Top Benefits of Lean Six Sigma Process Mapping Explained
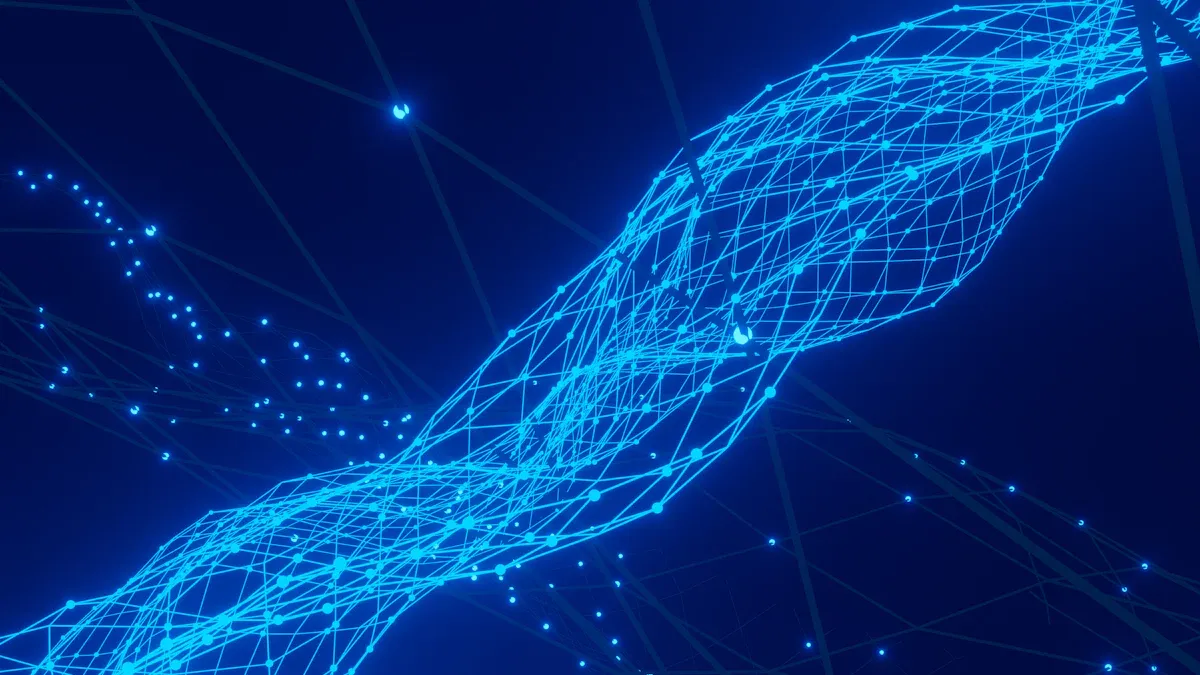
Lean Six Sigma Process Mapping empowers organizations to streamline workflows and achieve measurable results for their clients and customers. By visualizing processes, businesses can identify inefficiencies and implement targeted optimization steps. For example, a manufacturing plant increased production efficiency by 20%, while a healthcare provider reduced patient wait times by 35%. Metrics like defect rate and cycle time highlight areas for improvement, ensuring processes align with customer expectations. Clients benefit from enhanced quality and faster service delivery, fostering satisfaction and loyalty. This transformative tool drives operational excellence and continuous improvement across industries.
Key Takeaways
Lean Six Sigma Process Mapping shows how work gets done clearly.
It helps find and remove wasteful steps to save time and money.
Tools like flowcharts and maps make processes easy to understand.
Checking process maps often helps businesses stay efficient as needs change.
Including everyone in mapping builds trust and meets group goals.
Using data from maps helps businesses make smart decisions.
A culture of improvement inspires workers to fix problems quickly.
Real-life examples prove this method boosts work and keeps customers happy.
Understanding Lean Six Sigma Process Mapping
What Is Lean Six Sigma Process Mapping?
Lean Six Sigma Process Mapping is a structured approach to visualizing and analyzing workflows within an organization. It provides a clear representation of how tasks, decisions, and resources interact to deliver a product or service. By breaking down processes into individual steps, it becomes easier to identify inefficiencies and areas for improvement.
