired outcomes.
Effective communication and change management are crucial for overcoming resistance and ensuring stakeholder buy-in.
Total Quality Management (TQM)
Overview of TQM
Total Quality Management (TQM) is a holistic approach to improving organizational performance by focusing on quality at every level. It emphasizes customer satisfaction, employee involvement, and continuous improvement. TQM integrates quality management principles into daily operations, ensuring that every team member contributes to achieving organizational goals.
Benefits of TQM
Organizations adopting TQM often experience:
Improved product and service quality, leading to higher customer satisfaction.
Enhanced employee morale through active participation in quality initiatives.
Reduced costs by minimizing defects and waste.
Increased competitiveness in the market.
These benefits make TQM a valuable strategy for organizations aiming to achieve long-term success.
Steps to Implement TQM
To implement TQM effectively, organizations should:
Establish a clear vision and communicate it across all levels.
Provide training on quality management principles and tools.
Encourage employee involvement by creating opportunities for collaboration and feedback.
Monitor progress using metrics such as defect rates and customer satisfaction scores.
Continuously refine processes based on data and feedback.
Leadership plays a critical role in fostering a culture of quality and ensuring the successful adoption of TQM principles.
5 Whys Analysis
What Is the 5 Whys Technique?
The 5 Whys technique is a simple yet powerful tool for identifying the root cause of a problem. Developed by Sakichi Toyoda, this method involves asking "Why?" five times or more until the underlying issue becomes clear. Each "Why" builds on the previous answer, creating a chain of reasoning that leads to the core problem.
This technique works well in various industries, including manufacturing, healthcare, and IT. Teams use it to address recurring issues, improve processes, and enhance overall efficiency. By focusing on the root cause rather than symptoms, the 5 Whys method helps organizations implement solutions that prevent problems from reoccurring.
Benefits of Root Cause Analysis
The 5 Whys technique offers several advantages for organizations aiming to improve their processes:
Encourages deeper thinking to uncover root causes.
Leads to more effective and lasting solutions.
Helps prevent future occurrences of problems.
Improves processes and reduces errors across operations.
The 5 Whys fit perfectly into a continuous improvement approach. By encouraging systematic identification of the underlying causes of problems, this methodology fosters a culture of questioning and constant search for more effective solutions.
Organizations that adopt this method often experience measurable outcomes. For example, teams can reduce operational errors, streamline workflows, and enhance decision-making. These benefits make the 5 Whys a valuable tool for fostering long-term success.
How to Use the 5 Whys Method
Teams can follow these steps to apply the 5 Whys technique effectively:
Define the Problem: Clearly state the issue that needs resolution. For instance, "Why did the production line stop?"
Ask the First Why: Identify the immediate cause of the problem. Example: "The machine stopped because it overheated."
Continue Asking Why: Repeat the question to dig deeper into the root cause. Each answer should lead to the next "Why."
Reach the Root Cause: Stop when the team identifies the fundamental issue. This may take fewer or more than five iterations.
Implement Solutions: Develop and execute a plan to address the root cause. Monitor the results to ensure the problem does not recur.
For best results, teams should involve key stakeholders and document each step. This ensures transparency and accountability throughout the process. By using the 5 Whys method, organizations can tackle challenges systematically and create a foundation for continuous improvement.
Choosing the Right Methodology for Process Improvement
Assessing Your Organization’s Needs
Selecting the right process improvement methodology begins with understanding the unique needs of the organization. Each organization operates within a specific context, influenced by its goals, culture, and operational challenges. A methodology that aligns with these factors can enhance efficiency and customer satisfaction. Conversely, a poor choice may lead to wasted resources and minimal progress.
Organizations should evaluate their current performance using key metrics. These metrics provide a clear picture of operational strengths and weaknesses. For example:
Metric Type | Metric Name | Description |
---|---|---|
Operational performance indicators | Cycle time | Total time required to complete a task or process from start to finish. |
Yield rate | Quantity of compliant parts generated compared to raw material or resources used. | |
Quality indicators | Defect rate | Percentage of non-conforming or defective parts compared to the standard out of the total manufactured. |
Equipment efficiency | Overall Equipment Effectiveness (OEE) | Measures machine performance based on availability, performance, and quality. |
Financial indicators | Return On Investment (ROI) | Benefits obtained from improvement projects compared to the costs incurred. |
By analyzing these metrics, teams can identify areas requiring improvement and select a methodology tailored to address those specific challenges.
