Choosing the Best Business Process Improvement Methodologies for Your Team
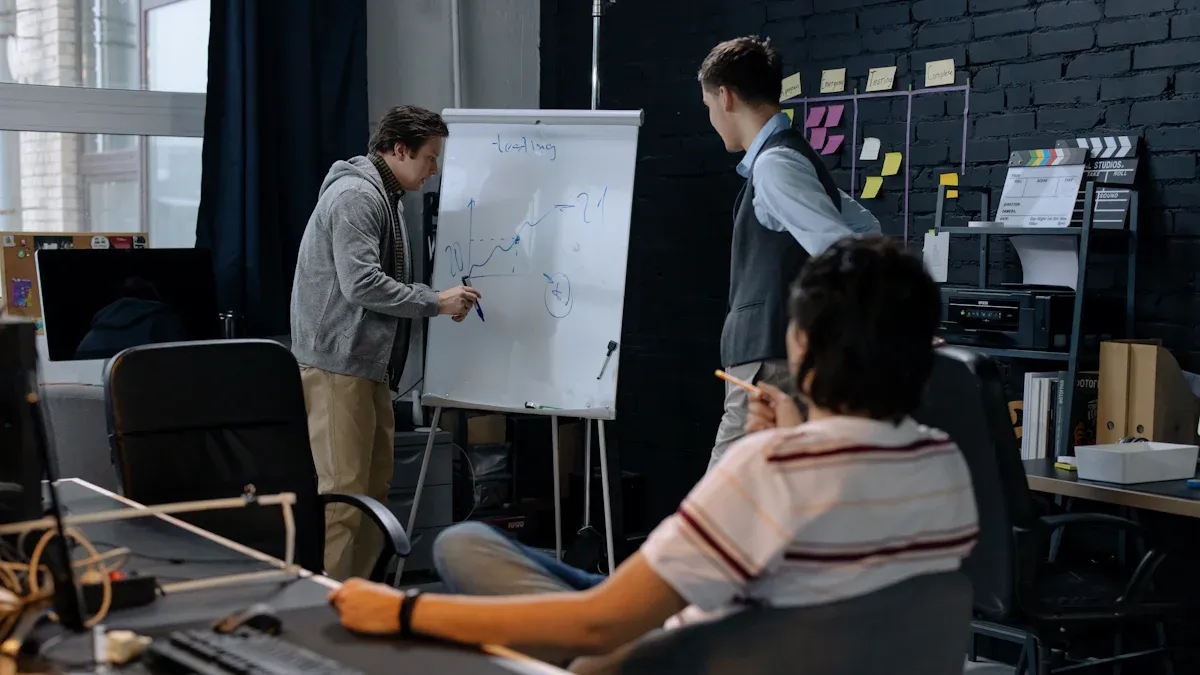
Selecting the appropriate business process improvement methodologies can revolutionize team operations. Each team encounters distinct challenges, whether it pertains to refining workflows, boosting collaboration, or providing superior results to clients and customers. By aligning these methodologies with specific team objectives, organizations can unlock enhanced efficiency and attain significant outcomes. Teams should meticulously assess optimization steps to guarantee they align with their structure and goals. This deliberate strategy ensures that the selected methodology promotes sustainable growth and encourages innovation throughout processes.
Key Takeaways
Picking the right method can improve how your team works.
Look at team size to find a good fit, like Agile for small teams or Six Sigma for big ones.
Match methods to your industry needs and business goals for better results.
Find problems and use methods that fix them and show clear improvements.
Choose methods that can grow and change with your team’s needs.
Involve everyone to work together and build a habit of improving.
Check progress often to see if the methods are working well.
Get help or training to use methods correctly and avoid mistakes.
Understanding Business Process Improvement Methodologies
Definition and Purpose
Business Process Improvement Methodologies refer to structured approaches designed to analyze, optimize, and enhance organizational processes. These methodologies aim to identify inefficiencies, reduce waste, and improve overall performance. By focusing on measurable outcomes, they help teams achieve specific goals, such as faster delivery times, higher quality outputs, or cost savings.
Organizations often use a data-driven approach to define and evaluate these methodologies. For example:
Metrics and Key Performance Indicators (KPIs) are analyzed to assess the health of existing processes.
Teams set measurable goals, such as reducing production times or increasing customer satisfaction scores.
Progress is tracked over time to ensure continuous improvement.
A variety of industries have successfully implemented these methodologies to address challenges. For instance:
Industry | Challenge | Improvement Projects | Outcome |
---|---|---|---|
Education | Inefficiencies in student enrollment | Digitizing student enrollment processes | |
Logistics and Transport | Route inefficiencies and high fuel costs | Optimizing fleet management | Lower operational costs and improved delivery times |
Financial Services | Customer service and operational efficiency | Enhancing customer service with chatbots | Improved customer experience and faster query resolution |
Construction | Project delays and budget overruns | Streamlining project management | Timely project completion and reduced costs |
These examples highlight how Business Process Improvement Methodologies can drive tangible results across diverse sectors.
Why They Are Essential for Teams
Effective process improvement methodologies are critical for teams aiming to enhance performance and achieve long-term success. They provide a framework for identifying hidden inefficiencies and implementing solutions that deliver measurable benefits.
Several reasons underscore their importance:
Lean and continuous improvement principles streamline operations, reducing unnecessary steps and waste.
