Mastering Six Sigma Process Mapping for Business Success
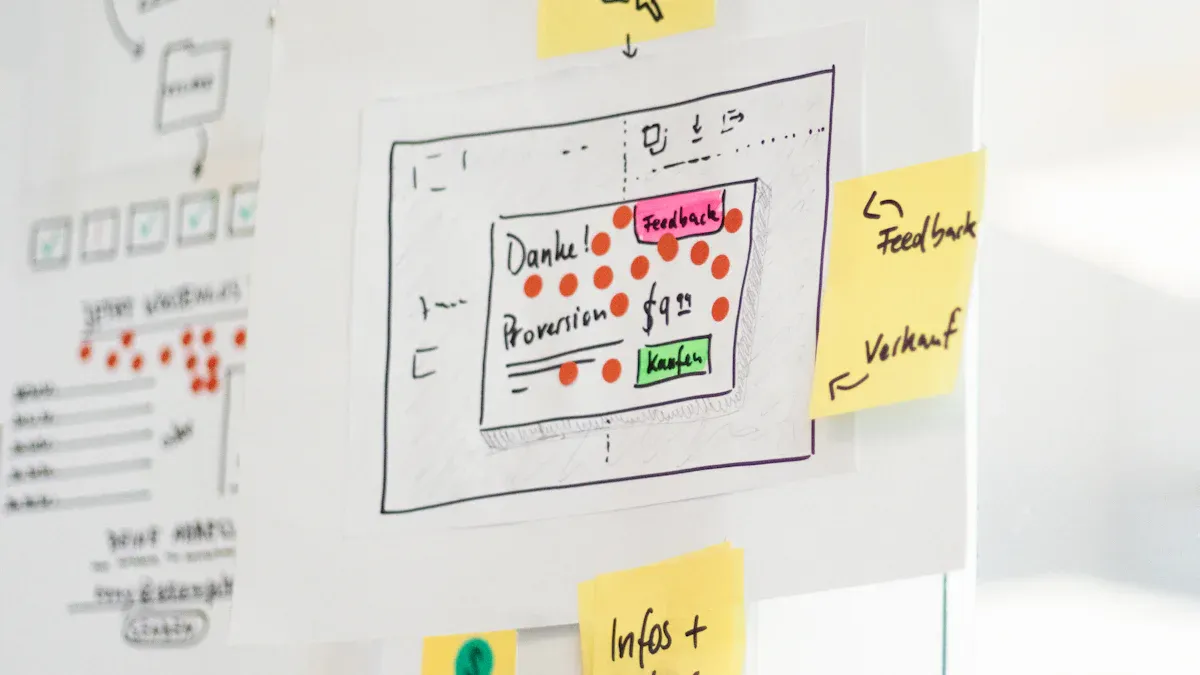
Six Sigma process mapping serves as a powerful tool for visualizing and refining business processes. It enables organizations to identify inefficiencies, streamline workflows, and align operations with strategic objectives. By reducing defects by up to 70% in the first year and cutting cycle times by 30-50%, businesses can achieve remarkable improvements in efficiency and quality. Companies have also reported cost savings of up to 5% of annual revenue and a 23% boost in customer satisfaction. Whether applied to hiring systems, sales, or broader business management, this methodology drives measurable success.
Key Takeaways
Six Sigma process mapping shows workflows clearly to find problems easily.
Fixing mistakes helps businesses work better and save money.
The DMAIC steps (Define, Measure, Analyze, Improve, Control) help improve processes step by step.
Updating process maps often keeps them accurate and useful.
Including the right people in mapping builds teamwork and better maps.
Using simple symbols in maps makes them easy to understand.
Clear and simple maps help teams find areas to improve.
Using data to make decisions ensures changes are smart and effective.
