How to Enhance Efficiency with Process Improvement Methods
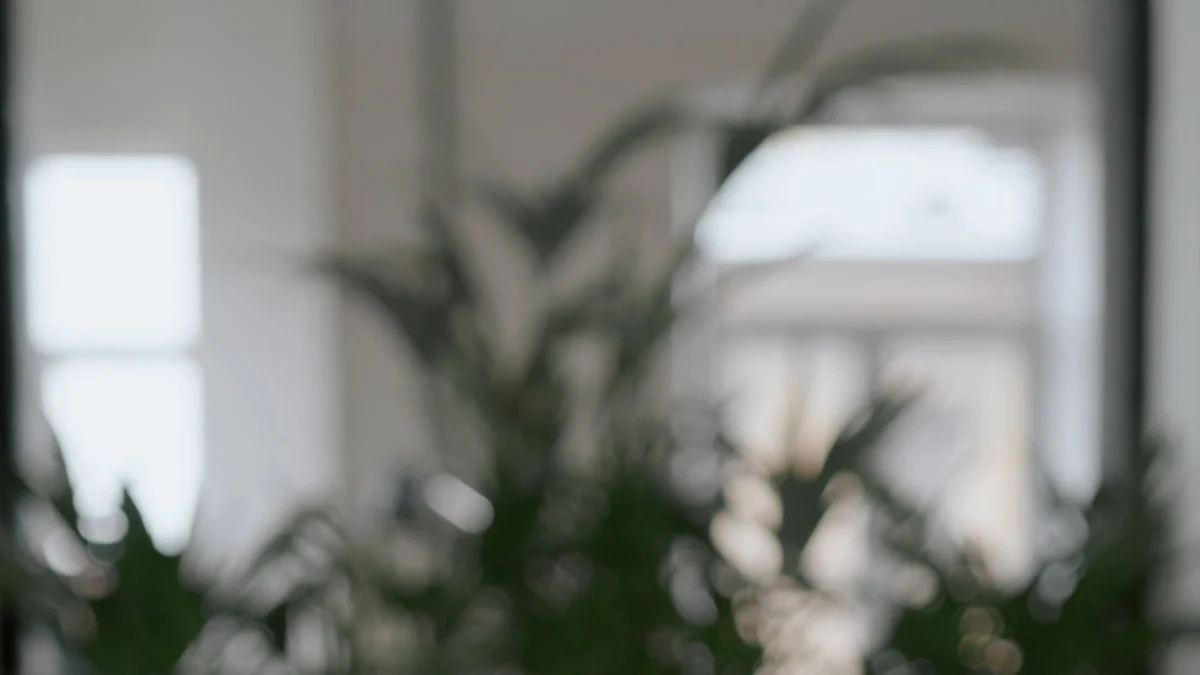
Process improvement methods play a crucial role in enhancing efficiency. They streamline operations, reduce waste, and boost productivity. By adopting a methodology for process improvement, organizations can achieve remarkable results. For instance, Motorola's implementation of Six Sigma led to a 90% reduction in defects and significant cost savings. Similarly, Toyota's use of Six Sigma increased production efficiency and fostered a culture of continuous improvement. These methodologies not only optimize processes but also enhance client satisfaction by delivering higher quality products. To learn more about optimization steps and methodologies, including how they can benefit your clients, reach out to us.
Understanding Process Improvement
Definition of Process Improvement
Process improvement involves systematically evaluating and enhancing business processes to optimize efficiency and productivity. Organizations use various methodologies to identify bottlenecks and streamline workflows. These methodologies aim to reduce inefficiencies and increase profits. By focusing on continuous improvement, businesses can adapt to changing environments and maintain a competitive edge.
Importance of Process Improvement for Efficiency
Process improvement plays a vital role in boosting efficiency across various business operations. It helps organizations pinpoint inefficiencies and implement strategies to address them. According to Opportune Insights, evaluating and improving process efficiency can yield substantial gains. This approach not only enhances productivity but also increases customer satisfaction. As highlighted by Leanscape, continuous improvement leads to better service delivery and client satisfaction. By adopting process improvement techniques, businesses can achieve significant cost savings and improve overall performance.
Key Methods for Process Improvement
Lean Methodology
Lean methodology focuses on eliminating waste and increasing value in processes. This approach, rooted in the Toyota Production System, aims to streamline operations by identifying and removing non-value-adding activities. By doing so, organizations can enhance efficiency and deliver more value to customers. Lean methodology encourages continuous improvement, fostering a culture where employees actively seek ways to optimize processes.