Data-driven approaches, such as Lean Six Sigma, enable teams to analyze processes systematically and make informed decisions.
Automating repetitive tasks, like email communication, minimizes manual effort and boosts productivity.
Techniques like Kaizen foster a culture of continuous improvement, encouraging teams to innovate and refine their workflows regularly.
For example, the Prime Vector team successfully reduced their process time to just 59 minutes while maintaining efficiency. This achievement demonstrates how structured methodologies can transform team performance. Similarly, Lean Six Sigma combines waste reduction with statistical analysis to address problem areas effectively.
By adopting these methodologies, teams can improve collaboration, enhance decision-making, and achieve their objectives more efficiently. Organizations that prioritize process improvement create an environment where innovation thrives, ultimately driving sustainable growth.
Factors to Consider When Choosing a Methodology
Team Size and Structure
The size and structure of a team play a pivotal role in determining the most suitable business process improvement methodology. Smaller teams often benefit from methodologies that emphasize simplicity and agility, such as Kanban or Agile. These approaches allow teams to adapt quickly and focus on incremental improvements without overwhelming resources. Larger teams, on the other hand, may require more structured methodologies like Lean Six Sigma or Total Quality Management (TQM). These frameworks provide detailed guidelines and processes that help coordinate efforts across multiple departments or stakeholders.
Hierarchical structures may favor methodologies with clear roles and responsibilities, such as Six Sigma, which assigns specific roles like Green Belts and Black Belts to team members. Flat organizational structures, however, thrive on collaborative approaches like Kaizen, which encourage all team members to contribute ideas for continuous improvement.
Tip: Teams should evaluate their communication dynamics and decision-making processes to identify methodologies that align with their operational style.
Industry and Business Objectives
The industry in which a team operates and its overarching business objectives significantly influence the choice of methodology. For example, manufacturing teams often prioritize waste reduction and efficiency, making Lean or Lean Six Sigma ideal choices. Software development teams may focus on flexibility and speed, favoring Agile or Kanban methodologies.
Business objectives also shape the selection process. Teams aiming to explore new markets or generate insights may benefit from qualitative methodologies, while those focused on cost reduction or operational efficiency might prefer quantitative approaches. The table below illustrates how objectives align with recommended methodologies:
Objective Type | Recommended Methodology | Characteristics |
---|---|---|
Exploratory Objectives | Qualitative | Ideal for understanding new markets and generating hypotheses. |
Descriptive Objectives | Quantitative | Best for describing population characteristics and understanding behavior frequency. |
Short Timeline | Quantitative | Quick results through online surveys and secondary data analysis. |
Medium to Long Timeline | Qualitative | Comprehensive studies requiring more time for data collection and analysis. |
Limited Budget | Quantitative | Cost-effective methods like online surveys providing actionable insights. |
Moderate Budget | Qualitative | Balances cost with depth of insight through methods like telephone surveys. |
Generous Budget | Hybrid of Quantitative and Qualitative | Comprehensive methodologies for detailed and reliable data. |
Teams should assess their industry-specific challenges and align their methodology choice with their strategic goals to maximize impact.
Current Challenges and Pain Points
Identifying current challenges and pain points is essential for selecting the right methodology. Teams often face issues such as inefficiencies, high error rates, or low customer satisfaction. Metrics provide valuable insights into these areas, helping teams pinpoint where improvements are needed.
Metric Type | Description |
---|---|
Completion or success | Measures whether users can complete tasks effectively, indicating design success or failure. |
Duration | Tracks the average time users spend on tasks, revealing design complexity and navigation efficiency. |
Error | Highlights user actions that lead to confusion, indicating areas needing improvement in UI. |
Satisfaction | Gauges overall user satisfaction through metrics like SUS or NPS, reflecting user sentiment. |
For example, a logistics team struggling with route inefficiencies might use duration metrics to identify bottlenecks and adopt Lean methodologies to streamline operations. Similarly, a customer service team facing low satisfaction scores could implement Kaizen to foster continuous improvement and enhance user experiences.
Teams should prioritize methodologies that address their most pressing challenges while remaining adaptable to future needs. By leveraging data-driven insights, they can ensure their chosen approach delivers measurable results.
Scalability and Flexibility
Scalability and flexibility are essential considerations when selecting business process improvement methodologies. Teams often face evolving demands, whether due to market changes, organizational growth, or shifting customer expectations. A methodology that adapts to these changes ensures long-term success and minimizes disruptions.
Scalability refers to a system's ability to handle increased workloads or expand operations without compromising performance. Flexible methodologies, on the other hand, allow teams to adjust processes to meet unique challenges or opportunities. Together, these qualities empower organizations to remain competitive and responsive.
Why Scalability and Flexibility Matter
Modern businesses operate in dynamic environments. Teams must adopt methodologies that can grow alongside their operations. For instance:
Rapid expansion requires systems that adapt quickly to market changes.
Real-time data access improves decision-making by providing actionable insights.
Extensible frameworks allow modular upgrades without disrupting core operations.
Flexible methodologies also enhance resource efficiency. Cloud-based solutions, for example, offer scalable resources that adjust to business needs. Virtualization further increases flexibility, enabling teams to allocate resources effectively. Modular systems simplify scaling by allowing individual components to be upgraded independently.
