Master Business Process Improvement Methodologies Easily
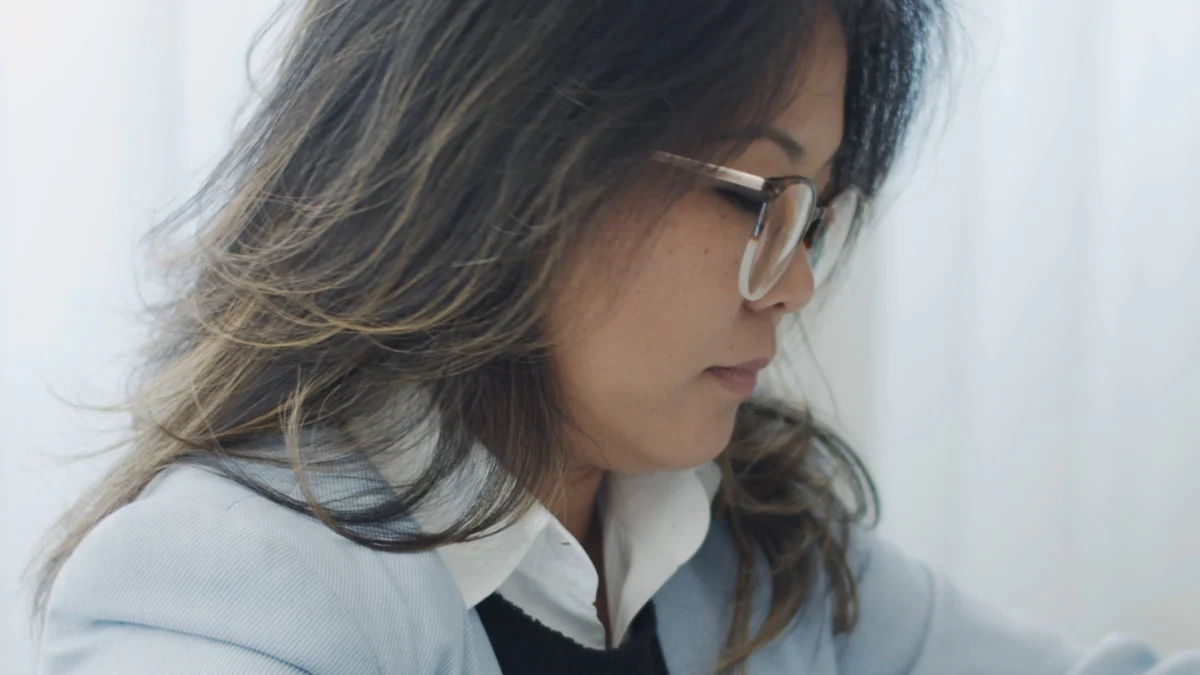
Business Process Improvement Methodologies offer structured systems to enhance efficiency and effectiveness in organizations. These methodologies aim to streamline operations, reduce waste, and improve productivity. By implementing these systems, businesses can achieve significant benefits such as reduced production times, lower defect rates, and increased customer satisfaction. This methodology provides a framework for identifying inefficiencies and implementing solutions, ultimately leading to cost savings and enhanced reliability. Companies that adopt these methodologies often see improvements in their business management practices, resulting in more consistent and accurate outcomes.
Understanding Business Process Improvement
What Are Business Process Improvement Methodologies?
Business Process Improvement Methodologies provide structured approaches to enhance the efficiency and effectiveness of organizational operations. These methodologies focus on analyzing existing processes, identifying inefficiencies, and implementing solutions to optimize performance. By employing these methodologies, businesses can streamline operations, reduce waste, and improve productivity. This systematic approach not only enhances operational efficiency but also leads to higher quality products and increased customer satisfaction.
Expert Testimony:
"Together, these methodologies create a powerful process improvement tool by combining Lean’s waste reduction and workflow optimization strategies with Six Sigma’s focus on quality and precision."
The integration of different methodologies, such as Lean and Six Sigma, results in more efficient operations. This combination allows businesses to achieve significant improvements in their competitiveness and operational performance.
Why Are They Important for Businesses?
Business Process Improvement Methodologies play a crucial role in helping organizations adapt, excel, and lead in their respective industries. By scrutinizing and refining existing processes, businesses can reduce waste and optimize resource use. This leads to streamlined operations, faster production cycles, and improved responsiveness to market demands.
