Can Six Sigma Methodology Boost Your Business
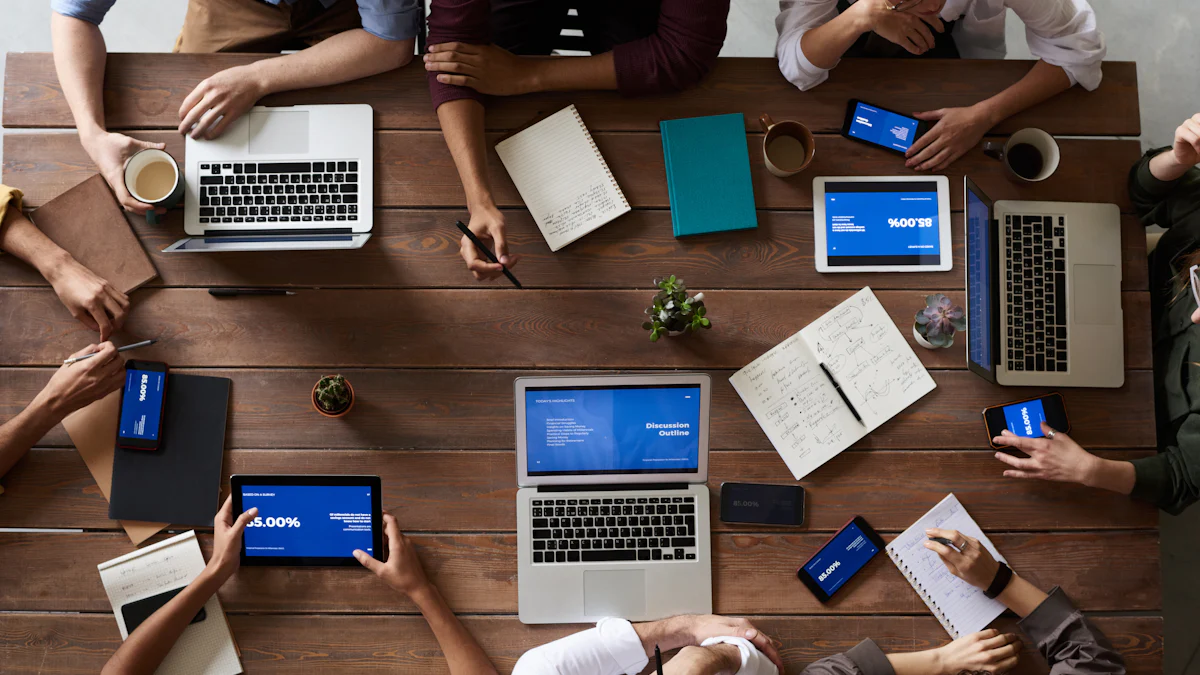
Six Sigma Methodology stands as a powerful tool for businesses aiming to enhance their systems. This approach focuses on reducing errors and improving efficiency, which is crucial for any business striving for excellence. Many Fortune 500 companies have embraced this methodology, with up to 82% of the top Fortune 100 companies integrating it into their systems. By leveraging Six Sigma, businesses can achieve significant cost savings and boost client satisfaction. This blog aims to provide valuable knowledge on how Six Sigma can transform your business operations.
Understanding Six Sigma Methodology
What is Six Sigma Methodology?
Definition and history
Six Sigma Methodology emerged as a powerful tool for improving business processes. It originated in the 1980s at Motorola, where engineers sought to reduce defects in manufacturing. Over time, Six Sigma evolved beyond manufacturing, becoming a universal approach for process improvement across various industries. By the 2000s, companies like Sony, Jaguar, and Samsung adopted Six Sigma globally, refining and standardizing its practices. This methodology focuses on identifying and eliminating defects, ensuring processes meet high-quality standards.
Key objectives
The primary objectives of Six Sigma Methodology include reducing process variation and enhancing quality. Businesses aim to achieve near-perfect processes by minimizing errors and defects. Six Sigma sets a standard of 3.4 defects per million opportunities, emphasizing precision and consistency. Organizations use this methodology to improve customer satisfaction and profitability by streamlining operations and reducing waste. The ultimate goal is to create efficient systems that deliver consistent results.