The Role of Technology in Scalability and Flexibility
Technology plays a pivotal role in enhancing scalability and flexibility. Artificial intelligence (AI) and predictive analytics are prime examples. AI automates repetitive tasks, reducing operational costs and freeing employees to focus on high-value activities. It also analyzes data to support strategic planning and resource allocation.
Predictive analytics forecasts demand, optimizing inventory and minimizing waste. These tools not only improve productivity but also foster innovation. AI systems, in particular, scale effortlessly to meet increasing workloads, ensuring teams can handle growth without major changes.
Practical Applications for Teams
Teams across industries benefit from scalable and flexible methodologies. For example:
Logistics teams use predictive analytics to optimize delivery routes, reducing fuel costs and improving efficiency.
Customer service teams implement AI tools to enhance user experiences, driving satisfaction and loyalty.
Manufacturing teams adopt modular systems to streamline production processes, ensuring seamless scaling as demand increases.
By prioritizing scalability and flexibility, organizations can future-proof their operations. Teams equipped with adaptable methodologies can respond to challenges and seize opportunities, ensuring sustained growth and success.
Tip: When evaluating business process improvement methodologies, teams should consider how well each approach supports scalability and flexibility. This ensures the chosen methodology aligns with both current needs and future goals.
Popular Business Process Improvement Methodologies
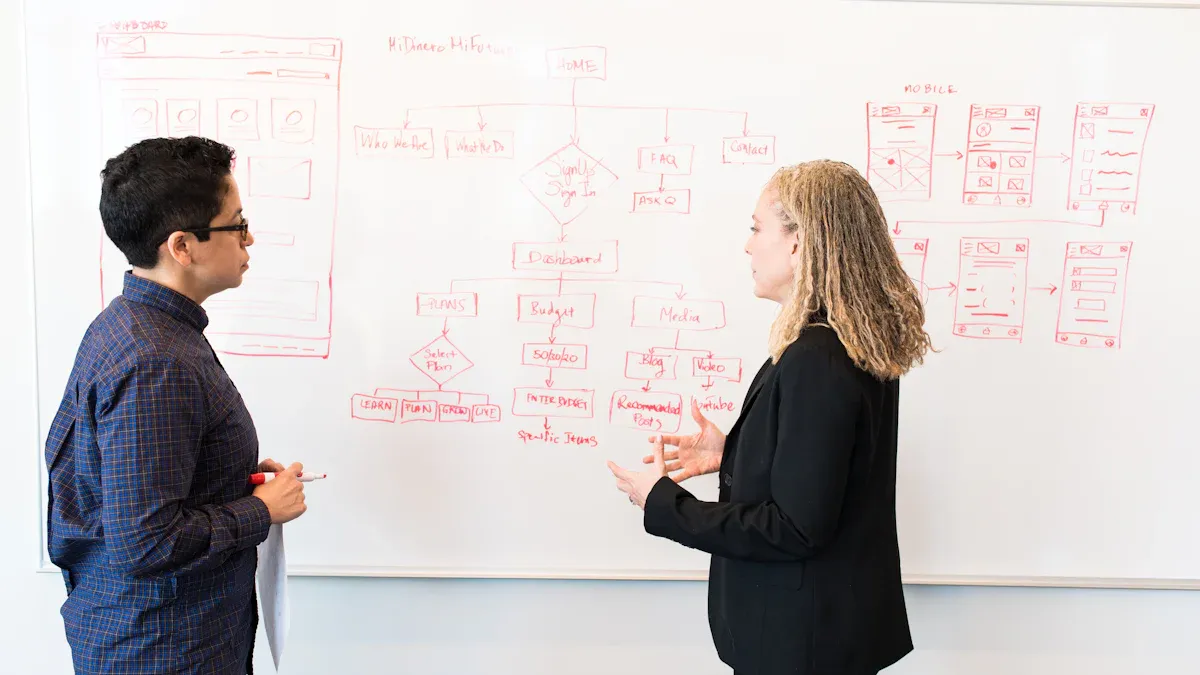
Six Sigma
Six Sigma is a data-driven methodology that focuses on improving process quality by identifying and eliminating defects. It uses statistical tools and techniques to analyze processes and ensure consistent results. Organizations often adopt Six Sigma to enhance efficiency, reduce waste, and improve customer satisfaction.
The effectiveness of Six Sigma lies in its reliance on measurable performance metrics. For example, it tracks key indicators such as defects per million opportunities (DPMO), first pass yield (FPY), and throughput yield (TY). These metrics help teams identify inefficiencies and implement targeted improvements.
Key Metrics in Six Sigma:
DPMO: Measures the number of defects in a process per million opportunities.
FPY: Tracks the percentage of units passing inspection on the first attempt.
TY: Monitors the percentage of units completing a process without defects.
A structured approach like Six Sigma ensures that teams can achieve their goals with precision. For instance, General Electric successfully reduced defects and improved efficiency by implementing Six Sigma principles. This methodology remains a popular choice for teams aiming to optimize processes and deliver high-quality outcomes.
Lean
Lean focuses on eliminating waste and maximizing value in business processes. It emphasizes streamlining workflows, reducing unnecessary steps, and improving resource utilization. Teams across industries use Lean to enhance productivity and deliver better results to customers.
Lean relies on specific performance metrics to validate its effectiveness. These include process efficiency, process effectiveness, and customer satisfaction. By monitoring these metrics, teams can identify areas for improvement and implement changes that drive measurable results.