Focus on Eliminating Waste
Lean methodology emphasizes the importance of waste reduction. Waste, in this context, refers to any activity that does not add value to the customer. By identifying and eliminating these inefficiencies, businesses can improve their operational efficiency. For example, Ford Motors implemented Lean principles to streamline production, resulting in significant cost savings and improved quality control.
Increasing Value in Processes
Increasing value in processes involves enhancing the quality and efficiency of operations. Lean methodology encourages organizations to focus on activities that directly contribute to customer satisfaction. By prioritizing value-adding tasks, businesses can improve their service delivery and achieve higher levels of customer satisfaction. The integration of Lean principles with Agile practices has shown to improve efficiency in logistics operations, leading to cost savings.
Six Sigma
Six Sigma is a methodology for process improvement that aims to reduce variation and improve quality. This data-driven approach uses statistical methods to identify and eliminate defects in processes. By focusing on quality control, Six Sigma helps organizations achieve consistent and reliable outcomes.
Reducing Variation
Reducing variation is a key aspect of Six Sigma. By minimizing inconsistencies in processes, businesses can ensure that their products and services meet high-quality standards. Ford Motors' implementation of Six Sigma led to improved quality control and streamlined production processes. This methodology enables organizations to maintain a competitive edge by delivering consistent and reliable products.
Improving Quality
Improving quality is at the heart of Six Sigma. By using statistical tools and techniques, organizations can identify root causes of defects and implement corrective measures. This focus on quality improvement not only enhances customer satisfaction but also leads to significant cost savings. The success of Six Sigma in various industries, including healthcare and manufacturing, highlights its effectiveness as a methodology for process improvement.
Agile
Agile methodology promotes flexibility and responsiveness in process improvement. This iterative approach allows organizations to adapt quickly to changing environments and customer needs. By embracing Agile principles, businesses can enhance their ability to respond to market demands and deliver value to customers.
Iterative Approach
The iterative approach of Agile methodology involves breaking down projects into smaller, manageable tasks. This allows teams to focus on delivering incremental improvements and adapting to feedback. By continuously refining processes, organizations can achieve greater efficiency and effectiveness. Agile methodology empowers teams to respond swiftly to changes, ensuring that they remain aligned with customer expectations.
Enhancing Flexibility and Responsiveness
Enhancing flexibility and responsiveness is a core principle of Agile methodology. By fostering a culture of collaboration and adaptability, organizations can quickly respond to market changes and customer feedback. This approach enables businesses to deliver high-quality products and services in a timely manner. The integration of Agile practices with Lean Six Sigma principles has demonstrated improved efficiency and cost savings in various industries.
Steps to Implement Process Improvement
Implementing process improvement involves a series of optimization steps that guide organizations toward enhanced efficiency. These steps help in identifying inefficiencies, analyzing current processes, and developing strategies for improvement.
Identify Areas for Improvement
Organizations must first identify areas that require enhancement. They should focus on pinpointing inefficiencies within their systems and teams. This involves examining existing workflows and recognizing bottlenecks that hinder productivity. By understanding where problems lie, organizations can prioritize which areas need immediate attention. This step sets the foundation for effective process improvement.
Analyze Current Processes
Once inefficiencies are identified, the next step involves analyzing current processes. Organizations can use various tools to gain insights into their operations:
Tools like Flowcharts: Flowcharts provide a visual representation of processes. They help teams understand the sequence of activities and identify potential areas for optimization. By mapping out each step, organizations can spot redundancies and streamline workflows.
Process Mapping: Process mapping offers a detailed view of how tasks are performed. It highlights interactions between different departments and identifies gaps in communication. This analysis allows organizations to optimize steps by eliminating unnecessary actions and improving coordination.
Develop Improvement Strategies
After analyzing processes, organizations must develop strategies for improvement. This involves setting clear goals and selecting appropriate methods to achieve them:
Setting Goals: Establishing specific, measurable objectives is crucial. Organizations should define what they aim to achieve through process improvement. Clear goals provide direction and help teams stay focused on desired outcomes.
Selecting Appropriate Methods: Choosing the right methodologies is essential for successful implementation. Organizations can opt for Lean, Six Sigma, or Agile approaches based on their unique needs. These methods offer structured frameworks for optimizing steps and enhancing efficiency.