Core Principles of Six Sigma Methodology
DMAIC Methodology
DMAIC stands for Define, Measure, Analyze, Improve, and Control. This structured approach guides teams through problem-solving and process improvement.
Define: Identify the problem and set clear objectives.
Measure: Collect data to understand current performance.
Analyze: Examine data to identify root causes of defects.
Improve: Develop and implement solutions to address issues.
Control: Monitor changes to ensure sustained improvements.
DMAIC provides a systematic framework for enhancing processes, making it a cornerstone of Six Sigma Methodology.
DMADV Methodology
DMADV, another key component of Six Sigma, stands for Define, Measure, Analyze, Design, and Verify. This methodology focuses on designing new processes or products that meet customer needs.
Define: Establish project goals and customer requirements.
Measure: Gather data to understand customer expectations.
Analyze: Explore options for meeting customer needs.
Design: Develop detailed designs for new processes or products.
Verify: Test and validate designs to ensure they meet objectives.
DMADV complements DMAIC by addressing the creation of new systems, ensuring they align with customer demands and quality standards.
The Relevance of Six Sigma in Business
Why Businesses Need Six Sigma
Addressing Inefficiencies
Businesses constantly seek ways to improve their operations. Six Sigma provides a structured approach to identify and eliminate inefficiencies. By analyzing processes, teams can pinpoint areas where resources are wasted. This methodology helps businesses streamline their operations, leading to significant cost savings. For example, companies can reduce production time by eliminating unnecessary steps, which enhances overall productivity. Six Sigma empowers organizations to operate more efficiently, ensuring they remain competitive in their respective industries.
Enhancing Quality Control
Quality control is crucial for maintaining customer satisfaction. Six Sigma focuses on reducing defects and ensuring products meet high standards. By implementing this methodology, businesses can enhance their quality control processes. Teams use data-driven techniques to identify defects and implement solutions to prevent them. This proactive approach minimizes errors, resulting in higher-quality products. As a result, businesses can build a reputation for reliability and excellence, attracting more customers and increasing profitability.
Industries Benefiting from Six Sigma
Manufacturing
Manufacturing industries have long benefited from Six Sigma. This methodology originated in manufacturing, where it was used to reduce defects and improve product quality. By applying Six Sigma principles, manufacturers can optimize their production processes. This leads to reduced waste and increased efficiency. Companies like Motorola and General Electric have successfully implemented Six Sigma, achieving significant improvements in their operations. The manufacturing sector continues to rely on Six Sigma to maintain high standards and meet customer demands.
Healthcare
The healthcare industry has also embraced Six Sigma to improve patient care. Hospitals and clinics use this methodology to streamline their processes and reduce errors. By analyzing data, healthcare providers can identify inefficiencies and implement solutions to enhance patient outcomes. Six Sigma helps healthcare organizations deliver high-quality care while minimizing costs. This approach ensures that patients receive timely and effective treatment, improving overall satisfaction. As a result, more healthcare institutions are adopting Six Sigma to enhance their services and achieve better results.
Benefits of Implementing Six Sigma

Improved Efficiency
Streamlining Processes
Businesses often face challenges in optimizing their operations. Six Sigma provides a structured approach to streamline processes. Teams identify bottlenecks and eliminate unnecessary steps. This leads to smoother workflows and faster production times. For instance, manufacturing companies have reported significant improvements in efficiency by applying Six Sigma principles. They achieve this by analyzing each step of the production process and removing redundancies. As a result, businesses can operate more efficiently and meet their production targets.
Reducing Waste
Waste reduction is a critical aspect of Six Sigma. By focusing on eliminating waste, businesses can save resources and reduce costs. Six Sigma encourages teams to analyze their processes and identify areas where waste occurs. This might include excess materials, time, or labor. By addressing these issues, companies can minimize waste and improve their bottom line. In manufacturing, for example, Lean Six Sigma has helped organizations reduce material waste and enhance product quality. This approach not only benefits the environment but also boosts profitability.
Reduced Errors
Error Identification
Identifying errors is a fundamental step in Six Sigma. The methodology uses data-driven techniques to pinpoint defects in processes. Teams collect and analyze data to understand where errors occur. This allows them to focus their efforts on the most critical areas. By identifying errors early, businesses can prevent them from escalating into larger problems. This proactive approach ensures that processes remain efficient and reliable. Companies that implement Six Sigma often see a reduction in error rates, leading to higher-quality products and services.