KPI Type | Description |
---|---|
Process Efficiency | Focuses on reducing waste, shortening cycle times, and improving resource utilization. |
Process Effectiveness | Assesses how well processes achieve their intended goals, including metrics like defect rate. |
Customer Satisfaction | Captures customer feedback through surveys and ratings to measure how well processes meet expectations. |
Toyota serves as a prime example of Lean's success. By involving employees in continuous improvement initiatives, the company achieved significant gains in efficiency and quality. Lean's adaptability makes it suitable for teams of all sizes and industries.
Lean Six Sigma
Lean Six Sigma combines the principles of Lean and Six Sigma to create a comprehensive approach to process improvement. It focuses on eliminating waste while maintaining a data-driven framework for quality enhancement. This hybrid methodology enables teams to address inefficiencies and achieve sustainable results.
Organizations like Amazon and Ford Motor Company have successfully implemented Lean Six Sigma. Amazon streamlined its processes and enhanced customer satisfaction by eliminating waste, while Ford improved efficiency and reduced costs. These examples highlight the versatility of Lean Six Sigma in addressing diverse business challenges.
The methodology's structured approach ensures that teams can track progress and measure success. By integrating Lean's focus on waste reduction with Six Sigma's emphasis on statistical analysis, Lean Six Sigma provides a balanced framework for achieving operational excellence.
Kaizen
Kaizen, a Japanese term meaning "continuous improvement," emphasizes small, incremental changes to enhance processes over time. This methodology fosters a culture where every team member actively participates in identifying inefficiencies and suggesting improvements. It thrives on collaboration and encourages teams to focus on long-term progress rather than quick fixes.
Kaizen operates on five core principles: teamwork, personal discipline, improved morale, quality circles, and suggestions for improvement. Teams often conduct regular meetings to discuss challenges and brainstorm solutions. For example, a manufacturing team might identify bottlenecks in production and implement minor adjustments to streamline workflows. Over time, these small changes lead to significant improvements in efficiency and quality.
This methodology suits teams that value collective input and aim to build a culture of continuous learning. By involving all members in the improvement process, Kaizen not only enhances operations but also boosts employee engagement and satisfaction.
Kanban
Kanban is a visual workflow management tool designed to optimize task flow and improve efficiency. Teams use Kanban boards to visualize tasks, track progress, and identify bottlenecks. Each task moves through columns representing different stages of completion, such as "To Do," "In Progress," and "Done."
Kanban's effectiveness lies in its simplicity and adaptability. Teams can quickly identify where tasks are delayed and allocate resources to address issues. Research shows that organizations using Kanban tools experienced a 45% increase in productivity and a 30% reduction in delivery time. These results highlight Kanban's ability to streamline processes and enhance team performance.
Key principles of Kanban include limiting work in progress (WIP) to prevent overload and focusing on reducing lead time and cycle time. For instance, a software development team might use Kanban to manage feature updates, ensuring tasks move smoothly from planning to deployment. By visualizing workflows, teams gain clarity and improve collaboration.
Agile
Agile is a flexible and iterative approach to project management and process improvement. It prioritizes adaptability, collaboration, and customer satisfaction. Teams using Agile break projects into smaller, manageable tasks called "sprints," allowing them to deliver results incrementally and respond to changes quickly.
Agile's core values include individuals and interactions, working solutions, customer collaboration, and responding to change. This methodology is particularly popular in software development, where teams must adapt to evolving requirements. For example, an Agile team might release a minimum viable product (MVP) to gather user feedback and refine features in subsequent iterations.
Agile's benefits extend beyond software development. Teams in marketing, education, and other industries use Agile to improve efficiency and foster innovation. By focusing on collaboration and continuous improvement, Agile helps teams achieve their goals while maintaining flexibility.
Total Quality Management (TQM)
Total Quality Management (TQM) is a comprehensive approach aimed at improving the quality of products and services by focusing on customer satisfaction. This methodology involves every team member, from top management to frontline employees, in the pursuit of continuous improvement. TQM emphasizes a proactive approach to identifying and resolving issues before they escalate.
Key principles of TQM include customer focus, total employee involvement, process-centered thinking, and continuous improvement. Teams often use tools like flowcharts, checklists, and cause-and-effect diagrams to analyze processes and identify areas for enhancement. For example, a manufacturing team might use TQM to reduce defects in production by standardizing workflows and training employees on best practices.
TQM also fosters a culture of accountability and collaboration. Teams work together to set quality objectives, monitor progress, and celebrate achievements. This methodology suits organizations that prioritize long-term quality improvements and customer loyalty. By adopting TQM, teams can enhance efficiency, reduce costs, and deliver superior value to customers.
Business Process Management (BPM)
Business Process Management (BPM) focuses on designing, analyzing, and optimizing business processes to achieve organizational goals. This methodology provides a structured framework for managing workflows, ensuring that processes align with strategic objectives. BPM often incorporates technology to automate repetitive tasks and improve efficiency.
The BPM lifecycle consists of five stages: design, modeling, execution, monitoring, and optimization. During the design phase, teams map out processes to identify inefficiencies. Modeling involves simulating workflows to predict outcomes and test improvements. Execution focuses on implementing changes, while monitoring tracks performance using key metrics. Finally, optimization ensures that processes remain effective over time.