The Basics of Six Sigma Process Mapping
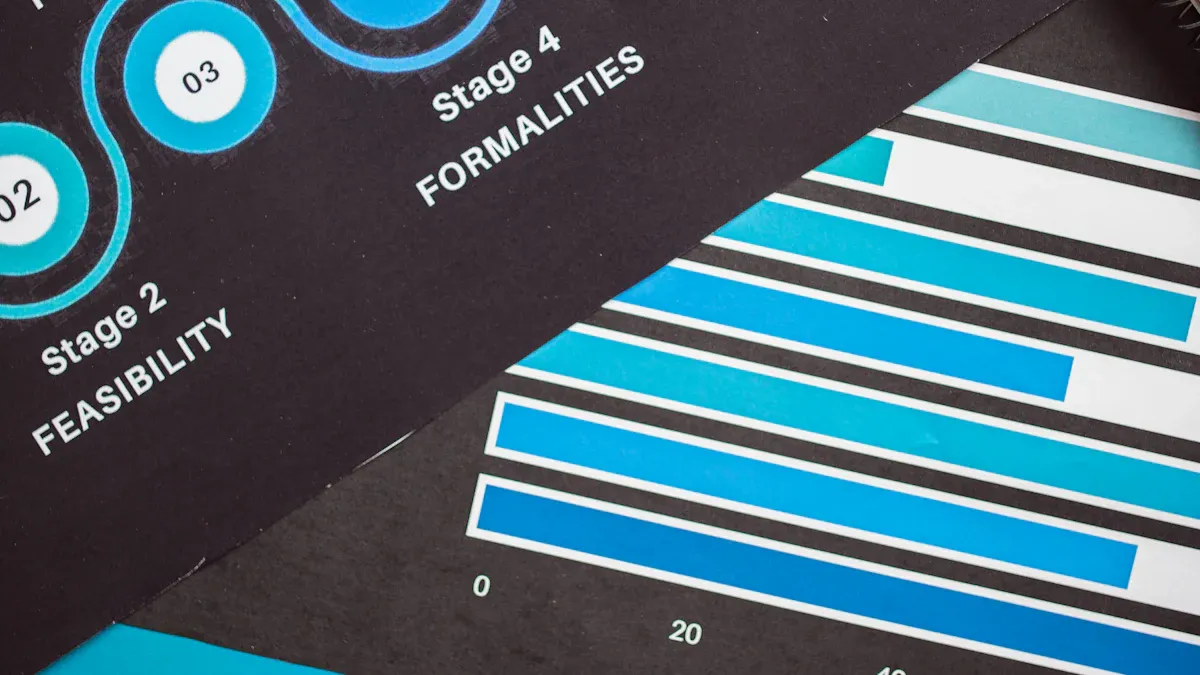
What is Six Sigma Process Mapping?
Six Sigma process mapping is a visual tool that helps organizations understand and improve their workflows. It provides a clear representation of each step in a process, highlighting inefficiencies and areas for improvement. By focusing on reducing defects and minimizing variability, this method ensures that processes consistently meet customer expectations. The concept of sigma levels, which measures a process's ability to produce defect-free outputs, is central to this approach. Higher sigma levels indicate fewer defects, validating the effectiveness of Six Sigma in achieving quality improvements.
Organizations like Motorola and General Electric have demonstrated the power of Six Sigma process mapping. Motorola, the originator of Six Sigma, significantly reduced production defects, while General Electric reported savings exceeding $2 billion through its implementation. These examples underscore the value of this methodology in driving measurable success.
How Process Mapping Fits into the Six Sigma Framework
Process mapping plays a critical role in the Six Sigma framework by providing a structured approach to identifying and eliminating inefficiencies. It integrates seamlessly with the DMAIC methodology, which stands for Define, Measure, Analyze, Improve, and Control. This framework emphasizes data-driven decision-making and sustained quality improvement, requiring commitment from all organizational levels, especially top management.
By visually representing workflows, process mapping facilitates communication among stakeholders and ensures alignment with strategic goals. It also serves as a foundation for documenting and standardizing processes, making it easier to train employees and implement future improvements. This structured approach empowers organizations to make informed decisions and achieve consistent results.
Overview of the DMAIC Methodology
The DMAIC methodology is a cornerstone of Six Sigma, guiding organizations through a systematic process improvement journey. Each phase focuses on specific objectives to ensure data-driven and measurable outcomes.
Define Phase
The Define phase establishes the scope and objectives of the project. Teams identify the problem, set goals, and outline the process to be improved. This phase ensures that everyone involved understands the project's purpose and expected outcomes.
Measure Phase
In the Measure phase, teams collect data to establish a baseline for the current process. Key performance indicators (KPIs) are identified to evaluate performance and track improvements. Accurate data collection is essential for identifying inefficiencies and areas for improvement.
Analyze Phase
The Analyze phase focuses on identifying the root causes of inefficiencies. Teams use statistical tools and techniques to examine the data collected in the previous phase. This analysis helps pinpoint the factors contributing to defects or variability in the process.
Improve Phase
During the Improve phase, teams develop and implement solutions to address the root causes identified in the Analyze phase. These solutions aim to optimize the process, reduce defects, and enhance overall efficiency. Testing and validation ensure that the improvements are effective.
Control Phase
The Control phase ensures that the improvements made during the Improve phase are sustained over time. Teams establish monitoring systems and standardize processes to prevent regression. This phase emphasizes the importance of maintaining the gains achieved through the DMAIC methodology.
The DMAIC framework has proven effective across industries, enabling businesses to analyze and enhance their processes. By following these steps, organizations can achieve meaningful operational changes and deliver consistent quality.
Benefits of Six Sigma Process Mapping for Business Success
Identifying and Eliminating Inefficiencies
Six Sigma Process Mapping enables organizations to pinpoint inefficiencies in their workflows. By visually representing each step, teams can identify bottlenecks, redundancies, and unnecessary delays. This clarity allows them to streamline operations and improve overall efficiency. For instance, analyzing process maps often reveals areas where resources are underutilized or tasks are duplicated.