Error Prevention
Preventing errors is a key objective of Six Sigma. Once teams identify the root causes of defects, they develop solutions to prevent them. This might involve redesigning processes, implementing new technologies, or providing additional training. By addressing the underlying issues, businesses can reduce the likelihood of errors occurring in the future. This leads to more consistent outcomes and improved customer satisfaction. Six Sigma's focus on error prevention helps organizations maintain high standards and build a reputation for excellence.
Increased Customer Satisfaction
Meeting Customer Expectations
Meeting customer expectations is essential for business success. Six Sigma helps organizations align their processes with customer needs. By analyzing customer feedback and data, teams can identify areas for improvement. This allows businesses to tailor their products and services to meet customer demands. As a result, companies can enhance their reputation and attract more clients. Six Sigma's emphasis on quality and efficiency ensures that businesses consistently deliver on their promises.
Building Customer Loyalty
Building customer loyalty is a long-term benefit of Six Sigma. By consistently meeting or exceeding customer expectations, businesses can foster strong relationships with their clients. Satisfied customers are more likely to return and recommend the company to others. Six Sigma's focus on quality and continuous improvement helps organizations maintain high standards and build trust with their customers. This loyalty translates into increased sales and long-term success for the business.
Real-World Examples of Six Sigma Success
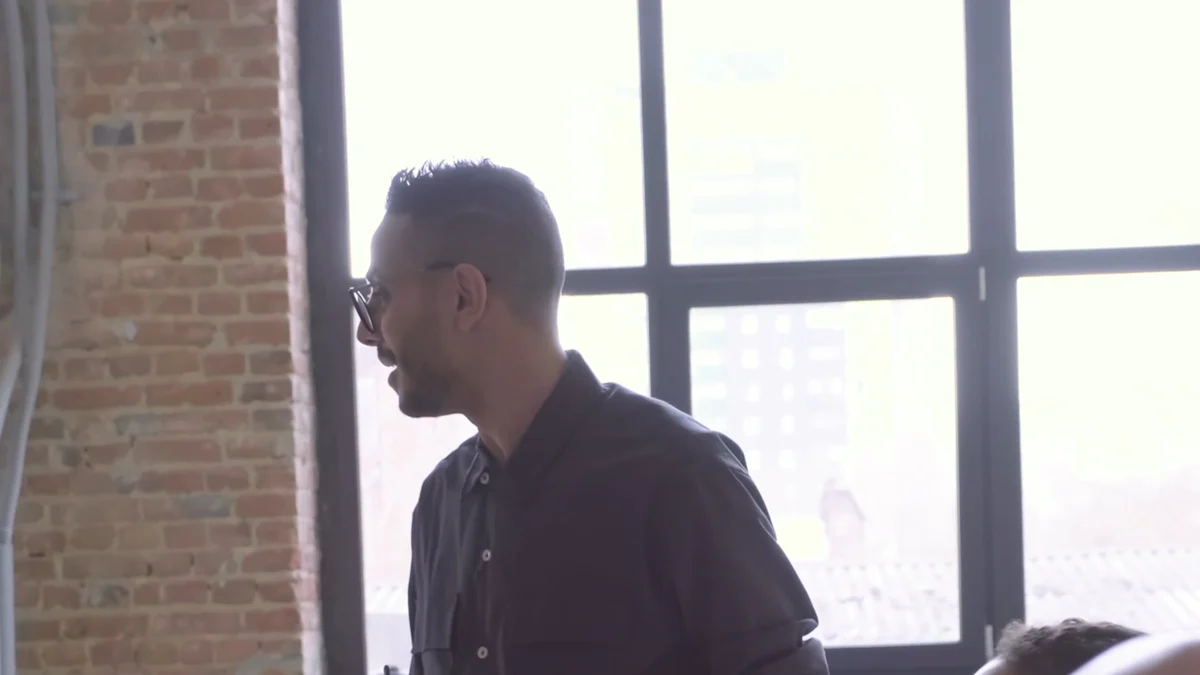
Case Study 1: General Electric
Challenges faced
General Electric (GE) encountered significant challenges in maintaining quality and efficiency across its vast operations. The company struggled with inconsistencies in processes, leading to increased costs and reduced customer satisfaction. These inefficiencies hindered GE's ability to compete effectively in the global market.