BPM is particularly beneficial for teams dealing with complex workflows or frequent changes. For instance, a logistics team might use BPM software to streamline supply chain operations, reducing delivery times and costs. By adopting BPM, organizations can enhance agility, improve decision-making, and achieve sustainable growth.
Theory of Constraints
The Theory of Constraints (TOC) is a methodology that identifies and addresses the most significant bottleneck in a process. This approach operates on the principle that every system has at least one constraint limiting its performance. By focusing on this constraint, teams can achieve significant improvements with minimal effort.
TOC follows a five-step process: identify the constraint, exploit it, subordinate other processes to it, elevate its capacity, and repeat the cycle. For example, a production team might identify a slow machine as the constraint and prioritize its maintenance to increase output. Once the bottleneck is resolved, the team moves on to the next limiting factor.
This methodology is ideal for teams seeking quick wins and measurable results. TOC encourages a systematic approach to problem-solving, ensuring that resources are allocated effectively. By addressing constraints, teams can enhance productivity, reduce waste, and achieve their objectives more efficiently.
Tip: Teams should regularly review their processes to identify new constraints and ensure continuous improvement.
Comparing Business Process Improvement Methodologies
Complexity and Ease of Implementation
The complexity of a business process improvement methodology often determines how easily a team can adopt and implement it. Some methodologies, like Kanban, are straightforward and require minimal training, making them ideal for teams seeking quick wins. Others, such as Six Sigma, involve advanced statistical tools and structured roles, which may demand significant time and resources for training and execution.
Teams can evaluate complexity and ease of implementation using specific criteria. For example:
Criteria | Description |
---|---|
Financial Metrics | Evaluates economic viability and profitability of alternatives, ensuring alignment with financial objectives. |
Strategic Alignment | Ensures decisions reflect the organization’s vision, mission, and competitive positioning. |
Risk Assessment | Provides a framework for assessing and prioritizing operational, regulatory, reputational, and environmental risks. |
Stakeholder Engagement | Considers criteria such as customer commitment, employee engagement, and community support. |
Technical Knowledge | Includes criteria related to expertise, availability of skilled personnel, and technological compatibility. |
Consistency Ratios | Measures coherence in pairwise comparisons, with low ratios indicating high consistency. |
Inconsistency Index | Quantifies the level of inconsistency in pairwise comparison matrices, aiding in decision refinement. |
Judgment Quantification | Translates qualitative assessments into numerical values for structured evaluation. |
By assessing these factors, teams can identify methodologies that align with their capabilities and resources. For instance, a small team with limited technical expertise might opt for Kaizen, while a larger organization with specialized personnel could implement Lean Six Sigma.
Scalability for Different Team Sizes
Scalability plays a critical role in determining whether a methodology can adapt to teams of varying sizes. Smaller teams often benefit from flexible approaches like Agile or Kanban, which allow for incremental adjustments without overwhelming resources. Larger teams, however, may require structured methodologies such as Total Quality Management (TQM) or Business Process Management (BPM) to coordinate efforts across multiple departments.
A peer-reviewed study involving 15,078 participants across 4,013 teams analyzed the scalability of Agile methodologies. The findings revealed minimal differences in responsiveness and autonomy among scaling approaches, suggesting that team experience and organizational size often outweigh the choice of methodology. This highlights the importance of tailoring the implementation process to the unique needs of the team rather than relying solely on the methodology itself.
Scalable methodologies ensure that teams can grow and adapt without compromising efficiency. For example, cloud-based BPM systems allow organizations to expand operations seamlessly by automating repetitive tasks and optimizing workflows. Teams should prioritize methodologies that offer both flexibility and scalability to support long-term growth.
Suitability for Various Industries
Different industries face unique challenges, making it essential to select a methodology that aligns with specific operational needs. Manufacturing teams often prioritize waste reduction and efficiency, making Lean or Lean Six Sigma ideal choices. In contrast, software development teams may focus on adaptability and speed, favoring Agile or Kanban.
Healthcare organizations frequently adopt Total Quality Management (TQM) to enhance patient care and ensure compliance with regulatory standards. Logistics teams, on the other hand, might use the Theory of Constraints to address bottlenecks and improve delivery times. Each methodology offers distinct advantages, but its effectiveness depends on how well it addresses the industry's pain points.
Teams should evaluate their industry-specific requirements and choose a methodology that aligns with their strategic goals. By doing so, they can maximize the impact of their business process improvement efforts and achieve measurable results.
Focus Areas (e.g., cost reduction, quality improvement, speed)
Business process improvement methodologies often target three critical focus areas: cost reduction, quality improvement, and speed. Each area addresses specific operational goals, helping teams optimize their workflows and achieve measurable results.
Cost Reduction
Reducing costs remains a top priority for many organizations. Methodologies like Lean and Six Sigma excel in identifying waste and inefficiencies that inflate expenses. Lean focuses on eliminating non-value-adding activities, while Six Sigma uses data-driven analysis to minimize defects and rework. Together, they help teams streamline operations and cut unnecessary costs.
For example, General Electric achieved over $2 billion in savings by implementing Six Sigma principles. Teams analyzed processes, identified inefficiencies, and applied targeted improvements. This approach not only reduced costs but also enhanced overall productivity. By adopting similar methodologies, organizations can allocate resources more effectively and improve their bottom line.