Comparing Methodologies Based on Scope and Complexity
Different methodologies vary in scope, focus, and complexity. Understanding these differences helps organizations choose the most suitable approach. For instance:
Methodology | Scope | Focus | Application |
---|---|---|---|
Six Sigma | Project-based | Reducing defects and improving quality | Manufacturing and business processes |
Lean | Project-based | Eliminating waste | Manufacturing and other sectors |
Kaizen | Ongoing | Continuous improvement | All organizational levels |
TQM | Organization-wide | Customer satisfaction | All processes and services |
BPM | Ongoing | Comprehensive management | All organizational processes |
For organizations seeking precision and defect reduction, Six Sigma offers a structured, data-driven approach. Lean focuses on waste elimination, making it ideal for streamlining processes. Kaizen fosters a culture of continuous improvement, while TQM integrates quality management across all levels. Business Process Management (BPM) provides a holistic framework for managing and optimizing processes.
Tip: Organizations should consider the complexity of their operations and the resources available when selecting a methodology. A simpler approach like Kaizen may suit smaller teams, while larger organizations might benefit from the comprehensive nature of TQM or BPM.
Aligning Methods with Team Resources and Goals
Aligning the chosen methodology with team resources and organizational goals ensures successful implementation. Teams must assess their capacity, expertise, and available tools. For example, Lean and Six Sigma require specific training and tools like value stream mapping or statistical analysis. Providing adequate training empowers employees to contribute effectively.
The Results Washington initiative demonstrates the importance of aligning resources with goals. This program empowered state employees to identify and solve problems using Lean principles. The initiative achieved significant savings and efficiency improvements by combining top-down leadership with bottom-up engagement.
Organizations can also use tools like value stream mapping to visualize workflows and identify inefficiencies. This approach ensures that team efforts align with broader organizational objectives, creating a cohesive strategy for process improvement.
Aligning methods with resources and goals not only enhances efficiency but also fosters a sense of ownership among team members, driving long-term success.
Overcoming Challenges in Process Improvement
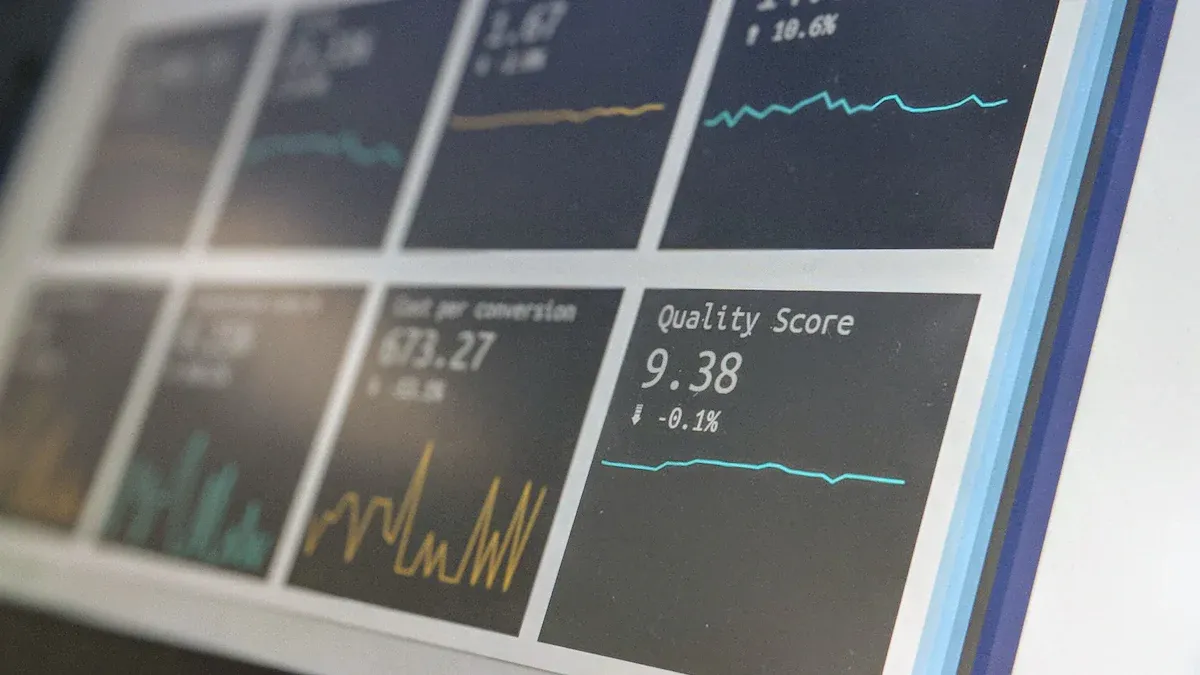
Addressing Resistance to Change
Resistance to change is one of the most common obstacles in process improvement. Employees often feel uncertain or fearful about new processes, which can hinder progress. The Change Curve model highlights this challenge by illustrating the emotional stages individuals experience during change. Resistance tends to peak early due to fear of the unknown or misunderstanding the need for change.