Organizations use various types of process maps to suit their needs. For example:
Flow Chart / Block Diagram: Offers a high-level overview of processes, which can be expanded with more detail over time.
Cross-Functional Map / Swim Lane: Organizes processes into lanes based on functions, highlighting handoffs and responsibilities.
Cross Resource Map: Focuses on resource interactions, providing a deeper understanding of functional dependencies.
These tools help businesses visualize their operations and set the foundation for optimization.
Purpose and Importance in Business Operations
The primary purpose of Lean Six Sigma Process Mapping is to enhance operational efficiency and quality. It allows organizations to visualize both the current and ideal states of their processes. This visualization helps identify root causes of inefficiencies and plan targeted improvements.
Case studies from various industries highlight its importance:
Small businesses have reported increased productivity and customer satisfaction after implementing Lean Six Sigma methodologies.
Manufacturing companies have achieved significant gains in quality and profitability by using process mapping to streamline operations.
Logistics services have successfully applied Lean Six Sigma to payment and request-to-ship processes, improving efficiency and reducing delays.
By focusing on continuous improvement and strategic analysis, process mapping becomes a critical tool for achieving operational excellence.
Key Principles of Process Mapping in Lean Six Sigma
Lean Six Sigma Process Mapping is guided by several key principles:
Focus on Value: Every step in the process should add value from the customer's perspective. Non-value-added activities must be identified and eliminated.
Data-Driven Analysis: Decisions should rely on data collected during the mapping process. Tools like SIPOC (Suppliers, Inputs, Process, Outputs, Customers) and Value Stream Mapping (VSM) support this analysis.
Continuous Improvement: Process mapping is not a one-time activity. It should be revisited regularly to adapt to changing business needs and ensure ongoing optimization.
These principles ensure that organizations can systematically improve their workflows and achieve sustainable growth.
Visualizing Processes for Clarity and Transparency
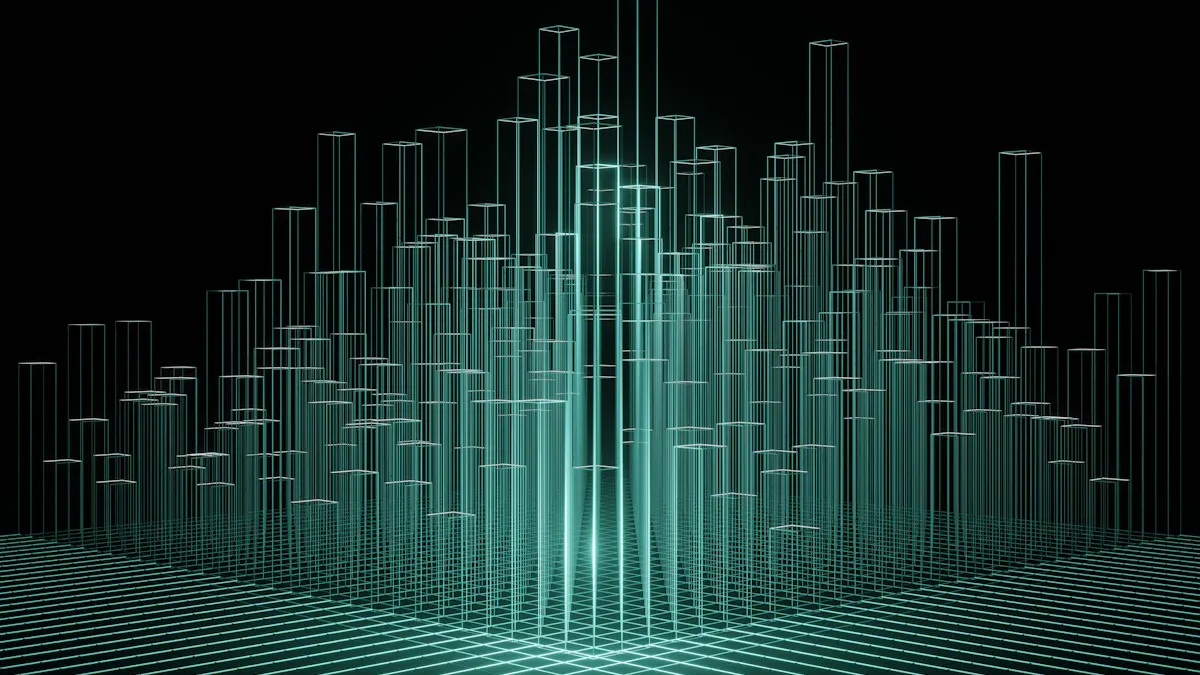
How Process Mapping Creates a Clear Workflow Picture
Lean Six Sigma Process Mapping provides a structured way to visualize workflows, making complex processes easier to understand. By breaking down tasks into clear steps, organizations can identify inefficiencies and improve operations. Various diagrammatic techniques enhance this clarity:
Description | Real-World Example | |
---|---|---|
Swimlane Diagrams | Outlines workflows by separating responsibilities across different lanes. | Employee training program management workflow. |