The impact of eliminating inefficiencies can be measured through key metrics. These include cycle time, throughput, and first-pass yield. The table below highlights how these metrics improve when inefficiencies are addressed:
Metric | Description |
---|---|
Cycle Time | The total time required to complete a process from start to finish, including any delays. |
Throughput | The rate at which a process generates output over a given period. |
First-Pass Yield | The percentage of units that complete the process correctly on the first attempt. |
Cost per Unit | The total cost associated with producing a single unit of output. |
Customer Satisfaction | A measure that can indicate the effectiveness of processes and areas for improvement. |
By focusing on these metrics, organizations can achieve measurable improvements in productivity and quality.
Enhancing Communication and Collaboration
Process maps serve as a universal language for teams, fostering better communication and collaboration. They provide a clear and shared understanding of workflows, reducing misunderstandings and misalignments among stakeholders. Teams can use these visual tools to discuss processes, identify gaps, and prioritize improvements.
The benefits of improved communication and collaboration are evident in various outcomes. The table below outlines some key improvements:
Outcome | Description |
---|---|
Stakeholder Convergence | Enabled stakeholders to collaboratively discuss and understand systems for the first time. |
Acknowledgment of Gaps | Stakeholders recognized areas of misunderstanding in processes. |
Prioritization of Interventions | Allowed stakeholders to agree on and prioritize interventions to strengthen systems. |
Improved Coordination | Enhanced coordination among stakeholders in the process. |
Formalized Data-Sharing Agreements | Established more efficient use of services and formalized data-sharing agreements. |
These outcomes demonstrate how Six Sigma Process Mapping strengthens teamwork and ensures alignment across departments.
Supporting Data-Driven Decision Making
Six Sigma Process Mapping emphasizes the use of data to drive decisions. By collecting and analyzing process data, teams can identify root causes of inefficiencies and implement targeted solutions. This approach ensures that decisions are based on facts rather than assumptions.
In a manufacturing case, Six Sigma was used to analyze production data, revealing that 70% of defects originated from a specific machine. By replacing this machine, defects were reduced by 60%, showcasing the reliability of data-driven decisions.
Organizations like General Electric have successfully adopted this methodology. They analyzed extensive production data to enhance the quality and reliability of their jet engines. The DMAIC framework further supports this approach by ensuring that every decision is backed by accurate data and thorough analysis.
By leveraging data-driven insights, businesses can achieve continuous improvement and maintain a competitive edge.
Aligning Processes with Strategic Goals
Aligning business processes with strategic goals ensures that every activity contributes to the organization's overall vision. Six Sigma Process Mapping plays a pivotal role in achieving this alignment by providing a clear and structured view of workflows. It helps organizations identify gaps between current operations and desired outcomes, enabling them to make targeted improvements.
Process mapping fosters a culture of continuous improvement and innovation. By visualizing workflows, teams can uncover inefficiencies such as bottlenecks and redundancies. Standardizing procedures ensures consistency, which reduces errors and enhances reliability across departments. For example, a company that implemented process mapping reported a 10-30% increase in productivity. This improvement highlights the value of aligning processes with strategic objectives.
Organizations that prioritize process mapping initiatives often experience measurable benefits. Customer satisfaction scores, for instance, tend to rise by an average of 7%. This increase reflects the positive impact of streamlined processes on service quality and responsiveness. Improved communication also plays a significant role. Process maps enhance understanding among team members, fostering collaboration and ensuring that everyone works toward shared goals.
To align processes effectively, organizations must first define their strategic objectives. Clear goals provide a foundation for evaluating existing workflows and identifying areas for improvement. Teams can then use process maps to visualize how each step contributes to these objectives. This approach ensures that resources are allocated efficiently and that efforts remain focused on achieving the desired outcomes.
In addition to improving internal operations, aligning processes with strategic goals strengthens an organization's competitive position. Companies that consistently deliver high-quality products and services gain a reputation for reliability, which attracts and retains customers. By leveraging process mapping techniques, businesses can maintain this standard while adapting to changing market demands.
The benefits of aligning processes with strategic goals extend beyond operational efficiency. They include enhanced customer satisfaction, improved team collaboration, and a stronger focus on innovation. Organizations that embrace this approach position themselves for long-term success in an increasingly competitive landscape.