Solutions implemented
GE adopted the Six Sigma methodology to address these challenges. The company focused on streamlining processes and reducing defects. Teams at GE implemented the DMAIC approach, which stands for Define, Measure, Analyze, Improve, and Control. This structured method allowed them to identify root causes of inefficiencies and develop targeted solutions. As a result, GE achieved remarkable success, saving an impressive $12 billion over five years. This transformation not only enhanced operational efficiency but also improved product quality, boosting customer satisfaction.
Case Study 2: Motorola
Challenges faced
Motorola, a pioneer in the development of Six Sigma, faced its own set of challenges. The company needed to improve product quality and reduce manufacturing defects to maintain its competitive edge. High defect rates led to increased costs and customer dissatisfaction, threatening Motorola's market position.
Solutions implemented
Motorola's commitment to Six Sigma played a crucial role in overcoming these obstacles. The company developed and refined the methodology, focusing on reducing defects and enhancing process efficiency. Motorola's teams employed both DMAIC and DMADV methodologies to address existing processes and design new ones. This comprehensive approach resulted in substantial improvements, with documented savings exceeding $16 billion. Motorola's success story highlights the power of Six Sigma in driving quality improvements and cost reductions, setting a benchmark for other organizations to follow.
These case studies demonstrate the transformative impact of Six Sigma on business operations. By adopting this methodology, companies like General Electric and Motorola have achieved significant cost savings and enhanced customer satisfaction. Businesses looking to improve their processes can learn from these examples and consider implementing Six Sigma to drive success.
Challenges in Implementing Six Sigma
Common Obstacles
Resistance to Change
Implementing Six Sigma often encounters resistance from employees. Change can feel daunting, especially when it disrupts established routines. Employees may fear the unknown or worry about job security. This resistance can hinder the adoption of Six Sigma practices. To address this, organizations must communicate the benefits clearly. Involving employees in the process helps them understand the value of Six Sigma. Providing adequate training and support can ease the transition and foster a culture of continuous improvement.
Resource Allocation
Allocating resources effectively poses another challenge in Six Sigma implementation. Organizations need to invest time, money, and personnel to ensure success. However, limited resources can strain existing operations. Companies must prioritize projects and allocate resources strategically. This involves assessing the potential impact of Six Sigma initiatives and aligning them with business goals. By doing so, organizations can maximize the benefits of Six Sigma while minimizing disruptions to daily operations.
Overcoming Challenges
Training and Development
Training and development play a crucial role in overcoming implementation challenges. Employees need the skills and knowledge to apply Six Sigma principles effectively. Comprehensive training programs equip teams with the tools they need to succeed. These programs should cover Six Sigma methodologies, data analysis techniques, and problem-solving strategies. Ongoing development opportunities keep employees engaged and motivated. By investing in training, organizations empower their workforce to drive process improvements and achieve long-term success.
Leadership Support
Leadership support is essential for successful Six Sigma implementation. Leaders set the tone for organizational change and influence employee attitudes. They must champion Six Sigma initiatives and demonstrate commitment to the process. This involves providing resources, setting clear expectations, and recognizing achievements. Leaders should also foster a culture of collaboration and open communication. By doing so, they create an environment where employees feel valued and motivated to embrace Six Sigma practices.
"When applied rightly, Six Sigma, without any doubt, can make processes more efficient," says an expert in Six Sigma Implementation Challenges. "But, its implementation comes into the hands of people." This highlights the importance of addressing human factors in Six Sigma adoption. By focusing on training and leadership support, organizations can overcome obstacles and unlock the full potential of Six Sigma.
How to Get Started with Six Sigma
Initial Steps
Assessing Business Needs
Businesses must first assess their needs to effectively implement Six Sigma. This involves identifying areas where improvements can enhance efficiency and quality. Teams should conduct a thorough analysis of current processes to pinpoint inefficiencies and defects. By understanding these challenges, organizations can tailor Six Sigma strategies to address specific issues. This initial assessment sets the foundation for successful implementation, ensuring that efforts align with business objectives.