SIPOC Diagrams | Provides a high-level overview of a process, focusing on Suppliers, Inputs, Process, Outputs, and Customers. | Customer support process summary. |
Value Stream Maps | Visualizes the flow of materials and information, highlighting value-added vs. non-value-added activities. | Manufacturing process for phones, showing non-value-added activities. |
Process Flow Diagrams | Represents the steps in a process, including inputs and outputs. | Car sales process, detailing customer qualification and decision points. |
BPMN Diagrams | Offers a detailed view of processes using standardized symbols for events, activities, and gateways. | Online shopping process, illustrating user interactions and decisions. |
These tools help teams visualize workflows, ensuring everyone understands the process and their role within it.
Identifying Gaps, Bottlenecks, and Redundancies
Process mapping enables organizations to pinpoint inefficiencies that hinder performance. For example, Value Stream Mapping highlights areas where value is lost, such as unnecessary delays or redundant steps. Pareto Charts further aid in prioritizing issues by identifying the most significant factors affecting a process.
Description | |
---|---|
Kanban | A system to visualize tasks and manage workflow, ensuring transparency and real-time updates. |
Pareto Chart | A statistical tool that identifies and prioritizes significant factors affecting a process. |
Process Mapping | A strategic tool that visualizes the flow of a business process, detailing activities and roles. |
By using these methodologies, organizations can address bottlenecks and streamline operations, ultimately improving efficiency and reducing costs.
Enhancing Teamwide Transparency and Understanding
Clear process maps foster transparency by providing a shared understanding of workflows. Flowcharts, for instance, use symbols to represent stages, decision points, and endpoints, making processes easier to follow. Their sequential nature also helps teams identify risks and inefficiencies.
Completed process maps serve as standard definitions for workflows, which can be refined over time. This promotes ongoing transparency and understanding among teams.
Value Stream Mapping reveals how value flows through the organization, emphasizing a holistic approach to avoid sub-system optimization.
Teams gain a clearer picture of their roles and responsibilities, aligning efforts toward common goals.
By enhancing transparency, Lean Six Sigma Process Mapping ensures that all stakeholders remain informed and engaged in the improvement process.
Identifying and Eliminating Inefficiencies
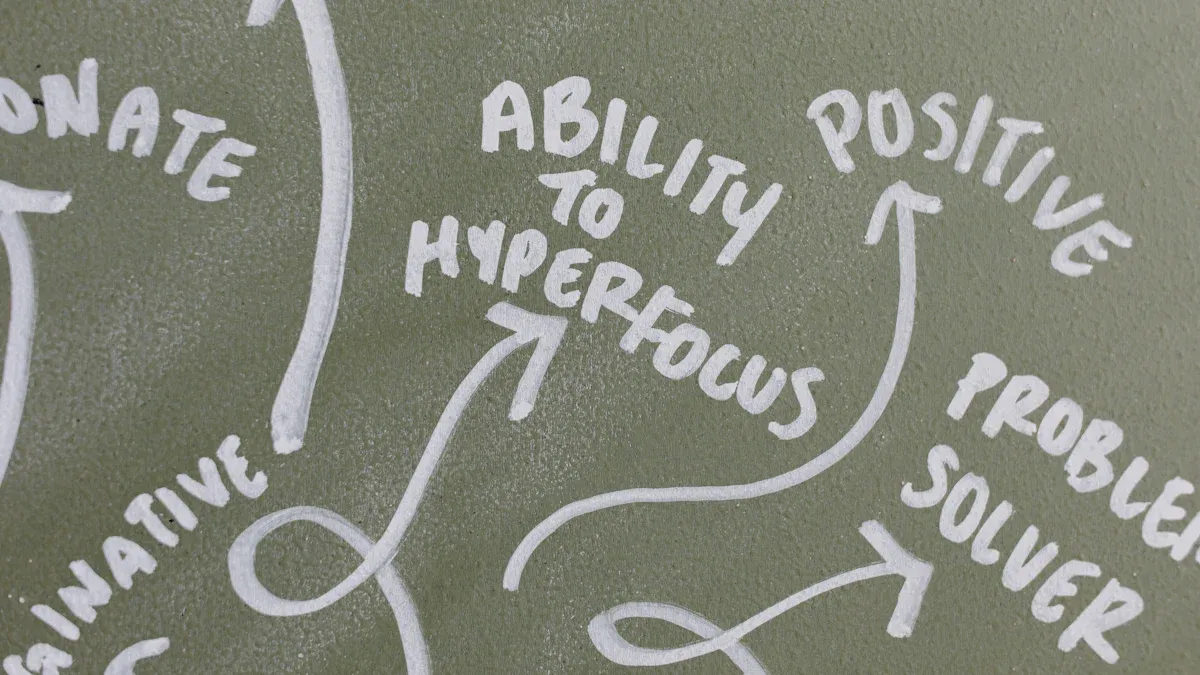
Recognizing Non-Value-Added Activities
Lean Six Sigma Process Mapping helps organizations identify activities that do not add value to their processes. These non-value-added activities often consume resources without contributing to the final product or service. By eliminating them, businesses can improve efficiency and reduce costs.