Types of Six Sigma Process Maps
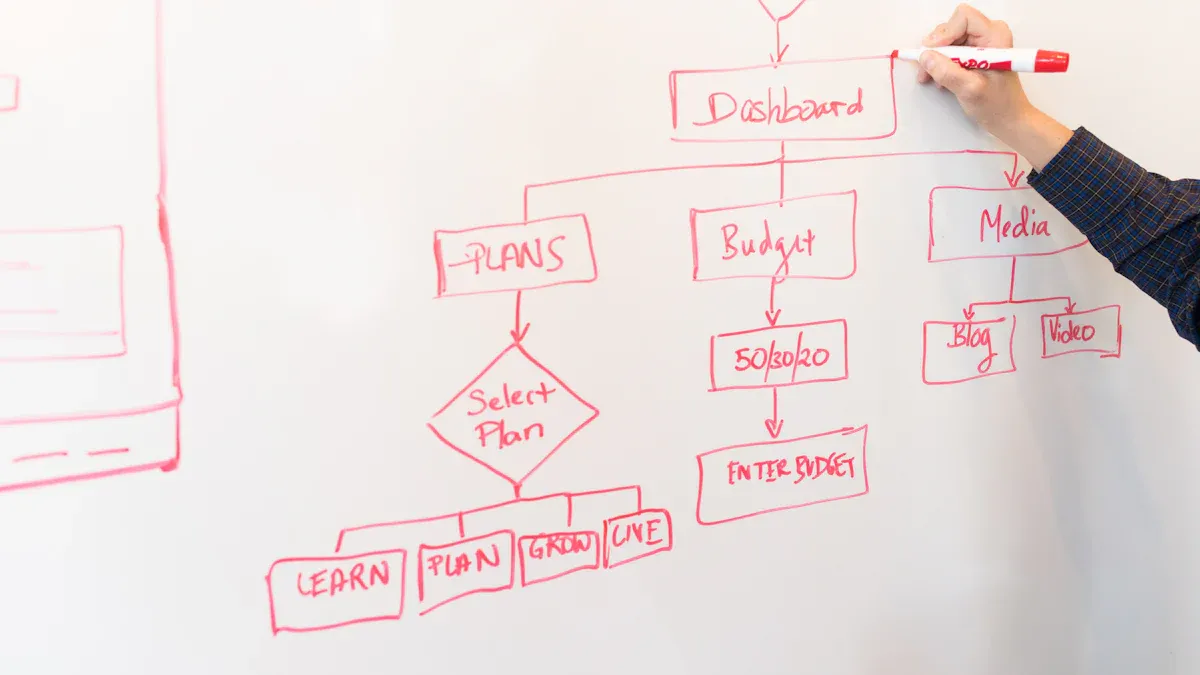
SIPOC Diagram
The SIPOC diagram is a foundational tool in Six Sigma Process Mapping. It provides a high-level overview of a process by identifying five key elements: Suppliers, Inputs, Process, Outputs, and Customers. This type of map is particularly useful for defining the boundaries of a process and ensuring alignment with customer needs. By focusing on these elements, teams can gain a clear understanding of how inputs flow through a process to deliver outputs that meet customer expectations.
SIPOC diagrams are widely used across industries to improve processes. For example, in healthcare, implementing SIPOC diagrams has led to a 30% reduction in undetected dispensing errors and a 20% decrease in hospital-acquired infections. Similarly, the hospitality industry has reported improved guest experiences and higher satisfaction ratings. These outcomes highlight the versatility and effectiveness of SIPOC diagrams in driving process improvements.
Industry | Quantitative Outcome |
---|---|
Healthcare | 30% reduction in undetected dispensing errors |
20% decrease in hospital-acquired infections | |
Hospitality | Improved guest experiences and higher satisfaction ratings |
Education | Improved communication and reduced administrative burdens |
Banking | Reduced turnaround times and enhanced customer satisfaction |
High-Level Process Maps
High-level process maps provide a simplified view of a process, focusing on major steps rather than intricate details. These maps are ideal for identifying overarching workflows and aligning them with strategic goals. By offering a bird’s-eye view, high-level maps help organizations pinpoint areas for improvement without overwhelming teams with excessive information.
The effectiveness of high-level process maps can be measured through impact and outcome metrics. For instance, businesses can track metrics such as increasing user conversion rates by 20% within three months or improving customer effort scores by a defined amount within a quarter. These metrics validate the usability of high-level maps in achieving business success.
Impact Metrics:
Closing a set number of enterprise contracts within a year.
Outcome Metrics:
Improving customer effort scores by a defined amount by the end of a quarter.
Increasing the number of weekly active users by a specific target by year-end.
Swimlane Diagrams
Swimlane diagrams excel in clarifying workflows, especially in cross-functional teams. They visually segment processes into lanes, each representing a specific department, role, or stakeholder. This layout ensures clear accountability and highlights interactions between different actors. Teams can use swimlane diagrams to identify bottlenecks, streamline hand-offs, and enhance overall efficiency.
Research demonstrates the effectiveness of swimlane diagrams in improving communication and collaboration. For example, they provide visual clarity by distinguishing responsibilities across stakeholders. This clarity reduces misunderstandings and fosters better teamwork. Additionally, swimlane diagrams help teams identify bottlenecks, enabling them to resolve inefficiencies and optimize workflows.