Setting Goals
Setting clear goals is crucial for guiding Six Sigma initiatives. Organizations should define what they aim to achieve through this methodology. Goals might include reducing defects, improving customer satisfaction, or increasing profitability. Clear objectives provide direction and motivation for teams, helping them focus their efforts on achieving measurable results. By setting specific, achievable goals, businesses can track progress and celebrate successes along the way.
Choosing the Right Six Sigma Tools
Selecting Methodologies
Choosing the appropriate Six Sigma methodologies is essential for addressing business needs. DMAIC and DMADV are two primary approaches that cater to different aspects of process improvement. DMAIC focuses on enhancing existing processes, while DMADV is ideal for designing new ones. Organizations should evaluate their goals and challenges to determine which methodology best suits their needs. By selecting the right approach, teams can effectively tackle inefficiencies and drive improvements.
Utilizing Software
Software tools play a vital role in supporting Six Sigma projects. Various applications assist teams in data analysis and process optimization. For instance, MiniTab and SixNet Intelligence offer robust features for statistical analysis and data visualization. These tools help professionals identify patterns and variations in processes, enabling them to implement corrective measures. Additionally, the Six Sigma calculator provides quick calculations for key metrics, streamlining decision-making. By leveraging these software solutions, organizations can enhance their Six Sigma efforts and achieve better outcomes.
"Histograms are the visual representation of data’s frequency distribution," explains a Six Sigma expert. "With this tool, professionals can quickly and easily identify variations in graph form." This highlights the importance of using the right tools to support Six Sigma initiatives. By integrating software and methodologies, businesses can effectively address challenges and unlock the full potential of Six Sigma.
Future of Six Sigma in Business
Emerging Trends
Integration with Technology
In the evolving landscape of business, Six Sigma must embrace advanced technologies to stay relevant. Teams now integrate tools like artificial intelligence, machine learning, and data analytics into their systems. These technologies provide predictive insights, allowing businesses to anticipate issues before they arise. By leveraging these tools, Six Sigma enhances its ability to drive process improvements. This integration not only streamlines operations but also ensures that businesses remain competitive in a tech-driven world.
Global Adoption
Six Sigma's principles have transcended borders, finding applications in diverse industries worldwide. As businesses globalize, the demand for standardized quality improvement methodologies grows. Six Sigma offers a universal framework that organizations can adapt to various cultural and operational contexts. This global adoption reflects the methodology's flexibility and effectiveness. Companies across continents recognize the value of Six Sigma in enhancing efficiency and quality, leading to its widespread implementation.
Long-term Impact
Sustaining Improvements
Sustaining improvements remains a core focus of Six Sigma. The methodology emphasizes continuous monitoring and control to maintain gains achieved through process enhancements. Teams use data-driven approaches to ensure that improvements are not only implemented but also sustained over time. This commitment to ongoing excellence helps businesses avoid regression and maintain high standards. By embedding Six Sigma into their systems, organizations create a culture of continuous improvement that drives long-term success.
Continuous Innovation
Innovation is at the heart of Six Sigma's long-term impact. The methodology encourages teams to explore new ways of solving problems and improving processes. By fostering a mindset of innovation, Six Sigma helps businesses adapt to changing market demands. This proactive approach ensures that organizations remain agile and responsive to new challenges. Continuous innovation, supported by Six Sigma, enables businesses to stay ahead of competitors and deliver exceptional value to customers.
"The future of Lean Six Sigma is likely to be dynamic and evolving," notes a study on Six Sigma's trends. "With continued integration into digital transformation efforts, expansion into new industries, and emphasis on sustainability and innovation." This highlights the importance of embracing change and innovation in Six Sigma's journey.
Six Sigma offers numerous benefits to businesses, including improved efficiency, reduced errors, and increased customer satisfaction. Many organizations have experienced significant enhancements in their processes and products by adopting this methodology. As a result, they have seen increased productivity and profitability.
Experienced Six Sigma professionals highlight that "53 percent of Fortune 500 businesses use Six Sigma to save an estimated $427 billion." This demonstrates the methodology's effectiveness across various industries.
Business leaders should consider integrating Six Sigma into their operations to achieve similar success. By doing so, they can streamline processes and enhance quality, ultimately boosting their competitive edge.