Organizations can mitigate resistance by adopting proven strategies:
Effective communication: Clearly explain the reasons for change and its benefits. This builds trust and reduces uncertainty.
Employee involvement: Encourage participation in the change process. A 2011 study found that involvement fosters acceptance and readiness for change.
Training and support: Equip employees with the skills needed to adapt to new processes.
Tip: Involving employees early in the process not only reduces resistance but also fosters a sense of ownership and commitment.
Statistics reveal that 60-70% of change initiatives fail, often due to poor communication and lack of planning. Organizations that prioritize thoughtful planning and employee engagement significantly improve their chances of success.
Setting Clear Goals and Metrics
Clear goals and metrics are essential for tracking the success of process improvement initiatives. Without them, teams may struggle to measure progress or identify areas needing adjustment. Key performance indicators (KPIs) provide a structured way to monitor improvements and ensure alignment with organizational objectives.
Description | Example | |
---|---|---|
Cycle time | Total time required to complete a task or process from start to finish. | A car manufacturing plant takes 8 hours to assemble each vehicle. |
Yield rate | Quantity of compliant parts generated compared to raw material used. | A factory produces 950 compliant items out of 1,000 parts, achieving a 95% yield rate. |
On Time Delivery (OTD) | Percentage of orders delivered on time. | A company delivers 180 out of 200 orders on time, achieving a 90% OTD rate. |
Defect rate | Percentage of non-conforming parts compared to total manufactured. | A production line produces 10,000 units, with 200 defective, resulting in a 2% defect rate. |
Overall Equipment Effectiveness (OEE) | Measures machine performance based on availability, performance, and quality. | A machine operates at 80% availability, 90% performance, and 95% quality, achieving 68.4% OEE. |
Note: Aligning KPIs with strategic objectives ensures that teams focus on what matters most. Using SMART criteria (Specific, Measurable, Achievable, Relevant, Time-bound) further enhances the effectiveness of goal-setting.
Organizations should also involve stakeholders in the KPI-setting process. This ensures clarity and buy-in, creating a shared vision for success.
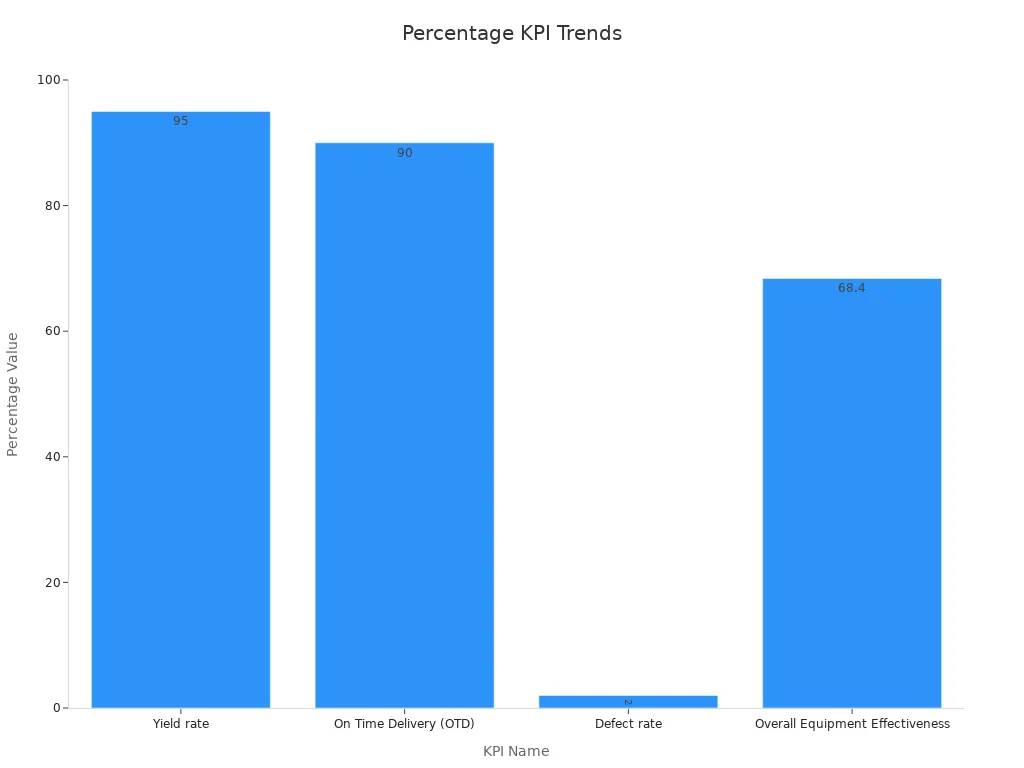
Tackling Implementation Barriers
Implementation barriers can derail even the most well-planned process improvement initiatives. Common obstacles include misconceptions about tools, lack of management support, and excessive tampering with processes. Addressing these challenges requires a proactive approach.