Evidence Point | Description |
---|---|
Visual Clarity | Swimlane diagrams clarify workflows by visually representing distinct processes and responsibilities. |
Enhanced Communication | They facilitate interdisciplinary collaboration, improving team communication and reducing misunderstandings. |
Identification of Bottlenecks | Swimlanes help teams spot and resolve bottlenecks, enhancing overall efficiency. |
By leveraging these types of process maps, organizations can address unique challenges and achieve their operational goals effectively.
Value Stream Mapping
Value Stream Mapping (VSM) is a critical tool within Six Sigma Process Mapping. It provides a detailed visual representation of the steps involved in delivering a product or service. By mapping out the entire process, organizations can identify inefficiencies, reduce waste, and improve overall flow. This approach ensures that every step adds value to the customer while eliminating non-value-adding activities.
VSM focuses on identifying and classifying different types of waste. These include overproduction, waiting times, unnecessary transportation, and excess inventory. By addressing these issues, businesses can reduce costs and enhance efficiency. For example, a manufacturing company might use VSM to pinpoint bottlenecks in its production line, enabling it to streamline operations and improve throughput.
VSM plays a pivotal role in aligning processes with customer needs. It reduces lead times and increases responsiveness, ensuring that businesses can meet customer expectations more effectively. This alignment fosters a culture of continuous improvement, where teams regularly assess and refine their workflows.
One of the key benefits of VSM is its ability to prioritize improvement efforts. By visualizing the entire process, teams can focus on the most significant areas for enhancement. For instance, if a particular step consistently causes delays, it becomes a priority for optimization. This targeted approach ensures that resources are allocated efficiently, leading to measurable improvements in performance.
VSM also supports data-driven decision-making. It facilitates the collection and analysis of process data, enabling teams to make informed choices about where to implement changes. For example, a retail company might use VSM to analyze its supply chain, identifying opportunities to reduce delivery times and improve inventory management.
Organizations often use VSM iteratively to assess the impact of improvements. This iterative process helps foster a culture of ongoing enhancement, where teams continuously seek ways to optimize their workflows. By regularly updating their value stream maps, businesses can adapt to changing market demands and maintain a competitive edge.
How to Create a Six Sigma Process Map
Step 1: Define the Scope and Objectives
Defining the scope and objectives is the foundation of creating an effective Six Sigma process map. This step ensures clarity about what the process map will cover and its intended outcomes. Teams must identify the boundaries of the process, including where it starts and ends. A well-defined scope prevents unnecessary complexity and keeps the focus on critical areas.
Clearly outlining objectives helps stakeholders understand the purpose of the process map. For example, the goal might be to reduce cycle time, improve quality, or eliminate bottlenecks. Standardized process maps allow stakeholders to anticipate potential challenges and make informed decisions early in the process. They also provide a shared understanding of the workflow, which fosters collaboration.
Tip: Use flowcharts to visualize the scope and boundaries. This approach simplifies the identification of individual steps, actions, and decision points.
Step 2: Identify Key Process Steps
Identifying key process steps is crucial for creating a comprehensive process map. Teams should focus on capturing all major activities, decision points, and interactions within the workflow. This step requires clean data collection to ensure accuracy. Each step must be examined to understand its purpose and contribution to the overall process.
Process analytics plays a vital role in this phase. By analyzing each step, organizations can eliminate redundancies and improve efficiency. For instance, a manufacturing company might discover that a specific step adds no value to the final product. Removing such steps streamlines the process and enhances productivity.
Note: Continually monitor process improvement efforts to maintain focus and effectiveness. Measuring the impact of these efforts ensures that performance metrics are utilized effectively.
Step 3: Sequence the Steps
Sequencing the steps involves arranging the identified activities in the correct order. This step ensures that the process flows logically and efficiently. Teams should consider dependencies between steps and identify any potential bottlenecks. A clear sequence helps in visualizing the workflow and identifying areas for improvement.
A well-sequenced process map highlights strengths and weaknesses, making it easier to implement changes. For example, if a step consistently causes delays, it can be prioritized for optimization. Visual representation aids in understanding and decision-making, ensuring that all stakeholders are aligned.
Description | |
---|---|
Inputs, Outputs, and Steps | Major components of a process map that illustrate the workflow and interactions within the organization. |
Visual Representation | Graphical representation aids in understanding and decision-making, highlighting strengths and weaknesses. |
Improvement Facilitation | Helps identify bottlenecks and areas needing change, enhancing efficiency and effectiveness. |
Tracking Improvements | Serves as a measurement tool to audit and understand different areas of the process. |
Enhanced Training | Visual aids are more effective for training, leading to quicker understanding. |
Change Management Guidance | Provides a detailed outlook of the current process, aiding in effective change management. |
By following these steps, organizations can create a Six Sigma process map that drives meaningful improvements and aligns with strategic goals.