Expert Testimony:
"Process improvement stands out as a cornerstone strategy, enabling organizations to adapt, excel, and lead in their respective industries."
Moreover, these methodologies foster a culture of continuous reevaluation and adaptation to emerging challenges. They encourage constant training and development, making jobs easier and more satisfying for employees. This sense of ownership and engagement among the workforce contributes to the overall success of the organization.
Key Methodologies for Business Process Improvement
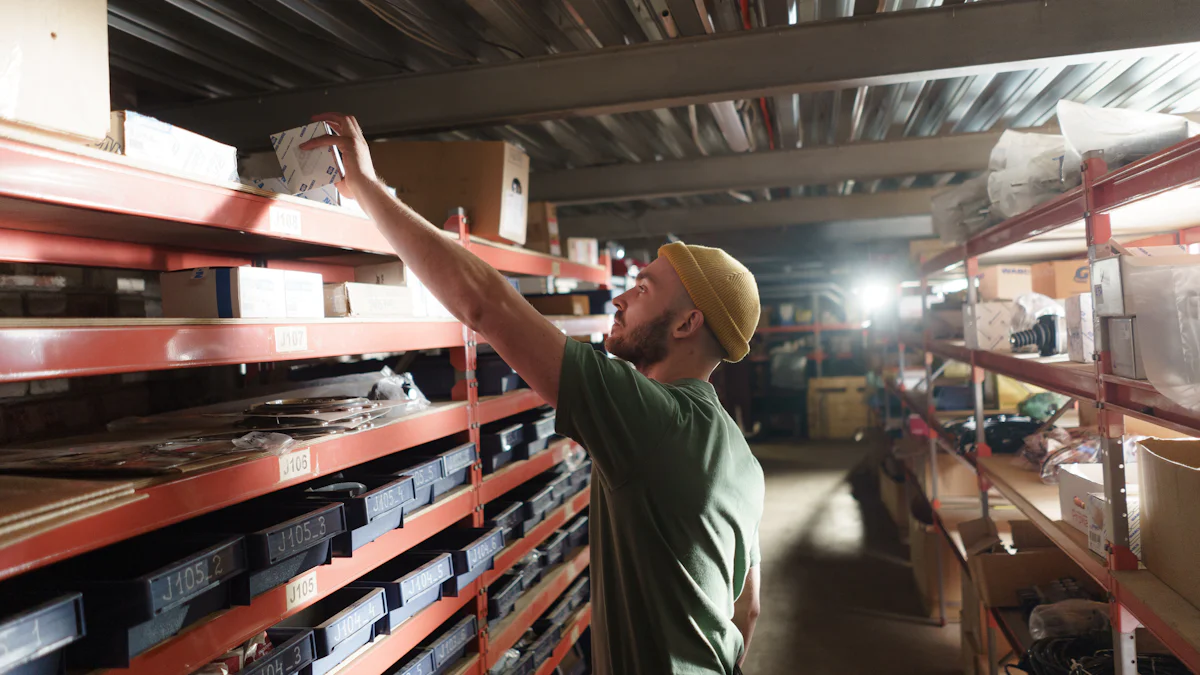
Lean Methodology
Principles of Lean
Lean methodology focuses on eliminating waste and optimizing processes to enhance efficiency. It originated in the manufacturing sector but has since been adopted across various industries. The core principles of Lean include:
Value Identification: Understanding what the customer values and ensuring that all activities contribute to delivering this value.
Value Stream Mapping: Analyzing the flow of materials and information to identify and eliminate waste.
Flow Optimization: Ensuring that processes run smoothly without interruptions or delays.
Pull System Implementation: Producing only what is needed when it is needed, reducing excess inventory.
Continuous Improvement (Kaizen): Encouraging ongoing efforts to improve processes and eliminate waste.
Applications of Lean in Business
Businesses apply Lean methodology to streamline operations and improve productivity. For example, manufacturing companies use Lean to reduce production times and minimize defects. Service industries implement Lean to enhance customer service by reducing wait times and improving process efficiency. By focusing on value and eliminating waste, organizations can achieve significant improvements in their operational performance.
Six Sigma Methodology
Principles of Six Sigma
Six Sigma is a data-driven approach that aims to reduce defects and improve quality in business processes. Its principles include:
Define: Identifying the problem and setting goals.
Measure: Collecting data to understand current performance.
Analyze: Identifying root causes of defects.