Key solutions include:
Educating employees: Teach teams that tools like Statistical Process Control (SPC) can apply to any process, emphasizing the importance of data collection.
Clarifying limitations: Train employees on the boundaries of tools like SPC and the need for complementary methods.
Providing resources: Ensure management offers adequate training and resources to support improvement efforts.
Obstacle Example: Misunderstanding control limits versus specification limits often leads to data misuse. Training employees on these distinctions prevents errors and enhances decision-making.
Leadership plays a critical role in overcoming barriers. By fostering a supportive environment and addressing misconceptions, organizations can create a foundation for successful implementation.
Sustaining Long-Term Process Improvement
Building a Culture of Continuous Improvement
A culture of continuous improvement ensures that organizations remain adaptable and competitive. This culture thrives on employee involvement, open communication, and a commitment to ongoing learning. Teams that embrace this mindset focus on small, incremental changes that lead to significant long-term benefits.
To build this culture, organizations can adopt several best practices:
Implement Kaizen Events to encourage focused workshops for process improvements.
Establish Employee Suggestion Programs to gather and implement innovative ideas.
Conduct Gemba Walks to observe challenges directly from frontline workers.
Form Quality Circles where small groups regularly address work-related problems.
Utilize Performance Metrics and Data Analysis to identify trends and areas for improvement.
Leaders play a crucial role in fostering this environment. By clearly communicating organizational values and goals, they align teams with the vision for continuous improvement. Regular monitoring and sharing of successes further reinforce this culture, motivating employees to stay engaged.
A culture of continuous improvement emphasizes data-driven decision-making and proactive problem-solving. These elements are essential for sustaining improvements and maintaining competitive advantages.
Monitoring and Measuring Progress
Monitoring progress ensures that process improvement initiatives achieve their intended outcomes. Organizations must define clear metrics and establish systems to track performance. Key performance indicators (KPIs) such as cycle time, defect rate, and customer satisfaction provide quantifiable insights into progress.
Steps to effectively monitor and measure progress include:
Define Metrics: Identify KPIs that align with business objectives.
Data Collection: Implement systems for real-time performance data analysis.
Reporting: Establish regular reporting mechanisms to evaluate process performance.
Organizations that view business processes as assets invest in performance monitoring tools like Statistical Process Control (SPC). These tools enhance efficiency by identifying trends and addressing inefficiencies promptly. Regular reviews of metrics also help teams make data-driven decisions, ensuring continuous improvement.
Measuring change validates whether initiatives meet objectives. It provides transparency, accountability, and facilitates ongoing refinement of processes.
Adapting to Changing Needs and Feedback
Adapting to evolving needs and feedback is critical for sustaining long-term improvements. Market conditions, customer expectations, and technological advancements often require organizations to revisit and refine their processes. Flexibility and responsiveness ensure that improvements remain relevant and effective.