By following these optimization steps, organizations can systematically improve their processes. This approach not only boosts productivity but also enhances customer satisfaction. For more information on how to implement these strategies effectively, reach out to us.
Implement Changes
Implementing changes effectively requires careful planning and execution. Organizations must ensure that all stakeholders understand the changes and their benefits. Clear communication plays a crucial role in this process. Teams should receive detailed instructions and training to adapt to new procedures.
Tips on Executing Changes Effectively
Communicate Clearly: Ensure that everyone involved understands the purpose and benefits of the changes. Use meetings, emails, and presentations to convey information.
Provide Training: Equip teams with the necessary skills and knowledge. Offer workshops and training sessions to help them adapt to new processes.
Set Realistic Timelines: Establish achievable deadlines for implementing changes. This helps teams manage their workload and reduces stress.
Monitor Progress: Track the implementation process regularly. Use checklists and progress reports to ensure that changes occur as planned.
Encourage Feedback: Create an environment where team members feel comfortable sharing their thoughts. Use feedback to make necessary adjustments and improve the process.
Monitor and Adjust
Continuous monitoring and adjustment are essential for successful process improvement. Organizations must regularly assess the effectiveness of implemented changes. This ensures that processes remain efficient and aligned with business goals.
Importance of Continuous Monitoring
Continuous monitoring allows organizations to identify issues early. By keeping a close eye on processes, teams can detect inefficiencies and address them promptly. This proactive approach prevents minor problems from escalating into major setbacks. Regular assessments also provide valuable insights into the effectiveness of changes, helping organizations make informed decisions.
Adaptation Strategies
Adaptation strategies involve making necessary adjustments to processes based on monitoring results. Organizations should remain flexible and open to change. Here are some strategies to consider:
Regular Reviews: Conduct periodic reviews of processes. Use data and feedback to evaluate performance and identify areas for improvement.
Iterative Improvements: Implement small, incremental changes. This approach allows teams to test new ideas and refine processes gradually.
Engage Stakeholders: Involve all relevant parties in the adaptation process. Encourage collaboration and input from different departments to ensure comprehensive improvements.
By implementing these strategies, organizations can maintain efficient processes and achieve their goals. For more information on how to effectively monitor and adjust your systems and teams, reach out to us.
Benefits of Process Improvement
Increased Productivity
Process improvement significantly boosts productivity. By streamlining workflows, organizations can eliminate bottlenecks and enhance efficiency. Teams can focus on value-adding tasks, leading to faster completion of projects. For instance, companies that adopt Lean methodology often see a marked increase in output. Employees work more effectively when processes are clear and optimized. This clarity reduces confusion and enhances overall performance.
Reduced Operational Costs
Reducing operational costs stands as a major benefit of process improvement. By identifying and eliminating waste, organizations can save substantial amounts of money. Lean and Six Sigma methodologies focus on cost reduction by minimizing unnecessary activities. These savings can then be reinvested into other areas of the business. For example, many companies have reported significant cost savings after implementing process improvement strategies. This financial efficiency allows businesses to allocate resources more effectively.
Enhanced Customer Satisfaction
Enhanced customer satisfaction results from improved processes. When organizations deliver high-quality products and services consistently, customer trust grows. Process improvement ensures that businesses meet or exceed customer expectations. By focusing on quality and efficiency, companies can provide better service. This leads to increased customer loyalty and positive word-of-mouth. Engaging with individuals working with processes frequently helps identify areas for enhancement. Listening to feedback and implementing changes based on customer needs further boosts satisfaction.
"Process improvement identification methods involve talking to individuals working with processes frequently, looking at data, and getting ideas from improvements others in the industry are implementing."
Organizations that prioritize process improvement often see a direct impact on customer satisfaction. For more insights on how to enhance your systems and teams, reach out to us.
Common Challenges in Process Improvement
Resistance to Change
Resistance to change often poses a significant challenge in process improvement. Employees may feel uncomfortable with new procedures, fearing the unknown or potential job loss. This reluctance can hinder progress and slow down implementation. To overcome this, organizations should foster an environment of open communication. Engaging employees in the change process and explaining the benefits can ease their concerns. For example, Motorola's successful implementation of Six Sigma involved continuous feedback loops and cross-departmental alignment sessions. These efforts helped reduce defects by more than 90% and saved around $16 billion over a decade.