A variety of non-value-added activities can be identified through process mapping. The table below highlights common examples:
Activity Type | Description |
---|---|
Explicit Bottleneck | Causes wait queues and delays, leading to idle time in subsequent activities. Example: Nurses unable to prepare patients for surgery, causing delays. |
Hidden Bottleneck | Causes idle time before and after the bottleneck. Example: Patient intake adjusted to match nursing workload, still resulting in bottlenecks. |
Non-Value-Add | Produces outputs that add no value. Example: Transportation of outputs between distant activities that could be co-located. |
Rework | Executed to resolve quality issues. Example: Incomplete Summary of Care documents requiring follow-up requests. |
By addressing these inefficiencies, organizations can streamline workflows and focus on value-added activities that directly benefit customers.
Reducing Delays and Cycle Times
Delays and long cycle times often hinder operational performance. Lean Six Sigma Process Mapping provides tools to analyze and minimize these inefficiencies. For instance, diagrams and control charts help visualize delays, while statistical tools like standard deviations measure process variability.
Statistical Tool | Purpose in Lean Six Sigma |
---|---|
Diagrams | Visual representation of processes to identify delays |
Control Charts | Monitoring process performance over time |
Standard Deviations | Measuring variability and consistency in processes |
Organizations across industries have successfully reduced delays using these methods. For example, a logistics company used process mapping to optimize its shipping process, cutting delivery times by 25%. These improvements not only enhance customer satisfaction but also reduce operational costs.
Optimizing Resource Allocation and Utilization
Efficient resource allocation is critical for achieving operational excellence. Lean Six Sigma Process Mapping enables organizations to analyze how resources are utilized and identify areas for improvement. By reallocating resources effectively, businesses can maximize productivity and minimize waste.
The table below illustrates how different industries have optimized resource allocation through process mapping:
Industry | Application Description | Outcome |
---|---|---|
Manufacturing | Redesigning the manufacturing process for adhesive tapes using DMEDI. | Developed a highly efficient and cost-effective production system that exceeded expectations. |
Services | Enhancing customer experiences and streamlining transactional processes. | Improved customer wait times and first-call resolution rates, leading to cost savings. |
Healthcare | Redesigning the clinical trial process for a new drug candidate. | Optimized patient recruitment and accelerated drug development while ensuring quality. |
These examples demonstrate how process mapping can lead to significant efficiency gains by ensuring resources are allocated where they are most needed.