Quality Improvement
Improving quality ensures that products and services meet or exceed customer expectations. Methodologies like Total Quality Management (TQM) and Kaizen emphasize continuous improvement and employee involvement. These approaches encourage teams to identify defects, standardize processes, and maintain high-quality standards.
Several companies have demonstrated the effectiveness of these methodologies. Toyota tracks daily quality metrics across all production areas, ensuring consistent performance. Boeing reduced production defects by 50% over three years through quality-focused initiatives. Ford Motor Company achieved a 60% reduction in defect rates within six months by refining its processes. These examples highlight how structured methodologies can drive significant quality improvements.
Company | Improvement Type | Measurable Result |
---|---|---|
Toyota | Quality Improvement | Daily quality metrics tracked across all production areas |
Boeing | Quality Improvement | 50% reduction in production defects over three years |
General Electric | Cost Reduction | Over $2 billion in savings through process improvements |
Ford Motor Company | Quality Improvement | 60% reduction in defect rates within six months |
Speed
Speed plays a crucial role in meeting customer demands and staying competitive. Agile and Kanban methodologies prioritize faster delivery by breaking tasks into smaller, manageable units. These approaches allow teams to adapt quickly to changes and maintain steady progress.
For instance, Kanban's visual workflow system helps teams identify bottlenecks and allocate resources efficiently. Agile's iterative process ensures that teams deliver results incrementally, reducing delays. By focusing on speed, organizations can enhance customer satisfaction and gain a competitive edge.
Tip: Teams should evaluate their primary goals—whether reducing costs, improving quality, or increasing speed—and select methodologies that align with these objectives. This ensures that their efforts yield the most impactful results.
By targeting these focus areas, organizations can achieve operational excellence and drive sustainable growth. Teams that adopt the right methodologies can address their unique challenges and deliver measurable improvements.
Steps to Identify the Best Fit for Your Team
Assessing Team Needs and Goals
Identifying the best methodology begins with understanding the unique needs and goals of the team. Teams should evaluate their current performance metrics and align them with organizational objectives. For example, a team aiming to increase customer retention might prioritize methodologies that focus on quality improvement and customer satisfaction.
To assess team needs effectively, consider the following steps:
Outline Key Performance Indicators (KPIs): Define measurable goals, such as reducing project costs by $500 or increasing customer acquisition by 20% annually.
Gather Relevant Data: Use reporting tools to collect data on team performance, such as task completion rates or customer feedback scores.
Analyze Data Trends: Compare current performance against KPIs to identify strengths and weaknesses.
Set Clear Objectives: Establish actionable goals based on the analysis, such as improving task efficiency or reducing error rates.
Provide Feedback and Training: Offer regular reviews and equip team members with the skills needed to meet objectives.
For instance, a logistics team might analyze delivery times and identify delays caused by inefficient routing. By aligning their goals with a methodology like Lean, they can streamline operations and achieve faster delivery times. Teams that take a data-driven approach to assess their needs can ensure their chosen methodology addresses specific challenges.
Tip: Teams should involve all members in the assessment process to gain diverse perspectives and foster a sense of ownership in achieving goals.
Evaluating Methodology Strengths and Weaknesses
Each methodology offers unique strengths and potential drawbacks. Teams must evaluate these factors to determine which approach aligns best with their objectives and resources. For example:
Six Sigma: This methodology excels in quality control and data-driven decision-making. It enhances product consistency and reduces errors, making it ideal for manufacturing teams. However, its structured framework may introduce bureaucracy, which could slow down decision-making.
Lean: Known for eliminating waste and maximizing value, Lean suits teams focused on efficiency. Its simplicity makes it accessible, but it may not address complex quality issues as effectively as Six Sigma.
Agile: Agile promotes flexibility and collaboration, making it a popular choice for software development teams. While it adapts well to changing requirements, it may lack the structure needed for large-scale projects.
Teams can use a comparative analysis to weigh the pros and cons of each methodology. For example:
Methodology | Strengths | Weaknesses |
---|---|---|
Six Sigma | Enhances quality and reduces defects | Can be bureaucratic and resource-intensive |
Lean | Streamlines processes and reduces waste | May not address complex quality issues |
Agile | Flexible and collaborative | Lacks structure for large-scale projects |
By understanding these factors, teams can select a methodology that complements their strengths and mitigates their weaknesses.
Note: Teams should consider their industry, team size, and project focus when evaluating methodologies to ensure alignment with their operational needs.
Testing and Iterating on a Chosen Approach
Selecting a methodology is only the first step. Teams must test their chosen approach and refine it based on real-world results. This iterative process ensures the methodology delivers the desired outcomes and adapts to changing circumstances.
Effective test-and-learn strategies include:
Build-Measure-Learn Loop: Teams implement small changes, measure their impact, and use the insights to guide further improvements.
Minimum Viable Product (MVP): Launching a simplified version of a process allows teams to gather feedback and make data-driven adjustments.
Validated Learning: Teams rely on actual data rather than assumptions to refine their approach, ensuring alignment with organizational goals.
For example, a startup adopting Lean principles might begin by streamlining a single process, such as inventory management. By measuring the impact on efficiency and costs, the team can identify areas for further improvement. Research shows that 82% of businesses adopting Lean experience significant efficiency gains, highlighting the value of iterative testing.