Lack of Resources
A lack of resources can impede process improvement initiatives. Organizations may struggle with limited budgets, insufficient staff, or inadequate technology. These constraints make it challenging to implement changes effectively. To address this, businesses should prioritize resource optimization. By streamlining workflows and automating tasks, companies can achieve significant cost savings. For instance, optimizing resources led to a 20% reduction in procurement costs and a 30% improvement in order fulfillment accuracy. Investing in Business Process Management (BPM) software can also help reduce employee onboarding time by half and increase retention rates by 58%.
Inadequate Training
Inadequate training presents another hurdle in process improvement. Employees need the right skills and knowledge to adapt to new processes. Without proper training, they may struggle to perform tasks efficiently, leading to errors and decreased productivity. Organizations should invest in comprehensive training programs to equip their teams with the necessary competencies. Providing workshops and hands-on sessions ensures that employees understand new procedures and can execute them effectively. This approach not only enhances workforce productivity but also contributes to smoother procedures, resulting in higher revenue and customer satisfaction.
"Smoother procedures lead to a happier workforce, resulting in higher productivity and revenue."
Addressing these common challenges requires a strategic approach. By fostering a culture of openness, optimizing resources, and investing in training, organizations can successfully navigate the complexities of process improvement. For more insights on overcoming these challenges and enhancing your systems and teams, reach out to us.
Case Studies of Successful Process Improvement
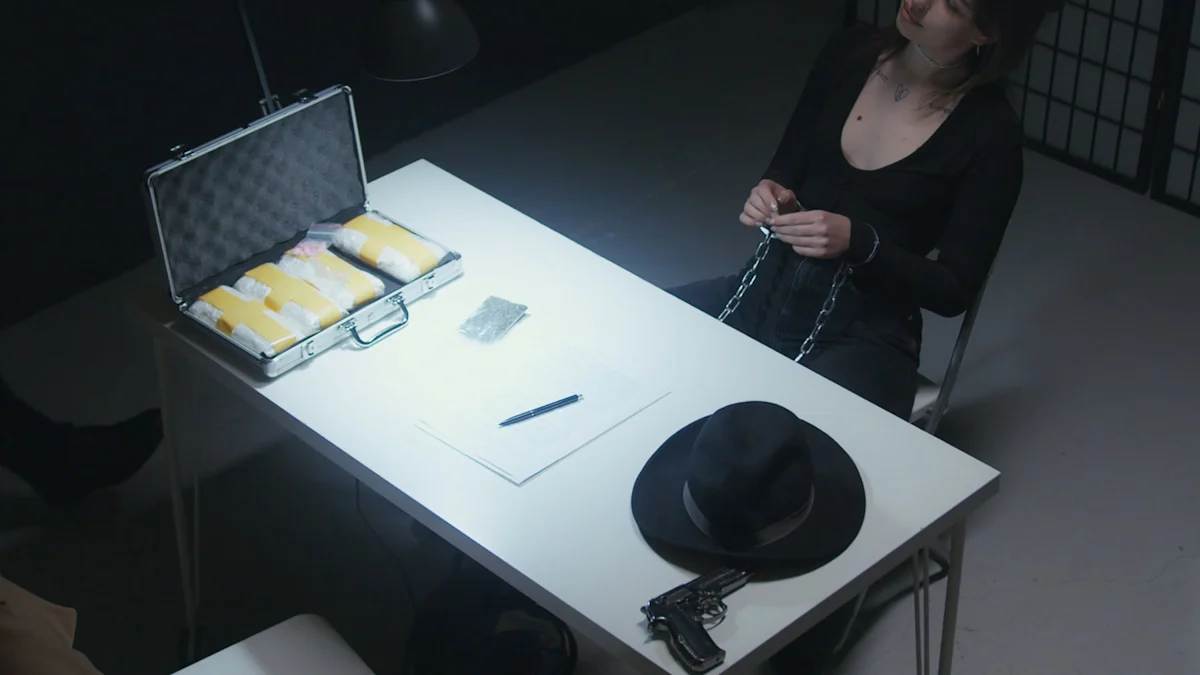
Example 1: Toyota's Lean Manufacturing
Toyota stands as a pioneer in implementing Lean Manufacturing, a methodology that focuses on waste elimination and value enhancement. This approach revolutionized their production processes, leading to significant improvements in efficiency and quality. By identifying non-value-adding activities, Toyota streamlined operations and reduced costs. Employees actively participated in continuous improvement initiatives, fostering a culture of innovation and collaboration.
"Lean Manufacturing emphasizes the importance of eliminating waste and increasing value in processes."