Step 4: Review and Validate the Process Map
Reviewing and validating the process map ensures its accuracy and effectiveness. This step involves examining the map for errors, inconsistencies, or missing details. Teams should gather feedback from stakeholders and compare the map against project data to confirm its alignment with real-world operations. Validation helps refine the map, making it a reliable tool for process improvement.
Key benefits of reviewing and validating process maps include:
Identifying repetitions, redundancies, and bottlenecks, which allows for targeted corrections.
Encouraging stakeholder involvement by soliciting feedback, enhancing collaboration and quality assurance.
Gaining new perspectives that may have been overlooked during the initial mapping, leading to continuous improvement.
Tip: Use workshops or collaborative sessions to involve stakeholders in the review process. This approach fosters engagement and ensures the map reflects diverse insights.
Step 5: Analyze the Process for Improvements
Analyzing the process map is critical for identifying areas that need enhancement. Teams should focus on pinpointing inefficiencies, bottlenecks, and non-value-adding activities. This analysis provides a foundation for implementing targeted changes that improve overall performance.
Metrics play a vital role in assessing the effectiveness of process improvements. The table below highlights key metrics that organizations can use to evaluate their processes:
Metric Type | Description |
---|---|
Effectiveness metrics | Measure the ability of a process to achieve its intended results, focusing on quality and outcomes. |
Customer satisfaction (CSAT) | Indicates how well a product or service meets customer expectations; higher scores suggest effectiveness. |
Error rate | Measures the number of errors in a process; a lower rate indicates a more effective process. |
Quality rate | Proportion of output meeting quality standards; a higher rate suggests effectiveness. |
Continuous improvement metrics | Assess the impact of changes made to processes, quantifying benefits like cost savings and efficiency. |
Cost | Measures cost efficiency from process improvements; effective savings indicate better performance. |
Improvement in cycle time | Measures decrease in cycle time post-improvements; larger decreases indicate more effective changes. |
Reduction in error rate | Measures decrease in error rate after improvements; larger reductions indicate effective changes. |
By leveraging these metrics, teams can measure the success of their improvements and ensure alignment with organizational goals.
Step 6: Implement Changes and Monitor Results
Implementing changes based on the analysis is the next step. Teams should prioritize solutions that address the most critical inefficiencies. Pilot testing these changes on a smaller scale can help validate their effectiveness before full implementation. This approach minimizes risks and ensures a smoother transition.
Monitoring results is equally important. Teams should track key performance indicators (KPIs) to measure the impact of the changes. Regular monitoring helps identify any deviations from expected outcomes, allowing for timely adjustments. For example, if a change reduces cycle time but increases error rates, further refinements may be necessary.
Note: Continuous monitoring fosters a culture of ongoing improvement. It ensures that processes remain efficient and aligned with strategic objectives over time.
By following these steps, organizations can maximize the benefits of Six Sigma Process Mapping and achieve sustainable improvements in their workflows.
Overcoming Challenges in Six Sigma Process Mapping
Addressing Lack of Clarity in Process Steps
A lack of clarity in process steps often hinders the effectiveness of Six Sigma Process Mapping. Ambiguities can arise when teams fail to define roles, responsibilities, or the sequence of activities. To address this, organizations should adopt structured problem-solving techniques that uncover the root causes of unclear steps.
Brainstorming sessions encourage diverse perspectives, helping teams identify hidden issues.
Fishbone diagrams categorize potential causes, making it easier to pinpoint specific problems.
The 5 Whys technique uses iterative questioning to trace issues back to their origins.
Pareto analysis prioritizes the most significant factors, ensuring efforts focus on impactful changes.
Stakeholder mapping highlights overlooked root causes by engaging key participants.
Collaborative problem-solving fosters innovation and ensures all voices are heard.
By combining these approaches, teams can create process maps that are both accurate and actionable. Clear steps improve communication, reduce errors, and ensure alignment with organizational goals.
Managing Resistance to Change
Resistance to change remains a significant barrier to the successful adoption of process mapping methods. Employees often feel overwhelmed by new initiatives, with surveys showing that 53% of workers struggle to adapt to change. Additionally, 70% of change initiatives fail due to a lack of cooperation from the workforce.
To overcome this challenge, organizations must prioritize effective change management strategies. Transparent communication is essential. Leaders should explain the benefits of process mapping and how it aligns with the company’s objectives. Training programs can equip employees with the skills needed to adapt to new workflows. Recognizing and addressing employee concerns fosters trust and reduces resistance.
Involving employees in the mapping process also enhances buy-in. When workers contribute to designing workflows, they feel a sense of ownership, making them more likely to embrace changes. By addressing resistance proactively, organizations can ensure smoother transitions and greater success in implementing Six Sigma methodologies.
Avoiding Overcomplication in Process Maps
Overcomplicated process maps can confuse teams and hinder decision-making. Including excessive details or using complex symbols often leads to misunderstandings. Simplicity is key to creating effective maps that everyone can understand.
To maintain clarity:
Use simple language and avoid jargon.