Statistic | Description |
---|---|
Emphasizes the importance of validated learning to address market needs. | |
82% of businesses go lean | Demonstrates the efficiency improvements achieved through Lean principles. |
Testing and iterating also foster a culture of continuous improvement. Teams that regularly evaluate their processes can adapt to new challenges and seize opportunities for growth.
Tip: Teams should document their findings during each iteration to build a knowledge base that informs future decisions.
Seeking Expert Guidance or Training
Implementing a business process improvement methodology can feel overwhelming, especially for teams unfamiliar with the chosen approach. Seeking expert guidance or training ensures that teams gain the knowledge and skills needed to apply these methodologies effectively. Experts provide valuable insights, helping teams avoid common pitfalls and maximize the benefits of their improvement efforts.
Why Expert Guidance Matters
Experts bring years of experience and a deep understanding of various methodologies. They can tailor their advice to address the unique challenges faced by a team. For example, a consultant specializing in Lean Six Sigma can help a manufacturing team identify inefficiencies and implement data-driven solutions. Similarly, an Agile coach can guide a software development team in adopting iterative workflows that enhance flexibility and speed.
Tip: Teams should look for experts with a proven track record in their industry. This ensures that the guidance provided aligns with the team's specific needs and goals.
Types of Expert Support Available
Teams can access expert support in several ways, depending on their requirements and resources:
Workshops and Training Programs: These sessions provide hands-on learning opportunities. Teams can practice applying methodologies in a controlled environment before implementing them in real-world scenarios.
Consulting Services: Consultants work closely with teams to analyze processes, identify improvement areas, and develop customized solutions.
Online Courses and Certifications: Many organizations offer online training programs that allow team members to learn at their own pace. Certifications, such as Six Sigma Green Belt or Agile Scrum Master, validate their expertise.
Mentorship Programs: Experienced professionals mentor teams, offering ongoing support and advice as they navigate the implementation process.
Benefits of Training for Teams
Training equips teams with the tools and techniques needed to succeed. It fosters a deeper understanding of the chosen methodology, enabling team members to apply it confidently and effectively. Key benefits include:
Improved Skillsets: Training enhances team members' abilities, making them more capable of tackling complex challenges.
Increased Confidence: A well-trained team feels more prepared to implement changes and achieve desired outcomes.
Better Collaboration: Training programs often emphasize teamwork, helping members work together more effectively.
Sustainable Results: Teams with proper training are more likely to maintain improvements over time, ensuring long-term success.
How Systems and Teams Can Benefit
At Systems and Teams, clients have achieved remarkable results by leveraging expert guidance and training. For instance, teams that participated in Lean workshops reported significant reductions in waste and improved efficiency. Similarly, organizations that invested in Agile coaching experienced faster project delivery and enhanced customer satisfaction.
Note: Teams unsure about where to start can reach out to Systems and Teams for personalized recommendations. Our experts are ready to help teams identify the best training options and guide them through the implementation process.
Taking the Next Step
Teams interested in exploring expert guidance or training should begin by assessing their needs. Identifying skill gaps and areas for improvement helps determine the type of support required. Once these needs are clear, teams can research available options and select the most suitable programs or consultants.
Call to Action: Ready to take your team's performance to the next level? Contact Systems and Teams today to learn more about our expert training programs and consulting services. Let us help you achieve your business process improvement goals.
Benefits of Implementing the Right Methodology

Enhanced Efficiency and Productivity
Implementing the right business process improvement methodology significantly boosts efficiency and productivity. Teams can streamline workflows, eliminate unnecessary steps, and focus on high-value activities. For example, Lean Manufacturing emphasizes waste reduction, allowing organizations to optimize resource utilization. Similarly, Six Sigma uses data-driven techniques to minimize defects and improve output quality.
The impact of these methodologies is evident in real-world applications. Consider the following examples:
Organization | Methodology | Key Results |
---|---|---|
Toyota | Lean Manufacturing | Enhanced efficiency, improved customer satisfaction, and strengthened market position. |
Motorola | Six Sigma | 90% reduction in defects, substantial cost savings, and improved product quality. |
These results demonstrate how structured approaches can transform operations. Clients at Systems and Teams have experienced similar outcomes by adopting tailored methodologies. For instance, teams have reported faster project completion and reduced operational costs. Organizations seeking to achieve these benefits can explore expert guidance and training from Systems and Teams.
Tip: Teams should regularly monitor performance metrics to ensure continuous improvement and sustained productivity gains.
Improved Team Collaboration
The right methodology fosters better collaboration among team members. Approaches like Agile and Kaizen emphasize teamwork and open communication. Agile, for instance, encourages regular meetings where team members share updates and address challenges. Kaizen promotes a culture of continuous improvement, where every individual contributes ideas to enhance processes.
Improved collaboration leads to several advantages. Teams can resolve issues faster, align on goals, and maintain a shared sense of purpose. For example, a software development team using Agile might hold daily stand-ups to discuss progress and identify roadblocks. This practice ensures that everyone stays informed and works cohesively toward project objectives.
At Systems and Teams, clients have leveraged collaborative methodologies to strengthen team dynamics. By adopting these approaches, organizations have seen increased employee engagement and smoother workflows. Teams interested in enhancing collaboration can benefit from tailored training programs offered by Systems and Teams.
Note: Encouraging open communication and regular feedback helps teams build trust and work more effectively together.