Toyota's success with Lean Manufacturing serves as a model for other organizations seeking to enhance efficiency. The company's commitment to continuous improvement not only boosted productivity but also improved customer satisfaction. By delivering high-quality products consistently, Toyota strengthened its market position and gained a competitive edge.
Example 2: Motorola's Six Sigma Implementation
Motorola's implementation of Six Sigma marked a significant milestone in process improvement. This data-driven methodology focuses on reducing variation and improving quality through statistical analysis. Motorola achieved remarkable results by identifying and eliminating defects in their processes. The company reported a 90% reduction in defects, leading to substantial cost savings and enhanced product quality.
"Six Sigma aims to reduce variation and improve quality by using statistical methods."
Motorola's success with Six Sigma highlights the effectiveness of this methodology in achieving consistent and reliable outcomes. By focusing on quality control, the company enhanced customer satisfaction and maintained a competitive edge. The integration of Six Sigma principles into Motorola's operations not only improved efficiency but also fostered a culture of excellence and continuous improvement.
These case studies demonstrate the transformative impact of process improvement methodologies. Organizations like Toyota and Motorola have successfully enhanced efficiency and productivity by adopting Lean Manufacturing and Six Sigma. By focusing on waste elimination and quality improvement, these companies achieved significant cost savings and improved customer satisfaction. For more insights on how to implement these strategies effectively in your systems and teams, reach out to us.
Tools and Resources for Process Improvement
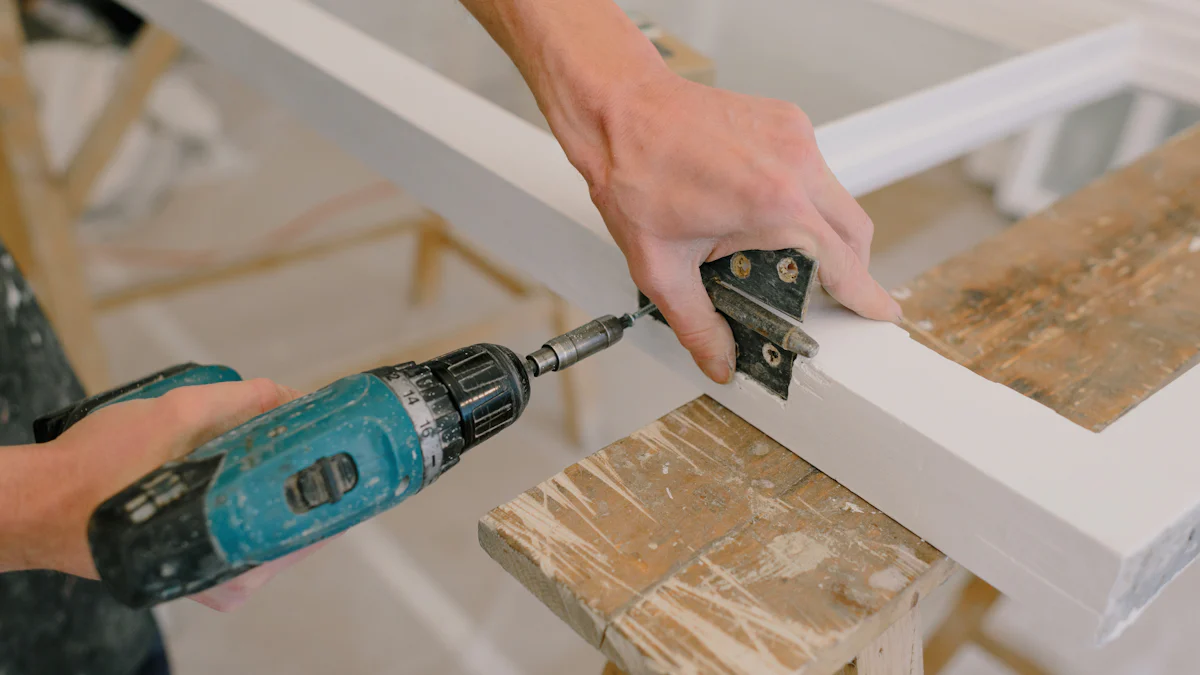
Organizations seeking to enhance efficiency through process improvement can leverage various tools and resources. These resources provide valuable support in implementing methodologies like Lean, Six Sigma, and Agile. By utilizing these tools, businesses can streamline operations, reduce waste, and improve productivity.