Fostering Collaboration and Communication
Aligning Teams Toward Common Goals
Lean Six Sigma Process Mapping plays a pivotal role in aligning teams toward shared objectives. By providing a clear visualization of workflows, it ensures that every team member understands their responsibilities and how their tasks contribute to the organization's goals. This alignment fosters a sense of purpose and unity across departments.
Studies highlight the impact of alignment on organizational success. For instance, Ströer, a German company, implemented the OKR (Objectives and Key Results) framework to enhance collaboration among over 10,000 employees. This initiative improved transparency and teamwork. Similarly, Brimstone Pharmacy managed a 70% workload increase post-acquisition by conducting alignment workshops, which boosted profits by over $7 million. These examples demonstrate how aligning teams through structured methodologies like process mapping can drive remarkable results.
Aligned organizations also experience tangible benefits. A global benchmark report revealed that companies with aligned teams lost 36% fewer customers. Another study found that aligning sales and marketing teams led to a 30% higher return rate. These findings underscore the importance of fostering alignment to achieve operational excellence.
Encouraging Cross-Functional Collaboration
Cross-functional collaboration thrives when teams from different departments work together effectively. Lean Six Sigma Process Mapping facilitates this by creating a shared understanding of workflows and dependencies. It encourages open communication and ensures that all stakeholders contribute their expertise to improve processes.
Collaboration models emphasize the value of diverse perspectives. For example, the 3P (Production Preparation Process) methodology integrates insights from process operators, industrial engineers, quality assurance experts, and other key roles. This approach leads to innovative solutions that minimize waste and enhance customer satisfaction. The table below highlights the roles involved in cross-departmental teamwork:
Role | Description |
---|---|
Process Operators | Hands-on experience with the process |
Industrial Engineers | Expertise in process excellence |
Quality Assurance Experts | Focus on maintaining quality standards |
Maintenance Technicians | Knowledge of equipment and maintenance needs |
Logistics Personnel | Understanding of material handling |
Customer Service Representatives | Voice of the customer perspective |
Suppliers | Insight into external impacts on the process |
Real-world examples further validate the value of cross-functional collaboration. A leading financial institution established a centralized RPA (Robotic Process Automation) team that worked closely with business users and IT teams. This collaboration automated over 100 processes, resulting in significant cost savings and improved efficiency. Such initiatives highlight how process mapping fosters teamwork and drives impactful outcomes.
Engaging Stakeholders in the Improvement Process
Engaging stakeholders is crucial for the success of any improvement initiative. Lean Six Sigma Process Mapping ensures that stakeholders remain actively involved by providing a transparent view of processes and encouraging their input. This engagement not only enhances the relevance of improvement efforts but also builds trust and accountability.
Effective stakeholder engagement requires structured interactions and trust-building activities. Face-to-face meetings, for example, allow stakeholders to share their perspectives and provide valuable feedback. Incorporating diverse viewpoints ensures that improvement initiatives address the needs of all parties involved. However, this process may require adjustments to timelines to accommodate stakeholder input.
Organizations that prioritize stakeholder engagement often achieve better outcomes. For instance, ongoing collaboration between research producers and users has proven essential for meeting project objectives. By involving stakeholders throughout the process, businesses can ensure that their improvement efforts align with organizational goals and deliver meaningful results.
Enabling Data-Driven Decision-Making
Leveraging Insights from Process Mapping
Lean Six Sigma Process Mapping equips organizations with actionable insights by visualizing workflows and identifying inefficiencies. This data-driven approach enables businesses to uncover trends and make informed decisions. For example:
Trend analysis reveals shifts in customer behavior, helping organizations predict future actions based on historical data.
Behavioral insights provide a deeper understanding of customer decision-making processes, uncovering significant trends.
Predictive analytics leverages machine learning to forecast outcomes, enhancing strategic planning.
These insights empower organizations to optimize their processes, improve customer satisfaction, and stay ahead of market demands. By leveraging data from process mapping, businesses can transform raw information into valuable knowledge that drives success.