Improve: Implementing solutions to address root causes.
Control: Monitoring processes to ensure sustained improvements.
Applications of Six Sigma in Business
Businesses use Six Sigma to enhance quality and efficiency. Manufacturing firms apply Six Sigma to reduce defects and improve product quality. Service organizations use it to optimize processes and enhance customer satisfaction. By focusing on data-driven decision-making, Six Sigma helps businesses achieve consistent and reliable outcomes.
Agile Methodology
Principles of Agile
Agile methodology emphasizes adaptability and responsiveness. It is particularly useful in dynamic environments where requirements change frequently. The principles of Agile include:
Customer Collaboration: Engaging with customers to understand their needs and preferences.
Iterative Development: Delivering work in small, manageable increments.
Flexibility: Adapting to changes quickly and efficiently.
Continuous Feedback: Gathering feedback regularly to improve processes and products.
Applications of Agile in Business
Agile methodology is widely used in software development and project management. Teams use Agile to deliver projects more efficiently by breaking them into smaller tasks and iterating based on feedback. This approach allows businesses to respond quickly to market changes and customer demands, enhancing their competitiveness and innovation.
Kaizen Methodology
Principles of Kaizen
Kaizen, a Japanese term meaning "continuous improvement," focuses on small, incremental changes to enhance processes. This methodology emphasizes the involvement of all employees, from top management to frontline workers, in identifying areas for improvement. The core principles of Kaizen include:
Continuous Improvement: Encouraging ongoing efforts to improve processes and eliminate inefficiencies.
Employee Involvement: Engaging all employees in the improvement process, fostering a sense of ownership and accountability.
Standardization: Establishing best practices and standard procedures to ensure consistency and quality.
Customer Focus: Prioritizing customer needs and ensuring that improvements align with delivering value to customers.
Applications of Kaizen in Business
Businesses apply Kaizen to foster a culture of continuous improvement and innovation. Manufacturing companies use Kaizen to enhance production efficiency and reduce waste. Service industries implement Kaizen to improve customer service and streamline operations. By involving employees at all levels, organizations can identify and address inefficiencies, leading to improved productivity and customer satisfaction.
Total Quality Management (TQM)
Principles of TQM
Total Quality Management (TQM) is a comprehensive approach that seeks to improve quality and performance across all organizational processes. The principles of TQM include:
Customer Focus: Understanding and meeting customer needs and expectations.
Total Employee Involvement: Engaging all employees in quality improvement efforts.
Process Approach: Viewing activities as processes that can be measured and improved.
Integrated System: Aligning all organizational processes with quality objectives.
Continuous Improvement: Committing to ongoing enhancement of processes and products.
Applications of TQM in Business
Businesses implement TQM to achieve higher quality standards and enhance customer satisfaction. Manufacturing firms use TQM to improve product quality and reduce defects. Service organizations apply TQM to optimize service delivery and enhance customer experiences. By focusing on quality and continuous improvement, TQM helps businesses achieve consistent and reliable outcomes.
Choosing the Right Methodology
Selecting the appropriate methodology for business process improvement requires careful consideration. Each methodology offers unique strengths and applications, making it essential to align them with specific business needs and scenarios.
Factors to Consider
When choosing a methodology, businesses should evaluate several key factors:
Nature of the Business: Different industries have varying requirements. For instance, manufacturing companies may benefit more from Lean methodologies due to their focus on waste reduction and efficiency. In contrast, service-oriented businesses might find Agile methodologies more suitable because of their emphasis on flexibility and customer collaboration.
Organizational Goals: Clearly defined objectives help in selecting the right approach. If the goal is to enhance product quality, Six Sigma's data-driven focus on reducing defects might be ideal. For continuous improvement and employee involvement, Kaizen could be the best fit.
Resource Availability: Implementing certain methodologies requires specific resources, including time, personnel, and technology. Businesses must assess their capacity to support the chosen methodology effectively.
Cultural Fit: The organization's culture plays a significant role in the success of any methodology. For example, Kaizen thrives in environments that encourage employee participation and continuous improvement. Companies with a strong culture of teamwork and innovation may find Agile methodologies more effective.
Matching Methodologies to Business Scenarios
Aligning methodologies with business scenarios ensures optimal results:
Manufacturing Sector: Lean and Kaizen methodologies have proven successful in manufacturing. Toyota, for instance, popularized Kaizen, focusing on continuous improvement to minimize waste and increase efficiency. This approach remains a core principle in quality management and Lean Manufacturing.