Software Solutions
Software solutions play a crucial role in process improvement. They offer automated tools that help organizations analyze and optimize workflows. For instance, Business Process Management (BPM) software enables companies to map out processes, identify bottlenecks, and implement changes efficiently. These solutions provide real-time data and analytics, allowing teams to make informed decisions.
"Software solutions provide real-time data and analytics, allowing teams to make informed decisions."
Many organizations have successfully used software solutions to enhance their systems and teams. For example, Toyota's implementation of Six Sigma involved using software to track defects and monitor improvements. This approach led to significant cost savings and improved quality control. Clients can benefit from similar software solutions to achieve remarkable results in their operations.
Training Programs
Training programs equip employees with the necessary skills and knowledge for process improvement. These programs focus on teaching methodologies like Lean, Six Sigma, and Agile. By participating in training sessions, teams learn how to identify inefficiencies and implement effective strategies.
"Training programs equip employees with the necessary skills and knowledge for process improvement."
Organizations that invest in training programs often see a direct impact on their systems and teams. For instance, Motorola's success with Six Sigma involved comprehensive training for employees. This approach ensured that everyone understood the methodology and could apply it effectively. Clients can enhance their teams' capabilities by enrolling in similar training programs.
Professional Consultants
Professional consultants offer expert guidance in process improvement. They bring valuable experience and insights to help organizations optimize their operations. Consultants work closely with clients to identify areas for improvement and develop tailored strategies.
"Professional consultants offer expert guidance in process improvement."
Engaging with professional consultants can lead to significant improvements in systems and teams. For example, Toyota's Lean Manufacturing success involved collaboration with consultants who provided expertise in waste elimination and value enhancement. Clients can benefit from similar partnerships to achieve their process improvement goals.
By leveraging these tools and resources, organizations can enhance their efficiency and productivity. Software solutions, training programs, and professional consultants provide valuable support in implementing process improvement methodologies. For more information on how to utilize these resources effectively, reach out to us.
Future Trends in Process Improvement
Integration of AI and Automation
Artificial Intelligence (AI) and automation are transforming process improvement. They offer advanced solutions for enhancing efficiency and productivity. AI analyzes large datasets to identify patterns and predict outcomes. This capability helps organizations make informed decisions quickly. Automation streamlines repetitive tasks, reducing human error and freeing up resources for more strategic activities.
Project Management Tools play a crucial role in this integration. They enhance planning, execution, monitoring, and collaboration. These tools provide structured approaches for improving processes. Key components include project planning software, risk management tools, communication platforms, and performance dashboards. By leveraging these technologies, organizations can optimize their systems and teams effectively.
"AI and automation streamline repetitive tasks, reducing human error and freeing up resources for more strategic activities."
Organizations that embrace AI and automation see significant improvements in efficiency. They can respond swiftly to market changes and customer demands. This adaptability ensures they remain competitive in a rapidly evolving business landscape. For more insights on integrating AI and automation into your systems and teams, reach out to us.
Emphasis on Sustainability
Sustainability is becoming a key focus in process improvement. Organizations recognize the importance of minimizing environmental impact while maximizing efficiency. Sustainable practices not only benefit the planet but also enhance brand reputation and customer loyalty.
Ntiva Onsite Audit services help organizations identify inefficiencies and performance gaps. A tech consultant interviews key staff members to learn about the business structure. They document and analyze existing processes, systems, and resources. This comprehensive approach uncovers areas for improvement, promoting sustainable practices.
"Sustainable practices not only benefit the planet but also enhance brand reputation and customer loyalty."
By prioritizing sustainability, organizations can reduce waste and conserve resources. This approach aligns with consumer expectations and regulatory requirements. It also positions businesses as leaders in environmental responsibility. For more information on implementing sustainable practices in your systems and teams, reach out to us.
These future trends highlight the evolving landscape of process improvement. AI, automation, and sustainability offer exciting opportunities for enhancing efficiency and productivity. Organizations that embrace these trends will achieve remarkable results. For more insights on how to leverage these trends in your systems and teams, reach out to us.
Process improvement methods offer numerous benefits, including increased productivity, reduced operational costs, and enhanced customer satisfaction. By implementing these strategies, organizations can streamline their systems and teams, leading to significant efficiency gains. The integration of AI and automation further enhances these efforts, providing data-driven insights and scalability. As highlighted in studies, AI optimizes processes and reduces waste, contributing to sustainability. Organizations must embrace continuous adaptation to stay competitive. For those eager to enhance their operations, now is the time to start implementing these methods. For more insights, reach out to us.