Supporting Strategic and Tactical Planning
Lean Six Sigma Process Mapping plays a critical role in both strategic and tactical planning. It provides a clear framework for setting goals, monitoring progress, and achieving desired outcomes. Key performance indicators (KPIs) and monitoring tools are essential components of this process. The table below highlights their importance:
Aspect | Description |
---|---|
KPIs | Define Key Performance Indicators to measure the progress and success of each task. |
Monitoring Tools | Use tools such as dashboards or project management software to track metrics. |
Organizations can also use process mapping to continuously monitor and measure the progress of tactical plans. This ensures that adjustments can be made as needed to achieve optimal results. Selecting the right KPIs is crucial, as they focus on the measures that have the most significant impact on organizational growth. By integrating these elements, businesses can align their strategies with operational goals and drive meaningful improvements.
Proactively Addressing Potential Issues
Proactive risk management is a cornerstone of Lean Six Sigma Process Mapping. This approach enables organizations to identify and mitigate risks before they escalate into significant problems. By assessing potential risks and developing contingency plans, businesses can act swiftly to prevent losses.
Continuous improvement in risk assessment further enhances this capability. Organizations refine their strategies based on historical data and past experiences, allowing them to recognize new risks more effectively. Tools such as predictive analytics and risk assessment matrices help visualize potential risks and their impacts. These tools enable teams to anticipate challenges and address them proactively.
By embedding risk management into process mapping, organizations can enhance their agility and resilience. This ensures that they remain prepared to tackle emerging issues, safeguarding their operations and maintaining efficiency.
Driving Continuous Improvement
Building a Culture of Ongoing Optimization
Organizations thrive when they foster a culture of continuous improvement. This culture encourages employees to identify inefficiencies and propose solutions. Leaders play a pivotal role by setting clear, measurable goals that align with organizational objectives. Regular performance reviews and feedback sessions reinforce positive behaviors and provide employees with actionable insights for growth.
A culture-based assessment can help employees pinpoint areas for improvement while highlighting their strengths. Leaders should also schedule follow-up meetings to track progress and ensure employees have the resources they need to succeed. These practices not only promote accountability but also create an environment where ongoing optimization becomes second nature.
To sustain this culture, organizations must integrate continuous feedback into their performance reviews. This approach emphasizes development over evaluation, motivating employees to embrace change and contribute to the organization's success.
Monitoring and Measuring Process Performance
Effective monitoring and measurement are essential for maintaining process efficiency. Lean Six Sigma Process Mapping provides a framework for tracking performance metrics and identifying areas for improvement. Organizations can leverage advanced tools to gain real-time insights into their workflows.
Tool Type | Description |
---|---|
Business Process Management | Comprehensive suites like Appian and IBM BPM provide dashboards and analytics for tracking metrics. |
Business Activity Monitoring | Tools like Software AG’s ARIS focus on real-time monitoring and visualizations of process KPIs. |
Process Mining Tools | Tools such as Celonis extract data to analyze and optimize process flows. |
IT Operations Monitoring | Solutions like Splunk monitor IT infrastructure impacting business processes. |
These tools enable organizations to visualize performance trends and make data-driven decisions. For example, process mining tools can uncover inefficiencies in workflows, while business activity monitoring ensures that key performance indicators (KPIs) remain aligned with organizational goals. By adopting these technologies, businesses can maintain transparency and drive continuous improvement.
Adapting to Evolving Business Needs
In a rapidly changing business environment, adaptability is crucial. Organizations must continuously refine their processes to meet evolving market demands and technological advancements. This involves analyzing current workflows, identifying inefficiencies, and implementing targeted improvements.
Automation plays a significant role in this adaptation. By automating repetitive tasks, businesses can eliminate bottlenecks and enhance efficiency. AI-powered tools further support this effort by providing actionable insights into potential optimizations. Continuous monitoring and feedback loops ensure that processes remain aligned with industry best practices.
To adapt effectively, organizations can follow a structured approach:
Analyze the current process to identify weaknesses.
Target specific tasks for automation to enhance efficiency.
Continuously monitor and improve the process after deployment.
By embracing these strategies, businesses can stay competitive and responsive to changing needs, ensuring long-term success.
Practical Applications of Lean Six Sigma Process Mapping
Real-World Examples in Manufacturing
Lean Six Sigma Process Mapping has proven to be a game-changer in manufacturing. It provides a detailed overview of workflows, enabling organizations to pinpoint inefficiencies and implement targeted improvements. This approach forms the backbone of continuous improvement strategies.