Service Industry: Agile methodologies suit dynamic environments where customer needs frequently change. Service organizations can leverage Agile to enhance responsiveness and deliver value incrementally.
Quality Improvement: Six Sigma's structured approach to reducing defects makes it ideal for businesses aiming to improve quality. By defining, measuring, analyzing, improving, and controlling processes, companies can achieve consistent and reliable outcomes.
Comprehensive Quality Management: Total Quality Management (TQM) offers a holistic approach to improving quality across all organizational processes. Businesses seeking to integrate quality into every aspect of their operations may find TQM beneficial.
By understanding these factors and scenarios, businesses can make informed decisions about which Business Process Improvement Methodologies to implement. This strategic alignment not only enhances operational efficiency but also drives long-term success.
Practical Steps for Implementation
Implementing Business Process Improvement Methodologies requires a strategic approach. Organizations must equip themselves with the right tools and techniques to ensure successful execution. Additionally, they need to anticipate and overcome common challenges that may arise during the implementation process.
Tools and Techniques
Organizations can utilize a variety of tools and techniques to facilitate the implementation of process improvement methodologies. These tools help in analyzing processes, identifying inefficiencies, and implementing solutions effectively.
Value Stream Mapping: This tool helps visualize the flow of materials and information within a process. By mapping out each step, organizations can identify areas of waste and opportunities for improvement.
Root Cause Analysis: This technique involves identifying the underlying causes of problems or inefficiencies. By addressing the root causes, organizations can implement more effective solutions.
Statistical Process Control (SPC): SPC uses statistical methods to monitor and control processes. It helps organizations maintain consistent quality and identify variations that may lead to defects.
Kanban Boards: These visual tools help manage workflow and improve efficiency. By displaying tasks and their progress, teams can prioritize work and identify bottlenecks.
PDCA Cycle (Plan-Do-Check-Act): This iterative method supports continuous improvement. Organizations plan changes, implement them, check results, and act on findings to refine processes further.
Overcoming Common Challenges
Implementing process improvement methodologies can present several challenges. Organizations must be prepared to address these obstacles to achieve successful outcomes.
Resistance to Change: Employees may resist changes to established processes. To overcome this, organizations should involve employees in the improvement process and communicate the benefits clearly.
Resource Constraints: Limited resources can hinder implementation efforts. Organizations should prioritize initiatives based on their impact and allocate resources strategically.
Lack of Expertise: Implementing methodologies like Six Sigma or Lean requires specialized knowledge. Organizations can invest in training programs or hire experts to guide the process.
Cultural Barriers: An organization's culture can impact the success of process improvement efforts. Fostering a culture of continuous improvement and employee involvement can help overcome these barriers.
Measuring Success: Organizations may struggle to measure the impact of improvements. Establishing clear metrics and key performance indicators (KPIs) can help track progress and demonstrate success.
By leveraging the right tools and techniques and addressing common challenges, organizations can successfully implement Business Process Improvement Methodologies. This strategic approach not only enhances operational efficiency but also drives long-term success.