Better Decision-Making and Problem-Solving
Effective methodologies enhance decision-making and problem-solving capabilities. Data-driven approaches like Six Sigma and Business Process Management (BPM) provide teams with actionable insights. These methodologies rely on metrics and analytics to identify inefficiencies and implement targeted solutions.
For example, Six Sigma uses tools like root cause analysis to address recurring issues. BPM enables teams to model and simulate workflows, predicting outcomes before making changes. These techniques empower teams to make informed decisions that drive measurable improvements.
Clients at Systems and Teams have successfully applied these methodologies to overcome complex challenges. By focusing on data and structured problem-solving, teams have achieved better outcomes and minimized risks. Organizations looking to improve their decision-making processes can explore expert support from Systems and Teams.
Callout: Teams should prioritize methodologies that align with their goals and provide the tools needed for effective problem-solving.
Long-Term Business Growth
Adopting the right business process improvement methodology lays the foundation for sustained growth. Teams that streamline operations and align processes with strategic goals often experience measurable improvements in key performance areas. Metrics such as efficiency, productivity, and customer satisfaction provide a clear picture of how these methodologies drive long-term success.
Organizations that focus on continuous optimization see significant benefits. Regular reviews of performance data help teams identify inefficiencies early, enabling them to make informed decisions. This proactive approach ensures that workflows remain effective even as market conditions evolve. For example, businesses that prioritize operational excellence often report enhanced lead conversion rates and higher average transaction values. These improvements not only boost revenue but also strengthen customer relationships.
Enhanced customer engagement plays a pivotal role in fostering growth. Teams that adopt methodologies like Lean or Agile often deliver better products and services, leading to higher satisfaction levels. Continuous improvement ensures that processes evolve to meet customer needs, creating a loyal client base. At Systems and Teams, clients have achieved remarkable results by implementing tailored methodologies. Many have reported better customer retention and increased market share, demonstrating the long-term impact of structured process improvements.
Operational excellence also cultivates a mindset of innovation. Teams that regularly refine their workflows develop a culture of problem-solving and creativity. This mindset drives improvements in products, processes, and services, ensuring that organizations remain competitive. Businesses that embrace this approach often outperform their peers, achieving sustained growth over time.
Tip: Teams should monitor key metrics, such as customer satisfaction and transaction values, to measure the effectiveness of their chosen methodology. Regular data reviews ensure that processes stay aligned with strategic goals.
Clients at Systems and Teams have leveraged these principles to achieve lasting success. By focusing on continuous improvement and aligning operations with long-term objectives, they have unlocked new opportunities for growth. Teams interested in replicating these results can explore expert guidance and training programs offered by Systems and Teams.
Call to Action: Ready to future-proof your business? Contact Systems and Teams today to learn how tailored methodologies can drive your long-term growth.
Selecting the right business process improvement methodology begins with understanding team-specific needs and aligning them with organizational goals. Companies that achieve this alignment often experience remarkable results:
Revenue growth increases 58% faster than unaligned counterparts.
Profitability improves by 72%, showcasing the financial impact of strategic alignment.
Leadership, strategy execution, and customer satisfaction also see significant enhancements.
Clients at Systems and Teams have witnessed similar transformations by adopting tailored methodologies. Teams that take a thoughtful, informed approach to process improvement unlock sustainable growth and operational excellence. To explore how Systems and Teams can guide your organization, contact us today.
FAQ
What is the first step in choosing a business process improvement methodology?
Teams should start by assessing their specific needs and goals. This involves analyzing current performance metrics, identifying pain points, and aligning objectives with organizational priorities. Clients at Systems and Teams often begin with a tailored consultation to ensure they select the most effective methodology.
How long does it take to implement a methodology?
The timeline varies depending on the methodology and team size. Simple approaches like Kanban may take days, while structured methods like Six Sigma could require months. Systems and Teams helps clients create realistic timelines based on their unique requirements.
Can small teams benefit from process improvement methodologies?
Yes, small teams can achieve significant results with methodologies like Agile or Kaizen. These approaches emphasize flexibility and incremental improvements. Systems and Teams has helped small teams streamline workflows and enhance productivity through tailored solutions.
Are these methodologies industry-specific?
While some methodologies align better with certain industries, most can adapt to various sectors. For example, Lean suits manufacturing, while Agile works well in software development. Systems and Teams provides expert guidance to match methodologies with industry needs.
How do teams measure the success of a methodology?
Teams track key performance indicators (KPIs) such as efficiency, cost savings, and customer satisfaction. Regular reviews ensure continuous improvement. Systems and Teams equips clients with tools to monitor progress and achieve measurable outcomes.
What if a chosen methodology doesn’t work?
Teams should test and iterate on their approach. Adjustments based on real-world results often lead to better outcomes. Systems and Teams supports clients in refining their strategies to ensure long-term success.
Do these methodologies require advanced technical skills?
Some methodologies, like Six Sigma, involve technical tools, while others, like Kaizen, focus on collaboration and simplicity. Systems and Teams offers training programs to help teams build the necessary skills for successful implementation.
How can Systems and Teams help with process improvement?
Systems and Teams provides expert guidance, training, and tailored solutions to help teams select and implement the right methodology. Clients benefit from proven strategies that drive efficiency, collaboration, and growth. Contact Systems and Teams today to learn more.