Limit the number of symbols and colors to prevent visual clutter.
Accurately represent each step, focusing only on essential tasks, decisions, and outcomes.
Clear and straightforward maps improve communication and collaboration. They also make it easier to identify inefficiencies and implement improvements. For example, a well-designed map highlights bottlenecks without overwhelming users with unnecessary information. By prioritizing simplicity, organizations can create tools that drive meaningful change and support continuous improvement.
Ensuring Stakeholder Buy-In
Stakeholder buy-in plays a critical role in the success of Six Sigma process mapping. When stakeholders actively support and engage with the initiative, organizations experience smoother implementation and better outcomes. Without their involvement, even the most well-designed process maps may face resistance or fail to deliver the desired results.
To secure stakeholder buy-in, organizations must first identify the key individuals or groups impacted by the process. These stakeholders often include employees, managers, and external partners. Engaging them early in the process fosters a sense of ownership and ensures their concerns are addressed. Teams can achieve this by organizing workshops, conducting surveys, or holding one-on-one discussions to gather input and feedback.
Sufficient stakeholder buy-in from the right stakeholders (and as many stakeholders as possible) can increase the likelihood of a successful project. It can mean fewer delays, greater overall approval, increased cooperation, and other benefits that contribute to your success.
Clear communication is another essential factor. Stakeholders need to understand the purpose of process mapping and how it aligns with organizational goals. Explaining the benefits, such as improved efficiency and reduced costs, helps build trust and enthusiasm. Visual aids like charts or simplified process maps can make complex ideas more accessible, ensuring everyone stays informed.
Involving stakeholders in the mapping process strengthens their commitment. When individuals contribute to designing workflows, they feel valued and more likely to support the changes. For example, assigning roles in process mapping sessions allows stakeholders to share their expertise and identify potential challenges. This collaborative approach not only improves the quality of the process map but also fosters a culture of teamwork.
Recognition and transparency further enhance stakeholder buy-in. Acknowledging contributions and celebrating milestones motivate individuals to stay engaged. Regular updates on progress and results keep stakeholders informed and reinforce their confidence in the initiative. For instance, sharing metrics that demonstrate improvements, such as reduced cycle times or increased customer satisfaction, highlights the value of their involvement.
Organizations that prioritize stakeholder buy-in often achieve better results. They experience fewer delays, greater cooperation, and higher approval rates for their initiatives. By fostering collaboration, maintaining open communication, and recognizing contributions, businesses can ensure the successful implementation of Six Sigma process mapping.
Best Practices for Effective Six Sigma Process Mapping
Involve the Right Stakeholders
Involving the right stakeholders is essential for creating effective process maps. Stakeholders bring diverse perspectives and expertise, which enrich the mapping process and ensure its relevance to organizational goals. Identifying key individuals based on their roles and responsibilities is the first step. For example, team leaders, process owners, and employees directly involved in the workflow should participate.
Engaging stakeholders throughout the process fosters collaboration and ensures alignment. Conducting interviews or workshops allows teams to gather valuable insights and feedback. This approach not only improves the accuracy of the process map but also builds a sense of ownership among participants. The table below outlines a systematic approach to stakeholder involvement:
Step | Description |
---|---|
1 | Identify relevant stakeholders based on their roles and expertise. |
2 | Conduct interviews to gather diverse perspectives, enriching the mapping process. |
3 | Actively involve stakeholders throughout the entire process, soliciting their feedback and insights at each stage. |
By following these steps, organizations can create process maps that reflect real-world operations and drive meaningful improvements.
Use Clear and Consistent Symbols
Using clear and consistent symbols in process maps ensures clarity and minimizes misunderstandings. Standardized symbols make it easier for stakeholders to interpret workflows, enhancing communication and collaboration. For instance, using universally recognized shapes for actions, decisions, and inputs ensures that everyone understands the process map, regardless of their background.
Clear symbols also improve documentation accuracy, which is critical for process optimization. Teams can identify inefficiencies and refine workflows more effectively when the map is easy to read. The table below highlights the importance of using consistent symbols:
Evidence Description | Importance |
---|---|
Minimizes misunderstandings among stakeholders | |
Improves documentation accuracy | Ensures precise representation of workflows |
Supports process optimization | Facilitates better analysis and integration of processes |
Organizations should establish guidelines for symbol usage to maintain consistency across all process maps. This practice not only enhances understanding but also ensures that maps remain a reliable tool for decision-making.
Focus on Simplicity and Clarity
Simplicity and clarity are the cornerstones of effective process mapping. Overcomplicated maps can confuse stakeholders and hinder decision-making. A clear and straightforward map highlights the essential steps, decisions, and outcomes without overwhelming users with unnecessary details.
To achieve simplicity, teams should focus on the primary objectives of the process map. Avoiding excessive jargon and limiting the number of symbols and colors can prevent visual clutter. For example, a process map designed to reduce cycle time should emphasize key bottlenecks and improvement opportunities rather than every minor detail.