Statistical trends highlight the impact of adaptive strategies:
Metric | |
---|---|
Operational Efficiency | 20 |
Production Defects Reduction | 40 |
Operational Costs Decrease | 30 |
Customer Satisfaction Increase | 25 |
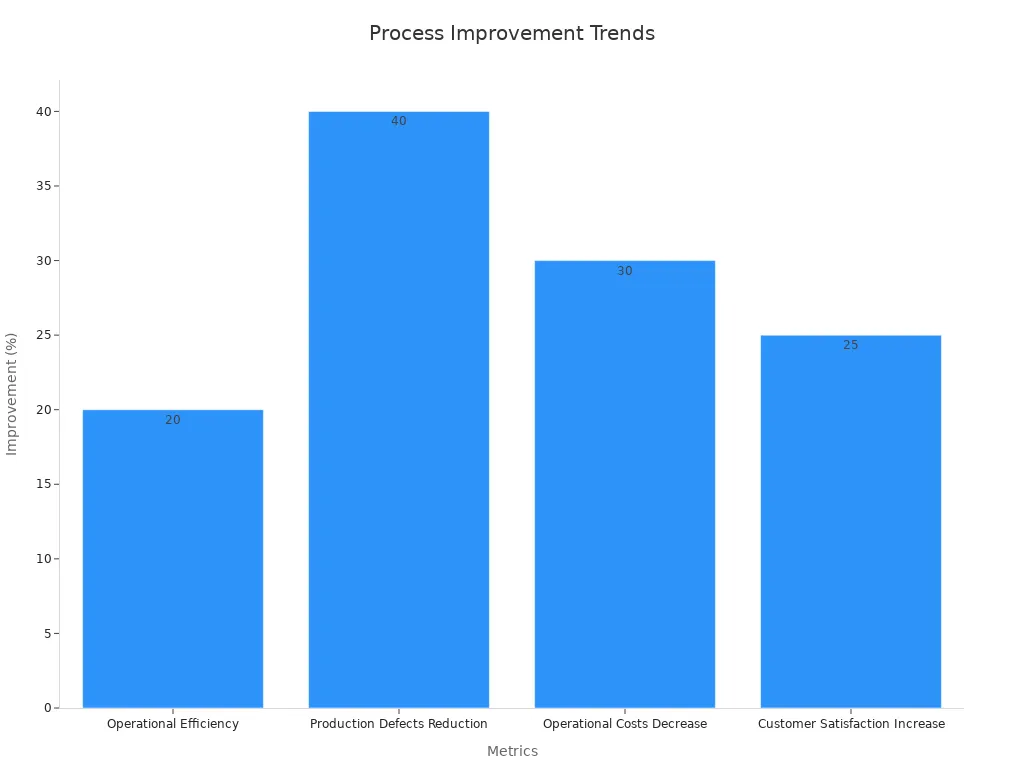
Organizations can adopt agile methodologies to remain flexible and responsive. Frequent feedback loops, combined with regular evaluations, allow teams to identify areas for adjustment. By incorporating stakeholder input and leveraging data, businesses can refine their strategies to meet changing demands.
Continuous adaptation ensures that process improvements align with organizational goals and external factors. This approach fosters resilience and long-term success.
Process improvement remains a cornerstone of organizational success. The methodologies discussed—Lean, Six Sigma, Kaizen, and others—offer practical tools for enhancing efficiency, reducing costs, and boosting customer satisfaction. Consistent application of these methods delivers measurable results. For example:
The Results Washington initiative achieved 50% of its nearly 200 goals, meeting or exceeding targets.
Lean programs returned $4.5 in value for every $1 invested, saving $33 million and improving customer satisfaction.
Operational improvements included a 15% reduction in speed-related deaths and 20% faster DNA test processing.
Starting with one method allows teams to build momentum. Over time, small, steady efforts lead to transformative outcomes. Organizations that prioritize process improvement position themselves for long-term growth and adaptability.
FAQ
What is the best methodology for process improvement?
The best methodology depends on the organization’s goals and resources. Lean works well for waste reduction, while Six Sigma focuses on quality. Kaizen fosters continuous improvement. Teams should assess their needs and choose a method that aligns with their objectives.
How long does it take to see results from process improvement?
Results vary based on the methodology and scope. Small changes, like those in Kaizen, may show results within weeks. Larger initiatives, such as Business Process Reengineering, can take months. Consistent effort ensures long-term success.
Can small teams implement process improvement methodologies?
Yes, small teams can adopt methodologies like Kaizen or PDCA. These approaches require fewer resources and encourage collaboration. Training and clear goals help small teams achieve measurable improvements without overwhelming their capacity.
How do you measure the success of process improvement?
Success is measured using key performance indicators (KPIs) like cycle time, defect rate, and customer satisfaction. Teams should track these metrics regularly to evaluate progress and ensure alignment with organizational goals.
What role does leadership play in process improvement?
Leadership drives process improvement by setting clear goals, providing resources, and fostering a culture of collaboration. Leaders must communicate the benefits of change and support teams throughout the implementation process.
Is training necessary for process improvement?
Training is essential for methodologies like Six Sigma and Lean. It equips teams with the tools and knowledge needed for effective implementation. Organizations should invest in training to maximize the impact of their improvement efforts.
How can resistance to change be minimized?
Resistance can be reduced through clear communication, employee involvement, and training. Teams should understand the benefits of change and feel supported throughout the process. Leadership plays a key role in addressing concerns and building trust.
Where can I learn more about process improvement?
Readers can explore additional resources or reach out to our team for guidance. Our experts provide tailored advice to help systems and teams implement effective process improvement strategies. Contact us today to get started.