For instance:
FedEx revolutionized its aircraft maintenance C-check process during the 2008 recession. By identifying 68 critical milestones and segmenting them into 4-hour increments, the company streamlined workflows. This initiative increased annual C-checks from 14 to 30 and reduced man-hours from 32,715 to 21,535.
A leading automotive manufacturer used process mapping to optimize its assembly line. By identifying bottlenecks and reconfiguring workflows, the company reduced production time by 15% while maintaining quality standards.
These examples highlight how process mapping can enhance efficiency, reduce costs, and drive productivity in manufacturing environments.
Applications in Service and Non-Manufacturing Industries
The benefits of Lean Six Sigma Process Mapping extend beyond manufacturing. Service industries, including healthcare, logistics, and finance, have successfully adopted this methodology to improve operations.
In healthcare, process mapping has been instrumental in reducing patient wait times and improving care delivery. A hospital, for example, used this tool to analyze its patient intake process. By eliminating redundant steps, the hospital reduced average wait times by 30%.
In logistics, companies have optimized shipping processes to meet tight delivery schedules. One logistics provider used process mapping to identify delays in its supply chain. By addressing these issues, the company improved on-time delivery rates by 20%.
Financial institutions have also leveraged process mapping to streamline transactional workflows. A bank, for instance, used this approach to enhance its loan approval process. By automating repetitive tasks and reallocating resources, the bank reduced approval times by 40%.
These applications demonstrate the versatility of process mapping in addressing challenges across various industries.
Success Stories of Organizations Using Process Mapping
Organizations that adopt Lean Six Sigma Process Mapping often experience transformative results. This methodology fosters clarity, efficiency, and continuous improvement, leading to measurable success.
Key benefits include:
Improved performance through the elimination of inefficiencies.
Enhanced customer satisfaction by delivering better products and services.
Cost reduction through optimized resource allocation.
Increased transparency and accountability, promoting collaboration across teams.
For example, a global electronics company used process mapping to standardize its production processes. This initiative improved product quality and reduced defect rates by 25%. Similarly, a retail chain implemented process mapping to optimize its inventory management system. The result was a 15% reduction in stockouts and a 10% increase in sales.
These success stories underscore the potential of process mapping to drive growth and operational excellence.
Lean Six Sigma Process Mapping offers a structured framework for analyzing and improving workflows. It empowers organizations to enhance efficiency, reduce waste, and foster collaboration. By adopting this methodology, businesses can achieve sustainable growth and maintain a competitive edge. Organizations that embrace process mapping unlock its potential to drive meaningful change and operational excellence.
Start implementing Lean Six Sigma Process Mapping today to transform your processes and achieve measurable results.
FAQ
What is the primary goal of Lean Six Sigma Process Mapping?
The primary goal is to visualize workflows, identify inefficiencies, and optimize processes. This approach ensures that every step adds value, reduces waste, and aligns with organizational objectives.
How does Lean Six Sigma Process Mapping improve efficiency?
It identifies bottlenecks, redundancies, and non-value-added activities. By addressing these issues, organizations streamline workflows, reduce delays, and enhance resource utilization.
Can Lean Six Sigma Process Mapping be applied to small businesses?
Yes, small businesses can benefit significantly. It helps them improve productivity, reduce costs, and enhance customer satisfaction by optimizing their limited resources.
What tools are commonly used in Lean Six Sigma Process Mapping?
Common tools include SIPOC diagrams, Value Stream Mapping, and Swimlane diagrams. These tools provide clear visualizations of workflows and help identify areas for improvement.
How does process mapping foster collaboration?
It creates transparency by providing a shared understanding of workflows. Teams can align their efforts, communicate effectively, and work toward common goals.
Is Lean Six Sigma Process Mapping suitable for non-manufacturing industries?
Yes, it applies to various industries, including healthcare, finance, and logistics. It helps improve service delivery, streamline operations, and enhance customer experiences.
How often should organizations revisit their process maps?
Organizations should revisit process maps regularly, especially when introducing new technologies, scaling operations, or addressing performance issues. Continuous updates ensure processes remain efficient and relevant.
What are the key benefits of using Lean Six Sigma Process Mapping?
Key benefits include improved efficiency, reduced costs, enhanced customer satisfaction, and better collaboration. It also supports data-driven decision-making and fosters a culture of continuous improvement.