Clarity also aids in identifying inefficiencies and implementing changes. A well-designed map ensures that all stakeholders, from team members to executives, can easily understand the workflow. This shared understanding fosters collaboration and supports continuous improvement. By prioritizing simplicity and clarity, organizations can create process maps that effectively guide their efforts toward achieving strategic goals.
Regularly Update and Review Process Maps
Regular updates and reviews of process maps ensure their relevance and effectiveness. Business processes evolve over time due to changes in technology, market demands, or organizational goals. Outdated maps can lead to inefficiencies, miscommunication, and missed opportunities for improvement. By reviewing process maps regularly, organizations can maintain alignment with their strategic objectives and adapt to new challenges.
Why Regular Updates Matter
Processes rarely remain static. Teams may introduce new tools, adjust workflows, or face external changes like regulatory updates. Without regular updates, process maps lose their accuracy and fail to reflect the current state of operations. This can result in confusion among team members and hinder decision-making.
Tip: Schedule periodic reviews—quarterly or semi-annually—to ensure process maps stay up-to-date.
Steps to Review and Update Process Maps
Gather Feedback from Stakeholders
Engage team members who interact with the process daily. Their insights can reveal inefficiencies, bottlenecks, or steps that no longer add value.Example: A customer service team might highlight delays caused by outdated software, prompting updates to the process map.
Compare the Map to Current Operations
Conduct a side-by-side comparison of the process map and actual workflows. Identify discrepancies and determine whether they result from changes in procedures or errors in documentation.Analyze Performance Metrics
Use data to evaluate the process's effectiveness. Metrics like cycle time, error rates, or customer satisfaction scores can indicate areas needing improvement.Metric
Purpose
Cycle Time
Measures the time taken to complete a process.
Error Rate
Tracks the frequency of mistakes.
Customer Satisfaction
Reflects the quality of outcomes.
Update the Map with New Information
Incorporate changes based on feedback and analysis. Ensure the updated map uses clear symbols and maintains simplicity for easy understanding.Communicate Changes to the Team
Share the revised map with all stakeholders. Provide training if necessary to ensure everyone understands the updated workflow.
Benefits of Regular Reviews
Regular reviews improve efficiency, reduce errors, and enhance collaboration. Teams gain a clearer understanding of their roles, leading to better coordination. Updated maps also support continuous improvement by identifying opportunities for optimization.
Reminder: Treat process maps as living documents. Regular updates keep them relevant and valuable tools for achieving business success.
By committing to regular updates and reviews, organizations can ensure their process maps remain accurate, actionable, and aligned with their goals. This practice fosters adaptability and positions businesses for long-term success.
Six Sigma Process Mapping remains a vital tool for driving business success. It empowers organizations to visualize workflows, identify inefficiencies, and implement targeted improvements. By enhancing efficiency, quality, and collaboration, it supports teams in achieving measurable results. Systems and teams that adopt this methodology often experience streamlined operations and improved customer satisfaction. Applying the outlined steps and best practices ensures that businesses can unlock the full potential of process mapping. For further guidance, readers are encouraged to explore how this approach can transform their operations.
FAQ
What is the primary purpose of Six Sigma Process Mapping?
Six Sigma Process Mapping helps organizations visualize workflows to identify inefficiencies and improve processes. It ensures that every step adds value, aligns with strategic goals, and meets customer expectations.
How does Six Sigma Process Mapping differ from traditional process mapping?
Six Sigma Process Mapping integrates data-driven analysis and focuses on reducing defects and variability. Unlike traditional mapping, it aligns processes with measurable goals and emphasizes continuous improvement through the DMAIC framework.
Who should be involved in creating a process map?
Key stakeholders, including process owners, team members, and decision-makers, should participate. Their insights ensure the map accurately reflects real-world workflows and identifies improvement opportunities.
Can Six Sigma Process Mapping be applied to small businesses?
Yes, Six Sigma Process Mapping benefits businesses of all sizes. Small businesses can use it to streamline operations, reduce costs, and improve customer satisfaction without requiring extensive resources.
How often should process maps be updated?
Organizations should review and update process maps regularly, such as quarterly or semi-annually. Updates ensure maps reflect current workflows and remain effective in addressing inefficiencies.
What tools are commonly used for creating process maps?
Popular tools include Microsoft Visio, Lucidchart, and Miro. These platforms offer user-friendly interfaces and templates for designing clear and professional process maps.
How does process mapping improve customer satisfaction?
By identifying and eliminating inefficiencies, process mapping ensures faster delivery, higher quality, and better service. These improvements directly enhance the customer experience and satisfaction.
Is training required to implement Six Sigma Process Mapping?
Basic training in Six Sigma principles and tools is recommended. It equips teams with the knowledge to create accurate maps, analyze data, and implement improvements effectively.