Case Studies and Examples
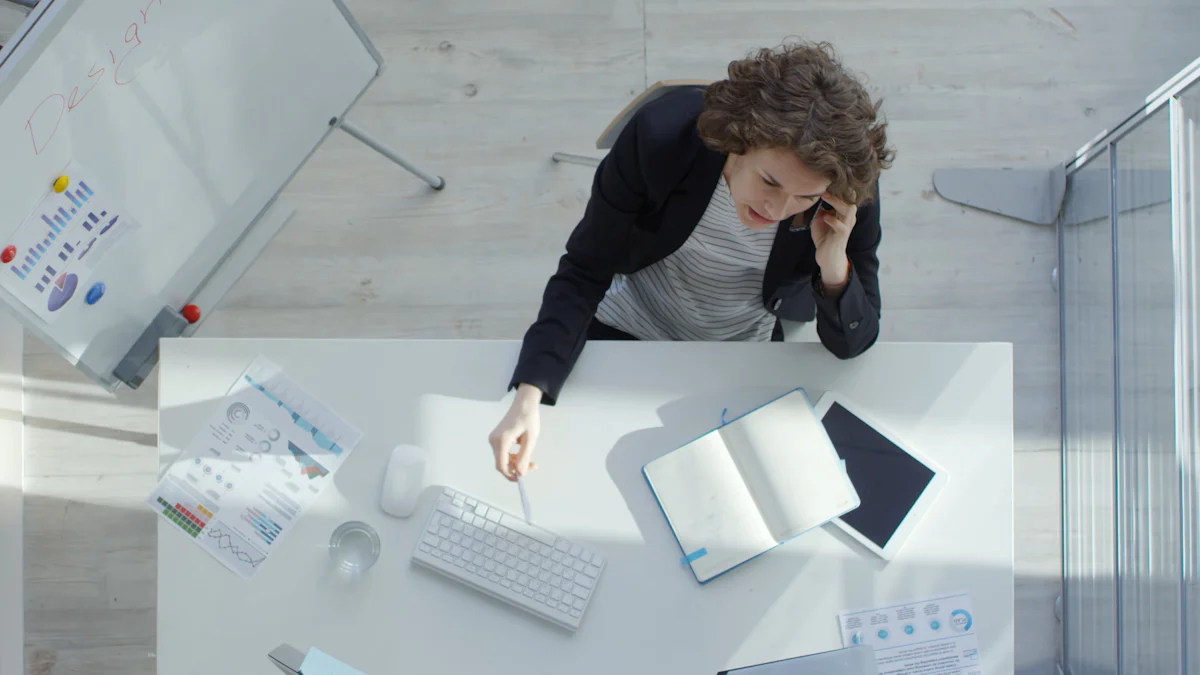
Successful Implementations
Many organizations have successfully implemented Business Process Improvement Methodologies to enhance their operations. One notable example is Lean Six Sigma, which combines Lean's waste elimination with Six Sigma's defect reduction. A manufacturing company adopted this methodology to streamline its production line. By using the DMAIC framework, the company identified bottlenecks and reduced cycle times by 30%. This improvement led to increased productivity and significant cost savings.
Another success story involves the use of Agile in a software development firm. The team embraced Agile's iterative approach to manage projects more effectively. By breaking down tasks into smaller increments, they delivered high-quality software faster. The Agile framework also encouraged collaboration and adaptability, allowing the team to respond swiftly to changing client requirements.
In the service industry, a financial institution applied Data-Driven Agile to enhance customer service. By integrating Six Sigma's data analysis into Agile processes, the institution improved its response time to customer inquiries. The use of metrics and statistical tools guided their sprint planning, resulting in a 20% increase in customer satisfaction.
Lessons Learned
These case studies highlight several key lessons for organizations considering Business Process Improvement Methodologies. First, the importance of aligning methodologies with specific business needs cannot be overstated. Each organization must assess its unique challenges and select the most suitable approach. For instance, manufacturing firms may benefit more from Lean Six Sigma, while service-oriented businesses might find Agile more effective.
Second, the involvement of all employees in the improvement process proves crucial. Engaging staff at all levels fosters a culture of continuous improvement and accountability. This involvement not only enhances the success of the implementation but also boosts employee morale and job satisfaction.
Lastly, organizations should remain flexible and open to adaptation. As seen in the Agile case study, the ability to respond to changing requirements ensures that businesses stay competitive and meet customer expectations. Continuous evaluation and refinement of processes lead to sustained improvements and long-term success.
By learning from these examples, organizations can effectively implement Business Process Improvement Methodologies to achieve their operational goals. For more information on how to apply these methodologies, reach out to our team for expert guidance.
Measuring Success
Key Performance Indicators
Key Performance Indicators (KPIs) serve as essential tools for measuring the success of Business Process Improvement Methodologies. They provide quantifiable metrics that help organizations assess their progress and identify areas for further enhancement. By setting clear KPIs, businesses can track improvements in efficiency, quality, and customer satisfaction.
Efficiency Metrics: These indicators measure how well resources are utilized. For example, a company might track production cycle times or the number of units produced per hour. A reduction in cycle time often signifies successful process improvements.
Quality Metrics: These KPIs focus on the quality of products or services. Businesses may monitor defect rates or customer complaints. A decrease in defects indicates that quality improvement methodologies, such as Six Sigma, are effectively reducing errors.
Customer Satisfaction: This metric evaluates how well a company meets customer expectations. Surveys and feedback forms can provide insights into customer satisfaction levels. An increase in positive feedback suggests that process improvements are enhancing the customer experience.
Employee Engagement: Engaged employees contribute significantly to process improvement. Organizations can measure engagement through surveys or participation rates in improvement initiatives. High engagement levels often lead to more innovative solutions and better problem-solving.
"When employees feel involved in initiatives to improve processes, it fosters a culture of continual learning, innovation, and effective problem-solving."
Continuous Improvement
Continuous improvement is a cornerstone of successful Business Process Improvement Methodologies. It involves an ongoing effort to enhance processes, products, and services. This approach not only boosts efficiency but also fosters a culture of innovation and adaptability.
Employee Involvement: Engaging employees in the improvement process is crucial. Team members who work directly with processes often have valuable insights into inefficiencies. Their contributions can lead to impactful changes that management might overlook.
Iterative Process: Continuous improvement relies on small, incremental changes. Organizations can use tools like the PDCA Cycle (Plan-Do-Check-Act) to implement and refine improvements. This iterative approach ensures that processes evolve to meet changing needs.
Cultural Shift: Fostering a culture of continuous improvement requires a shift in mindset. Employees should feel empowered to experiment and suggest changes. This empowerment leads to a more motivated and proactive workforce.
For example, a gym management software company, Wodify, reduced employee onboarding time by half through process adjustments. This achievement highlights the power of continuous improvement in streamlining operations.
By focusing on KPIs and embracing continuous improvement, organizations can effectively measure and enhance the success of their Business Process Improvement Methodologies. These strategies not only improve operational efficiency but also drive long-term success and competitiveness.
Future Trends in Business Process Improvement
Emerging Methodologies
The landscape of Business Process Improvement Methodologies continues to evolve, with new approaches emerging to address the dynamic needs of modern businesses. Organizations increasingly recognize the importance of documenting and refining their processes. According to a BPTrends survey, there is a growing practice of documenting business processes, which helps in identifying inefficiencies and areas for improvement. This trend underscores the shift towards more structured and systematic approaches to process enhancement.
One emerging methodology is the integration of Artificial Intelligence (AI) into process improvement strategies. A Forbes Advisor survey revealed that 56% of businesses are applying AI tools to enhance operations. AI can analyze vast amounts of data quickly, providing insights that drive more informed decision-making. This capability allows businesses to identify patterns and predict outcomes, leading to more efficient processes and reduced errors.
Another trend is the adoption of hybrid methodologies that combine elements from different approaches. For instance, Lean Six Sigma merges Lean's focus on waste reduction with Six Sigma's emphasis on quality improvement. This combination offers a comprehensive framework for achieving operational excellence. By leveraging the strengths of multiple methodologies, organizations can tailor their process improvement efforts to meet specific goals and challenges.
Technological Advancements
Technological advancements play a pivotal role in shaping the future of business process improvement. Digital tools and platforms enable organizations to streamline operations and enhance efficiency. The use of cloud-based solutions, for example, facilitates real-time collaboration and data sharing across teams. This connectivity improves communication and coordination, leading to faster decision-making and problem-solving.
Automation technologies also contribute significantly to process improvement. Robotic Process Automation (RPA) automates repetitive tasks, freeing up employees to focus on more strategic activities. This shift not only boosts productivity but also enhances job satisfaction by reducing mundane workloads. Additionally, RPA minimizes human errors, resulting in more accurate and reliable outcomes.
The integration of Internet of Things (IoT) devices further enhances process improvement efforts. IoT devices collect real-time data from various sources, providing valuable insights into operational performance. This data-driven approach enables organizations to monitor processes continuously and make adjustments as needed. By leveraging IoT technology, businesses can achieve greater transparency and control over their operations.
In conclusion, the future of Business Process Improvement Methodologies lies in embracing emerging methodologies and technological advancements. Organizations that adopt these trends position themselves for success in an increasingly competitive landscape. By staying informed about the latest developments, businesses can continue to refine their processes and achieve sustainable growth. For more information on how to implement these methodologies, reach out to our team for expert guidance.
Business Process Improvement Methodologies hold immense importance for organizations striving for excellence. They provide structured systems that enhance efficiency and effectiveness. By adopting these methodologies, businesses can streamline operations and reduce waste. This leads to improved productivity and customer satisfaction. The integration of AI and machine learning further enhances decision-making by offering predictive analytics and data-driven insights. Organizations should start applying these methodologies to unlock their potential for improved efficiency and effectiveness. For more information on implementing these strategies, reach out to our team for expert guidance.